Friday Top 5 IIoT News Roundup
It’s time to nominate our Friday top five Industrial IoT news articles of the week. Much like the weather in Boulder this week, we couldn’t decide on just one vertical focus, so we cast a wide net of IoT topics. In this week’s roundup, you’ll find a splash of fog computing, manufacturing, smart grid, security and overall IoT updates. Dive in and see if you agree with our picks. Don’t miss the Friday bonus at the end of this short roundup. Making fog computing sensors clearly reliableBy @Patrick_Mannion | Published on @ednmagazinehttp://www.edn.com/design/sensors/4442602/Making-fog-computing-sensors-clearly-reliable“As fog computing rolls in, the onus is upon designers to figure out how much intelligence should be at each node of the system for optimal performance. This implies then that sensors will need to start being more intelligent, with some level of built-in processing, storage, and communications capability.” Army needs wide-area electro-optical sensors for manned and unmanned aircraftBy @jkeller1959 | Published on @IntelligentAerohttp://www.intelligent-aerospace.com/articles/2016/08/ia-wami-sensors.html“Army researchers are interested in moderate-resolution persistent-surveillance electro-optical sensors that operate during the day and at night over large areas to detect vehicles and people on foot. Researchers want to develop a sensor that consists of an imaging sensor, as well as a storage and processing unit.” Five essential IIoT DefinitionsBy @MMS_MattDanford | Published on @MMSOnlinehttp://www.mmsonline.com/blog/post/5-essential-iiot-definitions-“The idea is not just to exchange and collect data, but to act on that data to make things better. (One commonly cited example is a “smart” thermostat.) IIoT is the same concept applied to industry. Examples range from “smart” buildings and power grids to “smart” transportation networks. IIoT might initially take the form of a machine tool status monitoring system.” What makes a grid smart?By David Shadle | Published on @tdworldmaghttp://tdworld.com/grid-opt-smart-grid/what-makes-grid-smart“My point, however, is that the critical consideration is not the number of sensors, controls or data storage components we add to our system when we decide to move ahead with smart grid applications. The focus also needs to be on mastering the integration of these systems, many times across traditional IT and OT lines, to allow them to achieve their potential for intelligence.” Top ten security predictions through 2020By @Gartner_inc | Published on @Forbeshttp://www.forbes.com/sites/gartnergroup/2016/08/18/top-10-security-predictions-through-2020/#4d8ba8073cbe“Through 2018, more than 50% of Internet of Things (IoT) device manufacturers will not be able to address threats from weak authentication practices.” Friday Bonus! FreeWave Technologies announces partnership with Solis Energy By @SolisEnergy and @freewavetech | Published on @SolarNovus http://www.solarnovus.com/freewave-technologies-announces-partnership-with-solis-energy_N10256.html “Both companies are excited about the partnership and are already working through high profile opportunities to take advantage of the growing demand for smart systems and industrial connectivity.”
