5 Reasons Why Your IIoT Network Needs Wireless Programmability
If your company is grappling with the shift towards wireless connectivity and automation, you’re certainly not alone. As more processes are automated, especially within industrial markets like oil and gas or utilities, data has become a valuable asset that provides critical information for operations and performance. Up and coming industry leaders are pushing for modern Industrial IoT (IIoT) networks, as the older, more traditional workforce heads towards retirement. As a result, the processes of yesterday are being phased out – especially when it comes to choosing between hardwire and wireless for remote deployments. For many, wireless solutions have been accepted for some time as the primary means in which data is collected, transported and analyzed. Frequency Hopping Spread Spectrum (FHSS)-based technology in particular is proven to be a reliable and maintainable wireless option. Now, however, we are facing an entirely new realm of opportunity with FHSS-based programmable wireless technology that is molding the future of data collection. Here are five reasons why you need to consider programmable wireless technology for your IIoT network: Bring it all to the Cloud – Programmable wireless solutions are equipped with the ability to incorporate custom, third party applications at the Edge. When we talk about the Edge, we essentially mean the outermost layer of the network. For industrial networks, the Edge is often a remote area where mission critical operations occur. In order for the business to capture a holistic view of their entire network, many have added sensors and other data-capturing devices at the Edge. By adding third party applications with new programmable wireless technology, businesses are able to expand automation capabilities, reduces costs, simplify operations and enable data transmission directly to a private or public cloud. Smart Data Over Big Data – The goal of achieving ‘Big Data’ is common practice in most modern IoT and IIoT networks. Decision makers recognize the power of data and know they need to receive it from every network end-point. We’ve seen this to be true purely in the proliferation of sensors and IoT devices deployed across the U.S. that continues to grow. Having programmability at the edge of the network offers a big advantage, because you have the ability to control of the quality of the data. Even better than Big Data is access to the specific, timely data that is most pertinent to your business operations. Robust and Reliable Technology: Programmable wireless solutions are equipped to embrace the future of data collection. The beautiful thing about these solutions is that the backbone of the technology is FHSS. This particular Radio Frequency (RF) technology has been proven in some of the most adverse conditions imaginable. These technologies are trusted by the government to maintain their links and have proven to operate in some of the most dreadful and intense environments in the world . Where performance is critical – these solutions have proven to work for decades and now programmable options can reliably bring this data directly to the cloud. Flexible and customizable– We are all privy to the fact that no two networks are the same. With programmable options, radio functionality is customizable to the specific needs of the network. Despite the variances, remote networks likely have one thing in common – data needs to be transported across significant distances. Programmable wireless technology is built to be deployed at nearly any point in the network where sensors are collecting data. This is an area in which traditional hardwire solutions almost always fall short, as most businesses cannot afford the cost of running hardwire to these remotes sites. Besides, there are wireless options that are built for easy installation and long-range communications that simply make the most sense for remote deployments. Meeting Modern Demands– Today, IT and OT departments are one in the same. These modern networks eliminate barriers which is conceptually great for operations. However, like any major disruption, convergence has created a number of challenges from visibility, to cultural difference, to security. To ease some of these tensions, modern wireless solutions are designed to drive connectivity for the entire network, and are even able to tie in legacy systems from the field. Many FHSS-based technologies offer secure-data transmission, and by leveraging the programmable wireless technology, and you can bring data to the cloud. Wireless technology is recognized as a necessary solution for remote operations. As IIoT networks mature, there are stark advantages in leveraging programmable solutions. Not only do they rack up cost savings and streamline operations, but they are deployed at the edge of the network with minimal hassle and are built to deliver in any environment.
Remote Tank Level Monitoring and Automation
Industrial livestock operations have several critical needs in order to function smoothly, but perhaps most important is also the most fundamental: water. On remote sites, tank level monitoring and automation are tools that can essentially make or break the entire operation. In many of these situations, the needs of the site managers are different, so in order to maximize the technology being deployed to drive the automation process, they need to be able to customize the functionality. For operations using radio communication networks, those radios need to provide maximum programmability in order to host third party applications specific to the needs of the site managers. We recently finished a deployment that serves as an excellent case study for remote site tank monitoring deployments and included some interesting uses of radio programmability: The operator of a Rocky Mountain based livestock facility approached FreeWave to assist in remote data visualization of water tanks that are vital to its operations. The pain point was that the tank levels could only be observed visually on premise. After consideration of the terrain (mountainous, remote and big temperature swings), sensors and communications infrastructure, FreeWave engineers recommended ZumLink IPR with the Node-RED programming language for intelligent tank data visualization via browser or mobile device. The facility has minimal to zero staff most of the time. If a fault occurs such as a leak that prevents a tank from filling, the facility operators are unaware until they visually inspect the remote faulty tank, located a half mile from property headquarters. The operators wanted to reduce the number of trips to the tank facility and remotely monitor all tanks via web-based browser or mobile device. For the complete case study, visit this link: https://www.freewave.com/case-studies/remote-tank-monitoring-automation/.