(Industrialized) IoT App Development
Has IoT app development begun to take the globe by storm? A few weeks ago we discussed the growing need for more third-party app creation for the Industrial IoT industry. This week, we dive deeper and focus on those early adopters of industrialized IoT app development and what industries these “bleeding edgers” are serving. We all know by now the number of connected things is projected to grow massivelyover the coming years. Injecting new software applications into the industrial IoT world creates even more monitoring, control and usage of devices and data at the edge. Some would call this influx of software with industrialized hardware a modern marriage. The manufacturing sector, for example, seems to have found a use for implementing next-generation hardware to improve and automate operations, especially along the assembly line. At the same time, cloud-based software solutions are being leveraged to improve data analytics, thus improving actionable intelligence in real-time. What’s more is this new environment is incentivizing industrial manufacturers to cultivate new business models as they are finding that solutions they have developed in-house are as valuable as the hardware they manufacture. By tracking the performance of manufactured products in the field, manufacturers gain faster feedback loops and insights from customers. For example, instead of waiting months or even years for performance feedback, the integration of cloud-based software and modern hardware provides manufacturers this information in what is approaching real-time. This allows them to respond quickly with fixes, advice or, when needed, replacement equipment. As we enter into uncharted territory for many in this new interoperable, connected tech world, we have to also consider the cybersecurity measures in place and how it will combat any vulnerabilities as the surge of new, industrialized software applications enter our critical infrastructures. Security must be manufactured into the product from the very beginning – this includes tamper-proof hardware, authentication protocols, data encryption and more. What’s Next? Big companies like AT&T and Microsoft are joining forces for the good of the developer. We all can agree software is taking hold of certain business operations, so it is only natural companies would seek an easy solution for enterprise to bring about this change. The industrial side may appear to move slower when it comes to implementation, but that is only because of the various moving parts – machine-to-machine (M2M) devices, sensors and wireless technologies – that must sync with precision without missing a beat. Software is the enabler of this interoperability. So what is the next step in this industrialized development? Jeff Dorsch with Semi Engineering believes that, “Industrial Internet of Things (IIoT) applications proliferate in critical infrastructure, such as the power grid and water supply, the importance of the underlying software and the availability of an open-source platform for app development is coming to the forefront.” This fully-functioning data driven ecosystem will have to decide if open or closed systems are the best for their needs. Google and Apple, for example, have provided internet enabled ecosystems of devices. The problem is that they are closed ecosystems that limit which devices and which data can speak to each other. If industrial players want to take advantage and accelerate their own digital transformations, market opportunities and revenue, then they must take a closer look at open and secure technologies and start innovating for IIoT today. So as we all start to dip our toes in the industrialized software development pond, be sure to consider how your desired outcome matches the factors of delivering business value – customer responsiveness, security, revenue generation and operational efficiency. All are important in and of themselves, but different business models drive different decision-making. Embracing the IIoT app development opportunity early on might prove to be the smartest investment from a competitive advantage standpoint – being able to answer the “why” question is what will eventually separate the high-performers from the rest.
Manufacturing the Future
It’s no secret that the industrial revolution was directly born from the development of specialized machinery, thus providing the means of manufacturing a new path in history. Industrialization marked a societal shift through the development of these new systems, which also opened new ways of doing business. The principles and practices from these transformations continue to have a long-lasting ripple effect on the world today. It may come as a surprise that America manufactures more today than we ever have before in the country’s history. The advancements in manufacturing have spurred the next era of global growth and innovation. As a local manufacturer for the past 20 years in Boulder, Colorado, FreeWave has a unique understanding of how producing goods locally actually improves the bottom line, as compared to sending the work offshore. The Manufacturer is Evolving According to a major report from the McKinsey Global Institute, manufacturing continues to evolve in many ways. Some of the key findings to note were: Manufacturing’s role is changing. The way it contributes to the economy shifts as nations mature: in today’s advanced economies, manufacturing promotes innovation, productivity, and trade more than growth and employment. In these countries, manufacturing also has begun to consume more services and to rely more heavily on them to operate. Manufacturing is not monolithic. It is a diverse sector with five distinct groups of industries, each with specific drivers of success. Manufacturing is entering a dynamic new phase. As a new global consuming class emerges in developing nations, and innovations spark additional demand, global manufacturers will have substantial new opportunities—but in a much more uncertain environment. The report also highlights two very critical priorities for the future: “Companies have to build their R&D capabilities, as well as expertise in data analytics and product design. They will need qualified, computer-savvy factory workers and agile managers for complex global supply chains. In addition to supporting ongoing efforts to improve public education—particularly the teaching of math and analytical skills—policy makers must work with industry and educational institutions to ensure that skills learned in school fit the needs of employers.” IoT and Smart Manufacturing Whether it’s called smart manufacturing, Industry 4.0 or Industrial IoT, even the casual observer of the industrial landscape can see how manufacturing is changing. Being driven by new technologies and rapidly evolving customer demands manufacturers have needed to respond with mass customization – the concept of building flexibility into mass production. Through the adoption of the Internet of Things (IoT), factory and plant settings are becoming more outfitted with advanced instrumentation and being interconnected for a holistic approach to the modern assembly line. IoT provides the ability to gain valuable data off of all the “things” along the manufacturing process. From the condition of assets and equipment to quality and yield metrics, IoT provides live, real-time data from the manufacturing environment to our fingertips. In addition, new data sets (and perhaps more importantly data analytics) are changing the way we see our machines, our processes and our business operations. Analytics can identify patterns in the data, model behaviors of equipment, and predict failures based on a variety of variables that exist in manufacturing. As more factories and equipment are instrumented with the IoT, data volume will only grow larger. In Closing America is still making plenty of “things” and thanks to the latest advancements in technology, is still the leader in many of its fields of expertise. Below is a throwback video from PBS to remind us how the manufacturing sector continues to produce not just products, but ingenuity. Video courtesy of PBS.org
Do You Have Intelligence at the Edge?
Smart devices have added a level of convenience to our lives that we couldn’t have imagined 20 or 30 years ago. Through applications we can manage our bank accounts, check email, listen to music, read the news, pay our bills — and that’s just the tipping point of what’s available today. Now, imagine a business being able to intelligently control the devices at the outermost edge of its communication network through third party applications that operate in a similar fashion to those used on our smartphones. With the Industrial Internet of Things (IIoT) emerging across markets, it is clear that we are heading toward a common goal of complete connectivity across a network – from Sensor-2-Server (S2S). The ability to collect data from any point in the network and transport it where it needs to go creates an opportunity for operational efficiencies driven by advanced data collection and analytics capabilities. Now, with the use of third party applications, it becomes easier to tie components together at the edge of the network and create actionable intelligence. ZumLink solutions are the industry’s first intelligent, programmable 900 MHz wireless network with the ability to connect third party applications. Think of ZumLink as the “smartphone” for industrial networks, allowing you to connect apps designed to meet demanding needs for collecting, protecting, transporting and controlling data from network end points all the way back to the server. Here are the specifics on what makes ZumLink unique: High Speed, Low Power, Long Range – 4Mbps Data Link Rate, 1 Watt output and 100-mile coverage area Programmability – Supports Python and Java, third party applications –just like a smartphone Maximum Flexibility – Standard and user defined hop sets, sense before transmit, frequency hopping and single channel option and user channel masking Until Friday, you have a chance to win a network of ZumLink radios that will help you get a jump start on your future industrial communication technology solutions. Simply provide FreeWave with your use case example and why you should win. All entries must be received by August 19th. FreeWave will announce the winner on August 31st, selected based on submission (U.S. and Canada only). The winning network must be deployed by October 31st. In return for the free radio network, the winning candidate will be able to gain additional promotion of their installation and network implementation! Submit here for your chance to win: http://bit.ly/2awdmkC
An Industrial IoT Anniversary
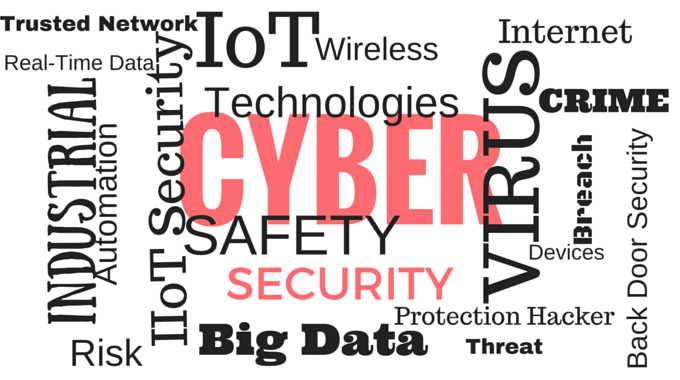
Wow, what a year! This post marks the one year anniversary of publishing Industrial IoT top news, trends and highlights, and we wanted to dedicate a recap post to our favorite articles throughout the past year. In particular, a lot of attention has been paid to the happenings in precision agriculture, oil and gas, unmanned systems, the smart grid, public utilities, manufacturing, machines and machine learning, fog computing, big data, sensor technology, wireless technology and cybersecurity, to name a few. Read on for the top 10 articles we’ve posted since last August and make sure to see the special bonus at the end! Precision Ag: Big data is precision agriculture’s best tool to feed the world By @LuxResearch | Published on @AgProfessionalhttp://www.agprofessional.com/news/big-data-precision-agriculture%E2%80%99s-best-tool-feed-world“Big data can be the most flexible tool for increasing the efficiency of food production through precision agriculture – a quantified approach to cultivation that uses sensing, input modulation, and data analytics to enhance the efficiency of agriculture.” Oil and Gas: In the digital oil field, “no wires” is a no-brainerBy Zach Wertenberger @WPXEnergy | Published on @WorldOilhttp://www.worldoil.com/magazine/2015/september-2015/features/in-the-digital-oil-field-no-wires-is-a-no-brainer“Wireless technology plays an integral part in the day-to-day operations of virtually every industry on the