Happy Independence Day!
As we prepare for fireworks, barbeques and all of the excitement that comes along with tomorrow’s holiday, we’d also like to recognize what Independence Day means to the U.S. By definition it’s the celebration of the Declaration of Independence and the birth of our incredible country as an independent nation. On this holiday, we’re also reminded that millions of people have sacrificed (and continue to sacrifice) in order for us to gain and retain our freedoms and liberties. As a company that has had the honor of working in the military and defense industry for more than two decades, we are humbled and grateful to all of the men and women in the armed forces. From the bottom of our hearts, with respect and admiration, we’d like to thank all of brave men and women who have served and sacrificed for this great country — including those who are currently serving today. FreeWave and the Military The government and defense industries have been woven into FreeWave’s story from early on. As previously noted, we have worked in the defense markets for more than two decades providing wireless communication solutions – including command and control (C2) links for unmanned systems. Our embedded communication solutions for drones and robotics have logged more than 2.5 million flight hours without a single link failure. As the number of unmanned systems for air, land and water increases, it is imperative for manufacturers and operators to use rugged, reliable and secure C2 solutions with high-speed data transmission. We are dedicated to continuing to provide robust and trusted solutions. Not only do we focus on providing a great technology, but a solution that can be trusted to operate when human lives are at stake. We hope you have a wonderful Fourth of July holiday!
7 Tips for OEMs to Improve SCADA Networking Communications
From remote field sensors to Supervisory Control and Data Acquisition (SCADA) and I/O modules, industrial wireless radios connect your device and sensor ecosystems with robust and reliable links. Furthermore, wireless data radio networking technology connected to I/O modules for SCADA applications have become faster, smarter and their firmware now easier to upgrade. More options and frequencies, including 2.4 GHz for short range I/O and 900MHz for long range data networking, continue to improve SCADA-based network communications for robotics, industrial automation, unmanned systems and heavy machinery. So what do Original Equipment Manufacturers (OEMs) need to know when deciding upon which technology to use? Below are seven tips for OEMs to consider when reviewing industrial wireless communication options. 1) Assess Technology Options for the SCADA Network Start first by identifying your needs, goals, and limitations. When it’s time to research technology options, observe what’s available today and what’s going to be available in the future, heeding the “buyer beware” saying. Communication products vary in many ways, and each manufacturer and/or technology has advantages and disadvantages. No single product—and likely not a single manufacturer—can meet all application needs. 2) Reduce Costs While some companies seek to continue to preserve existing investments of wired and wireless technologies, wireless options have clear advantages for SCADA systems. Most obviously, wireless installations reduce labor and material costs by avoiding hard-wiring remote assets. Speed of deployment adds savings. Wired systems can take days or weeks to be properly installed. Wireless networks generally require only the end points to be installed, saving substantial time and costs. Networks need to scale gracefully as the number of end points increases. After installation savings, scalability is the biggest advantage of wireless over hard-wiring, including slow integration into wired systems as it’s implemented. 3) Consider Hybrid Benefits Toss out any old perceptions. If you need mobile SCADA network access, find somebody that offers it. If you have a microwave tower place, use it. Piggyback slower licensed radio networks with faster 902-928 MHz frequency hopping, AES encrypted networks. Know that you can install I/O capable radios (analog and digital signal, 4 to 20 and 1 to 5) to relay contact closures or other data without adding a new Progammable Logic Controllder (PLC) or Remote Terminal Unit (RTU). 4) Maximize SCADA System Value With telemetry technologies, such as spread spectrum radios, the same radio used in RTUs can act as a slave device sending data back to the SCADA host, and as a repeater to other field devices or other RTUs. This allows almost limitless network expansion by using remote sites as a series of repeaters, and by using radios in the RTUs to poll the instrumentation. Polling the instrumentation creates a second network reporting wirelessly back to the RTU. This shorthaul network is the equivalent of a local area network (LAN). 