planet. However, if you spent your time visiting most of the world’s oil fields, you wouldn’t believe that.Despite being a rather obvious fit with the inherent nature of the oilfield services sector (OFS), wireless I/O has been adopted by producers at a slow pace, with most continuing to rely upon miles and miles of fault-prone wire to connect onsite control centers with wellsite instrumentation.” Smart Grid: Wireless Lifts Focus on Grid Resiliency By Brad Gilbert @freewavetech | Published on @POWERGRIDmaghttp://www.elp.com/articles/powergrid_international/print/volume-21/issue-6/features/wireless-lifts-focus-on-grid-resiliency.html“Industrial Internet of Things (IIoT) networking technology and wireless Machine-to-Machine (M2M) communications solutions are critical to the daily operations of an increasingly connected and industrial world. With a greater dependence on providing reliable and secure high-speed connectivity to personnel, smart devices, machinery and many other geographically dispersed assets, electric utility operators require powerful, yet flexible, communications solutions for their business demands.” Utilities: Wastewater Treatment: Out of Sight, Out of Mind (Thanks to IIoT)By Scott Allen @S_Allen_IIoT | Published on @Ulitzerhttp://scottallen.ulitzer.com/node/3527211“Water is a crucial piece of any city’s – or country’s – infrastructure. The United States is fortunate to have some of safest drinking water in the world, for a number of reasons, one of which is its many water and wastewater treatment facilities.” Manufacturing: Bringing Smart Technology to Old Factories Can Be Industrial-Size ChallengeBy @mcoc | Published on @wsjhttp://www.wsj.com/articles/bringing-smart-technology-to-old-factories-can-be-industrial-size-challenge-1465351322“It’s a tantalizing vision: Bright and shiny factories where robotic arms and conveyors never break down and production goals are never missed—all thanks to internet-connected sensors that monitor machine health and respond to the slightest supply or logistics hiccup.” Machine Learning: 10 Ways Machine Learning is Revolutionizing ManufacturingBy @LouisColumbus | Published on @Forbeshttp://www.forbes.com/sites/louiscolumbus/2016/06/26/10-ways-machine-learning-is-revolutionizing-manufacturing/#3f10cd992d7f“Machine learning’s core technologies align well with the complex problems manufacturers face daily. From striving to keep supply chains operating efficiently to producing customized, built- to-order products on time, machine learning algorithms have the potential to bring greater predictive accuracy to every phase of production.” Fog Computing: Why IoT Needs Fog ComputingBy @BanafaAhmed | Published on @bbvaOpenMindhttps://www.bbvaopenmind.com/en/why-iot-needs-fog-computing/“The Internet of Things (IoT) is one of the hottest mega-trends in technology – and for good reason , IoT deals with all the components of what we consider web 3.0 including Big Data Analytics, Cloud Computing and Mobile Computing.” Sensors: The Army Wants to Implant Body Sensors into Combat SoldiersBy @tjenningsbrown | Published on @vocativehttp://www.vocativ.com/342014/army-body-sensors/“In the near future, American soldiers might all be implanted with a sensor before going to battle.The United States Department of Defense is interested in monitoring the health of soldiers in real-time. But wearable health trackers have faults and limitations. That’s why the Army Research Office and Defense Advanced Research Projects Agency have awarded $7.5 million to San Francisco-based Profusa to develop tissue-integrated health-monitoring sensors for service members.” Wireless Tech: Industrial Wireless RevolutionBy Soliman A. Al-Walaie @Saudi_Aramco | Published on @ISA_Interchangehttps://www.isa.org/intech/20151001/“Wireless technology is an essential business enabler for the automation world. It has gained rapid acceptance in many industrial sectors because of its cost effectiveness, reliability, fast deployment, and flexibility. Over the past four decades, ultrahigh frequency (UHF) radios have been widely used for long-range supervisory control and data acquisition (SCADA) connectivity in the oil and gas and power and utility sectors.” Cybersecurity: Navigating Industrial IoT risk and complexityBy @EStarkloff | Published on @AMDMaghttp://www.aerospacemanufacturinganddesign.com/article/amd1015-industrial-iot-complex-systems/“As massive networks of systems come online, they will need to communicate with each other and with the enterprise, often over vast distances. Both the systems and the communications need to be secure or millions of dollars in assets will be put at risk. One example of the need for security is on the smart utility grid, which is on the leading edge of the IIoT.” Bonus! Eliminate the cost of your next IIoT deployment Now is the time to brave the digital transformation in your industry while you continue to future-proof your systems. All you need to do is submit a use case for your radio network for a chance to win a next generation industrial wireless IoT solution. All entries must be received by August 19th. FreeWave will announce the winner on August 31st chosen based on submission (US and Canada only). The winning network must be deployed by October 31st. In return for the free radio network, the winning candidate will be able to gain additional promotion of their installation and network implementation! Submit here for your chance to win: http://bit.ly/2awdmkC. Learn more about ZumLink.
Where is RF Technology for Oil and Gas Headed?
The entire landscape of the oil and gas industry is changing. Not only has the industry downturn forced operators to rethink their business models, but the RF technology supporting industry operations is quickly changing. It is more important than ever to make intelligent business decisions with the right technology in place. As a decision maker for your organization, you need to be aware of the technology that is pointing towards the future of automation and RF technology. Challenge yourself to think beyond basic command and control and picture a fully connected network – from Sensor-2-Server. Here’s a quick snapshot of the technology movement we are seeing in the oil and gas industry right now: The installed base of wireless Machine-to-Machine (M2M) devices is growing. More technology in the field allows operators to access more data from more sensor access points – on a grander scale than ever before. The ability to leverage Big Data supports intelligent decisions that will optimize business operations and cut down on expenses. The Industrial Internet of Things (IIoT) is the future of communication technology. With IIoT, data can be transported from its collection point to wherever it needs to go – anywhere in the network. This has sparked a convergence of OT and IT operations, driving RF technology networks closer to the concept of complete connectivity. With a fully connected network, decisions are made based on comprehensive data, which drives intelligent problem-solving. With that type of insight, you could better disperse your resources, leaving a positive impact on the organization for years to come. Sensor-2-Server (S2S) solutions that deliver intelligence to the access layer are critical to industry success. S2S solutions bring intelligence to the access layer, enabling edge devices to do more than simply transmit data. They support highly detailed data analysis such as predictive analytics. Imagine the operational decisions you could make with a complete set of data from the outermost edge of your network all the way back to the server. IoT App development is the next big thing. Programmable third-party applications are on the horizon of the wireless RF solutions market. These apps will support machine learning, distributed intelligence, predictive maintenance, and more at the edge of the network. Technology is being designed to enable these applications – which have the potential to lead the industry to the next frontier of RF technology.