5) Don’t Use a Proprietary SCADA System By using a non-proprietary SCADA system, users gain real-time access, control, and monitoring of their network (including all the devices and functions of their network). They can manage requirements of an ever-growing system allowing them to manage their network in real-time with fewer bodies and hours invested. Security and safety improves with better monitoring. For instance, some industrial systems don’t contain a process for monitoring the cathodic integrity for corrosion (like in water/wastewater and oil and gas) to avoid disaster. But with deployment of a wireless system, they can. They can begin by monitoring simple things, such as pump stations at wells, using I/O radios communicating back to the central SCADA system to get up-to-date information on the tanks’ or pipelines’ status. End users can more quickly resolve an emergency wirelessly, instead of manually. 6) Seek SCADA System Flexibility Advanced flexibility of radio communications offers benefits to new SCADA system deployments and upgrades performance of existing SCADA systems. For example, in water/wastewater industrial applications, there need to be generation/distribution, lift stations, system monitoring, and treatment facility systems in place (or planned) to meet the expanding growth of a community’s population and/or service areas to meet future requirements. Each year, many industries deploy more frequency hopping spread spectrum (FHSS) SCADA solutions to help monitor and manage critical infrastructure. Several manufacturers (including FreeWave Technologies) offer FHSS radios capable of retrieving data from remote locations. And although wireless IO (input/output) has been available, only recently have both capabilities been offered in one communication solution. 7) Seek Easy-to-Use SCADA Software OEMs implementing and using a SCADA network systems for data communications want a simplified, rapid setup and easy management of a network. That includes ability to manage multiple frequencies and multiple networks within one system. A centralized storage and management center provides easy access to system configuration and diagnostics data. Technicians in remote or harsh weather environments need robust reporting capabilities. Software like FreeWave’s ToolSuite can manage data communication diagnostics and configuration.
Connected Oil Fields in Peru
China National Petroleum Corporation (CNPC) is one of the largest energy companies in the world with operations in 28 countries. In May 2017, CNPC announced it would invest $2 billion in an oil and natural gas block in the southern part of Peru. Beyond the recent investment, CNPC has had a presence in Peru for more than 20 years, including oil fields in the northern portion of the country. To optimize operations in 2009, CNPC ran a pilot test in Piura, Peru to find the ideal communication solution for monitoring, collecting and transporting data. Piura is a coastal city located near the equator where the average temperatures hover around 95 degrees Fahrenheight. To connect the oil fields into the Supervisory Control and Data Acquisition (SCADA) system, CNPC needed a communication technology built to withstand harsh weather, such as high temperatures, large amounts of rain, wind and a variety of other environmental factors. The goal of the pilot was to have several test sites reporting to a gateway and then into a SCADA system to monitor several pumping devices and equipment including: Pump of Controller (POC), Pump Cavity Progressive (PCP), Balance Oil Recovery System (BORS) and plunger lift. FHSS for Oil and Gas In the Piura test case, the distances between links weren’t long, but depressions, canyons and steams made line-of-site (LOS) a challenge. CNPC, who tested multiple Machine-to-Machine (M2M) communication solutions in Piura, found that FreeWave’s Frequency Hopping Spread Spectrum (FHSS) technology solutions offered the most reliable connectivity in comparison to other solutions used during the test. FreeWave solutions also use repeaters that helped establish and maintain connectivity despite the lack of LOS. Additionally, the links were established easily and fast in comparison to other solutions that were a part of the test. During the entire three-month pilot, the FHSS-based M2M solutions did not lose communication or the ability to send data to the SCADA system. Industrially hardened, ruggedized FHSS technology has proven to be reliable in in many oil and gas installations around the world. As the Industrial IoT (IIoT) drives connectivity, we continue to see the demand for reliable communication links in environments like Piura that can have challenging conditions. FHSS technology offers not only a reliable, easy to install communication link, but it easily integrates into today’s modern IIoT networks. To get the full story about the test sites in Piura, read the case study: https://www.freewave.com/case-studies/china-national-petroleum-company/
IIoT Top News — Security Remains Top of Mind