IoT Top News: Distribution Intelligence
According to the U.S. Department of Energy, distribution intelligence refers to the part of the smart grid that addresses utility distribution systems – meaning the wires, switches and transformers connecting the utility substation to both the utility company and the end customer. These systems are designed to drastically improve the demand response times and overall efficiency of transferring electric power, thus enabling a fully controllable and flexible distribution system and giving field technicians the actionable knowledge to troubleshoot problem areas faster. As utility providers continue to move towards a digital and connected enterprise, the prospect of a self-healing power distribution system becomes extremely valuable – especially as electric power consumption continues to rise globally. That’s way this week’s round up is dedicated to distributing intelligence across one of the most mission-critical infrastructures on the planet – the power grid. State of Distribution Intelligence, per a Recent Smart Grid Report A smart grid survey of 70 U.S electric cooperatives found that, regardless of the challenges most have found a way to start incorporating smart grid technology across the board. Zpryme and the Rural Smart Grid Summit (RSGS) report that, “Nearly all electric cooperatives have some sort of smart grid effort. Many are at thestage of deploying multiple applications (31%) up from 21% last year. Pilot projects are also growing from 8% last year to 16% this year.” We Now Have Hourly Data on the US Power Distribution System The U.S. Energy Information Administration (US EIA) can now collect data on electric supply, demand and flows on an hourly basis. CleanTechnica informs us that, “EIA’s U.S. Electric System Operating Data tool provides nearly real-time demand data, plus analysis and visualizations of hourly, daily, and weekly electricity supply and demand on a national and regional level for all of the 66 electric system balancing authoritiesthat make up the U.S. electric grid.” Distribution Intelligence Starts with Proper Training India’s National Smart Grid Mission (NSGM) with USAID announced they will begin a series of utility personnel training programs designed to help educate workers on smart grid functionality and design. The Business Standard revealed, “The government has taken several proactive steps towards grid modernization, including the establishment of a Smart Grid Mission to plan and monitor the implementation of policies and programs related to Smart Grid activities in India.” Cyber Attack Vulnerability in the Power Grid? We have all heard about a few of the big cyber attacks that have affected some big companies, but many don’t realize an attack on the electrical infrastructure could be crippling to our society. The Energy Collective unveiled a quiz to dispel some myths about the state of cybersecurity in the power grid. “Minimizing the risk is not just about training a network IT team. It’s about running a comprehensive and continuous scan of operational technology (OT)—the programmable logic controllers, the mobile devices, the supervisory control and data acquisition systems (SCADA), etc.—and then coordinating OT and IT teams with risk officers and crisis management experts to form a cohesive front capable of responding to an industrial cyber incident.” Perhaps the notion of distribution intelligence systems can help address and alleviate some of these concerns. Most utilities are only starting on the road to true distribution intelligence, but the market is expected to boom in the coming years. With the advent of industrial IoT technologies and new regulatory factors, we could realize distribution intelligence in our power grid sooner than later. I hope you have enjoyed our weekly round up on distribution intelligence, and please be sure to leave your comments and questions below. BONUS ARTICLE The round up above is all about the smart grid and how to make it more efficient and resilient. Ever hear of a smart city? Smart cities are connected cities, and they work in conjunction with everything from IoT sensors to open data collection and smart streetlights to provide better services and better communication. Teena Maddox from Tech Republic wrote a great round up piece on six essential technologies that make the smart city of the future a reality today. Give it a read!
The Next 30 Years of IT
At Interop Las Vegas back in May, InformationWeek Executive Editor Curtis Franklin sat down with Senior Editor Sara Peters about how IoT is changing everything we know in IT, especially in the industrial enterprise. From predictive analytics, to security, to ROI, see why Franklin and Peters view the next 30 years of IT starts with IoT. Here are some key trends and considerations worth noting: We’re starting to see a clear division between the consumer and industrial markets as far as the evolution of IoT. The Industrial IoT (IIoT) space looks to be growing, developing and maturing at a faster rate than the consumer IoT space. The concept of predictive maintenance and advanced analytics is where a lot of innovation and excitement is happening for a few reasons: The end-to-end enterprise IT toolchain is now being viewed holistically, looking at how data and information travels from the sensors at the edge of the network, through the different networking and communication modalities and all the way back to the big data analytics engines at the core network (further reading: Sensor-2-Server). As a result of the new intelligence and operational efficiencies that are being realized, companies are seeing hard dollar returns which provide the capital to make new investments in these emerging technologies Security is a legitimate concern and while the pace of innovation might be slowing the adoption or rollout of new IoT technologies, vendors and service providers recognize the importance of the security paradigm and are building encryption and authentication into their systems. Interoperability of networks – are they being taken for granted? Perhaps there is even more on the horizon as far as how different technologies and networks integrate. The progression of new RF standards has been slower than most expected; will it pickup from here? The answer is most definitely and through ubiquitous networking and other advancements with RF and digital engineering, we will see innovations in the application layer of networks over the next five years that we can only dream about today.