Cybersecurity has been top of mind for industry experts and consumers alike. The WannaCry ransomware is putting a legitimate scare into affected companies, although many are apparently preparing to call the hackers’ bluff. Yesterday, another cyberattack was announced as well, and it has the potential to be far more lucrative for the developers. The common denominator between the two? A leaked exploit developed by the NSA that leverages a Windows file-sharing protocol. These attacks are indicative of the long-term game of cat and mouse that the government and private enterprise faces for the foreseeable future of security and counterintelligence. Moving forward, the growing network of connected devices for the Industrial Internet of Things (IIoT) faces similar security threats. This week, we found several stories demonstrating some of the solutions surrounding those potential security issues. The 9 Best Practices for IIoT from a Dell Security Expert At a recent presentation for 2017 Dell EMC World Conference, Rohan Kotian, Dell EMC’s senior product manager for IoT security, spoke about his nine best practices for improved IIoT security. His number one strategy? Simply understanding the concerns. Many IoT devices come out of the box with few security controls in place, and understanding the risk is the most important step in addressing them. In this article from Tech Republic, you can read Mr. Kotian’s other nine best practices, including studying the attack trends, classifying risk, and leveraging fog computing. IIoT Market Expected to Approach One Trillion Dollars by 2025 Grand View Research writes that the industrial Internet of Things will experience explosive growth over the next decade, going from a $109 billion industry in 2016 to an expected $933.62 billion by 2025. The massive market increase will be driven by a number of factors, one of which continued investment by government agencies and corporate leaders. As the report states, “The role of the Internet of Things (IoT) is increasingly becoming more prominent in enabling easy access to devices and machines. Government-sponsored initiatives and innovative efforts made by key companies, such as Huawei, GE, and Cisco, are anticipated to enhance the adoption of IIoT worldwide over the forecast period.” IIoT Presents Unique Security Challenges Security is always a top priority in the Internet of Things, but IIoT applications present unique challenges. In this article from CSO Online, Phil Neray, CyberX’s vice president of industrial cybersecurity, writes that despite the growth of IoT applications in oil, gas, electric, and pharmaceuticals, “The fact is that all of these devices were designed a long time ago.” That means IIoT innovators have the challenge of integrating the newest technology into systems that may be decades old. This sort of retrofitting can make security a real challenge and there are few experts available who have both the knowledge of legacy systems and the latest IIoT solutions. Sprint to Deploy LTW Cat 1 by End Of July The Internet of Things relies heavily on low-power communication protocols to perform, so a recent announcement on FierceWireless.com that Sprint will be releasing LTE Cat 1 by the end of July is music to IoT developer’s ears. LTE Cat 1 is designed to support low-power applications on the Sprint network such as vehicle telematics and industrial IoT applications. “As one of the leading enablers and solution providers of the internet of things, Ericsson believes in its power to transform industries and capture new growth,” said Glenn Laxdal, head of Network Products for Ericsson North America. “Ericsson looks forward to partnering with Sprint to deploy Cat M1 next year and bring the transformative power of IoT to the Sprint Nationwide network.” The announcement also noted that Cat M would be following in mid-2018. TE Cat M1 and LTE Cat NB1 will support other applications requiring ultralow-throughput and power consumption.
FreeWave at AUVSI Xponential – Booth #3142
AUVSI XPONENTIAL 2017 is just around the corner and we couldn’t be more excited! Unmanned systems from some of the industry’s leading technology providers will be on display, and we’re looking forward to putting our embedded systems solutions out there as well (booth #3142). It’s a potentially transformative time for the unmanned systems industry. As military spending budgets increase, along with the adoption of unmanned systems for air, land and water, manufacturers and operators will need rugged, reliable and secure C2 solutions with high-speed data transmission. Reliability and security are two extremely critical factors in the ongoing development of unmanned systems solutions, especially for commercial deployments. For years, the government and defense industry has been on the forefront of secure unmanned systems, but as the commercial sector begins to utilize unmanned technology, the ability to ensure secure command and control can be the difference between reliable industry operations and serious injury. Clearly, security considerations for unmanned systems are going to be an ongoing hot topic at XPONENTIAL and into the future. We have spent the past 20 years supplying secure, rugged and reliable embedded solutions for government and defense, precision agriculture and beyond, and as a result, we hold a firm belief that the unmanned systems solutions providers for the next generation need to be hyper-vigilant with regard to the industry. With that in mind, we will be offering demonstrations of our latest C2 solutions for unmanned systems at XPONENTIAL this year. Booth attendees will get a first-hand look at our solutions, offered in a small form factor ideal for drones and robotics that have logged more than 2.5 million flight hours without a single link failure (https://www.freewave.com/unmanned-systems-drones-robots/).
A ‘Heads Up’ on Drone Safety
We all know that what goes up must come down. In the case of drones falling out of the sky, hopefully your head isn’t in the collision path. Drones are becoming increasingly popular for commercial and recreational purposes. According to a recent FAA report, this has sparked an “increase in accidents resulting in blunt impact or laceration injuries to bystanders.” The report, released late last month, generated a fair share of news coverage. It examines the dangers of drone collisions with people on the ground, the risk of injury and ways to reduce those risks. The good news, and probably most newsworthy conclusion, is that if a small drone were to hypothetically fall from the sky and collide with your head, you probably won’t die. One of the tests conducted during the study included dropping a drone on the head of a crash test dummy. The drone used in the test represented a typical drone — a Phantom 3, which weighs about 2.7 pounds. Test results determined that a drone causes significantly less damage than a wood block or steel debris. Findings also showed that the “drag,” caused by air resistance slowed the drone down much more than the wood and steel. A USA Today article reported that while there was only a 0.01 to 0.03 percent chance of a serious head injury, but there was an 11-13 percent chance of a serious neck injury. While the risk of serious injury might be lower than expected, both drone manufacturers and operators of remotely piloted aircrafts can continue to actively take responsibility for the risks by operating from a preventative and safety-focused perspective. A combination of proper training, education and reliable, secure command and control links (C2) can lead each side to a safer drone environment. Knowing the Rules Groups have formed with commercial drone safety in mind. Know Before You Fly is an organization dedicated to educating drone operators on the FAA guidelines for operation. They also offer resources on how to safely and responsibly operate unmanned aircraft systems (UAS). The FAA report also names Academy of Model Aeronautics (AMA), Association of Unmanned Vehicle Systems International (AUVSI), and the FAA as groups dedicated to educating hobbyist and commercial UAS users on the important requirements for piloting UAS. New drone operators who leverage the assortment of educational tools available can help champion the pursuit of responsible drone operations. Building Drones with Reliability and Safety in Mind In addition to training and education from the operator perspective, when the right command-and-control (C2) solution is in place, drone operations can become much more safe and reliable. Secure wireless data communication solutions that leverage data encryption capabilities, adhering to FIPS and AES standards, are already heavily relied on for mission-critical government and defense applications. Additionally, certain types of wireless solutions, like Frequency Hopping Spread Spectrum Technologies (FHSS) are secure in their nature. For example, frequency-hopping techniques can leverage coordinated, rapid changes in radio frequencies that literally “hop” in the radio spectrum, thus evading detection and the potential of interference Some wireless products also can deliver multiple user-defined cryptography keys (as many as 32 user-defined keys in some cases), providing more robust link security by allowing the automatic and frequent changing of cryptographic keys. In addition to secure data, these solutions also offer distance. There are FHSS radio solutions that can transmit more than 60 miles Line-of-Sight (LOS). When the communication links are robust and prevent interference, they are much less likely to be jammed or disrupted, ultimately preventing drone performance issues (i.e., falling from the sky). This is a very important consideration because of the growing number of unmanned vehicles operating in industrial and commercial sectors today. With a secure and reliable wireless C2 link, these technical issues are substantially reduced. Drones have opened the door for many hobbyist and commercial opportunities, but that also means there are more inexperienced operators. If an operator educates themselves on the FAA guidelines and safety procedures when operating a drone, and the manufacturers build in a secure and reliable C2 link that works over long distances, then both are taking the steps to decrease drone-related injuries. Although the FAA report shows the risk of serious injury and death is low, manufacturers and operators still need to keep safety a top priority.
British Antarctic Survey Leverages Ruggedized Data Transport
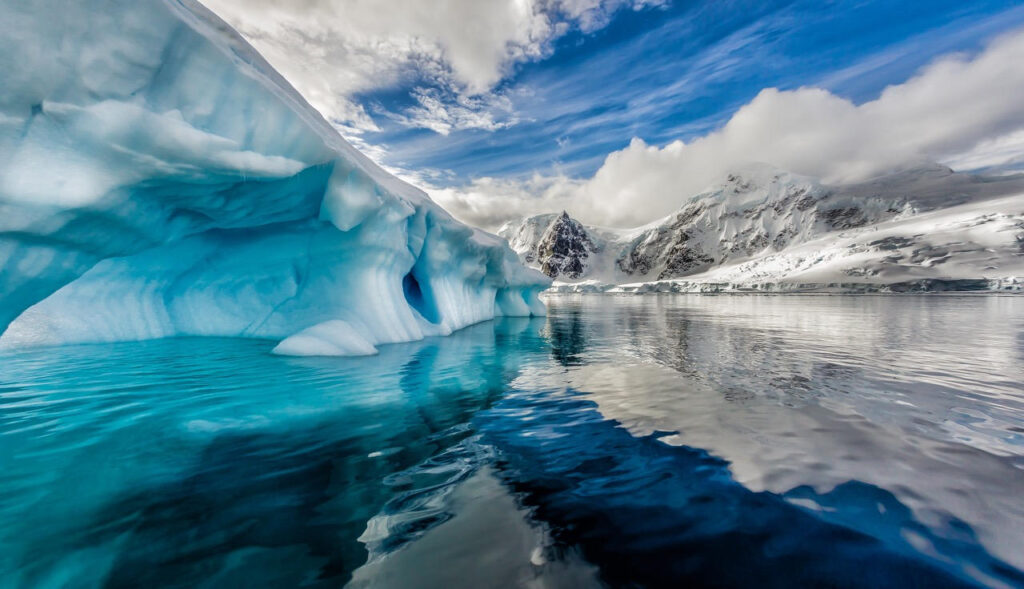
Antarctica inhabits a unique place in the human exploration mythos. The vast expanse of uninhabitable land twice the size of Australia has birthed legendary stories of human perseverance and cautionary tales about the indomitable force of nature. However, since those early years, Antarctica has become a rich research center for all different kinds of data collection – from climate change, to biology, to seismic and more. And although today there are many organizations with field stations running this data collection, the nature of its, well, nature still presents daily challenges that technology has had a hand in helping address. Can You Send Data Through Snow? British Antarctic Survey (BAS) – of recent Boaty McBoatface fame – has been collecting data from its field station network for more than 60 years. Over that time, BAS has become a global leader for polar science and polar operations, collecting data on sediments, ice cores, the polar atmosphere and the ever-changing ice shelves – all of which are vitally important for helping predict the climate of the future. To collect this data, BAS required a network that could reliably transmit it in what could be considered one of the harshest environments on the planet. This means deploying GPS equipment, motion and atmospheric sensors, radios and more that could stand up to the daily tests. In order to collect and transport the data in this harsh environment, BAS needed a ruggedized solution that could handle both the freezing temperatures (-58 degrees F in the winter), strong winds and snow accumulation. Additionally, the solution needed to be low power due to the region’s lack of power infrastructure. The Solution BAS found that FreeWave’s 900 MHz radios could handle this myriad of requirements. The organization deployed 19 radios across its network, each connected to a remote GPS station containing sensors that track the movement of the Brunt Ice Shelf near one of the primary research stations. The GPS sensors determine the Shelf’s position and dynamics before sending the data back to the station. There are several other specs that make the deployment of these radios operationally viable for British Antarctic Survey, but to find out more check out our case study with all the details: https://www.freewave.com/case-studies/british-antarctic-survey/!
FreeWave Named as One of “20 Most Promising Wireless Solution Providers 2017”
Today, CIO Review published it’s list of the “20 Most Promising Wireless Solution Providers 2017,” and FreeWave is excited to be included in that list along with many other notable industry leaders! CIO Review writes, “FreeWave delivers best-in-class wireless platforms for secure and cost-effective control, transport and collection of IIoT data.” Among other companies included in this report are Qualcomm, Mojo Networks, Brocade Communication Systems and NetGear. For the last two years, we have focused our new product engineering on developing a comprehensive collection of communication platforms, an Industrial IoT programmable radio (IPR), ruggedized WiFi platforms, and products with mesh networking and frequency hopping spread spectrum (FHSS) capabilities. In the last year, we’ve announced several new products designed to service a wide range of IIoT applications, including a pilot program for our IPR where third parties can develop proprietary IIoT apps for Edge and Fog Computing. Join the ZumLink IPR Pilot Program today! https://t.co/bWVQM8Arun #IIoT #IoT #programming #AppDev #Wireless pic.twitter.com/Km06N4nukK — FreeWaveTechnologies (@freewavetech) April 5, 2017 It’s been an exciting 2017 so far, and we’re excited for what the future holds, both for FreeWave and for the IIoT industry as a whole!