Berg Insight: Bright Days Ahead For Wireless Automation
A recent report published by Berg Insight details the bright future ahead for Industrial IoT through the implementation of wireless automation technologies. Berg Insight senior analyst Johan Svanberg made note that higher levels of automation and IoT solutions enable “shorter lead times, lower inventories, increased throughput as well as more flexibility and the ability to respond faster to changing customer needs.” The wireless IoT device market is served by a multitude of players from various backgrounds including global automation solution providers, automation equipment and solution vendors, industrial communication specialists and IoT communication specialists. This new report from Berg Insight informs us that: 2015 estimate of wireless devices for industrial automation applications reached 4.8 million units worldwide. Wireless devices installed for industrial applications have a forecasted growth rate of 27.7 percent from 14.3 million connections at the end of 2015 to 62.0 million devices by 2021. Key Findings from Berg Insight: Wireless connectivity is instrumental in the Internet of Things era and the use of wireless solutions in industrial automation is increasing rapidly at all levels of automation systems. Industrial automation systems utilize wireless communication to connect remote and local facilities and equipment to increase operational efficiency. A wireless automation system contains a mix of network technologies, equipment and systems including enterprise and automation systems, network equipment, control devices and field devices. The most common wireless technologies in industrial automation include cellular, 802.11.x Wi-Fi, proprietary unlicensed ISM radio, Bluetooth, various LPWAN technologies and 802.15.4 based protocols such as WirelessHART, ISA100.11a and ZigBee. Berg Insight estimates that shipments of wireless devices for industrial automation applications, including both network and automation equipment, reached 4.8 million units worldwide in 2015. Growing at a compound annual growth rate of 25.1 percent, shipments are expected to reach 18.3 million by 2021. The installed base of wireless devices in industrial applications is forecasted to grow at a compound annual growth rate of 27.7 percent from 14.3 million connections at the end of 2015 to 62.0 million devices by 2021. Wi-Fi is widely used for backbone communications as well as in monitoring and control applications within factory automation where Industrial Ethernet has got a strong foothold. Bluetooth is also popular – often as a point-to-point wire-replacement between for example a mobile HMI solution and a field device or control unit. 802.15.4 networks are often used to connect wireless sensors and instrumentation in process automation. Cellular connectivity is typically used for backhaul communication between plants, connecting remote devices in long haul SCADA applications and for third party access to machinery and robots. LPWAN technologies are increasingly used in certain low data, long range applications. Most of the major vendors of wireless IoT devices in industrial automation offer a wide range of devices with various wireless technologies in order to support many different applications. Key Takeaways, According to Berg Insight: Companies are now deepening the integration between industrial automation systems and enterprise applications and the promise of IoT is getting more tangible by the day. Large multinational corporations are beginning to systematically develop and adopt best practices to maximise the benefits of IoT technology in every part of their organisations. IT/OT convergence, smart factories, Industry 4.0 and the Industrial Internet of Things are concepts which are part of the ongoing evolution of industrial automation. Innovation in sensors, wireless connectivity, collaborative robots, big data and cloud solutions along with seamless exchange of information between devices, systems and people paves the way for improved performance, flexibility and responsiveness throughout the enterprise value chain. For more information, read the full report from Berg Insight.
IIoT Top News: Machine Learning
Machine-to-machine (M2M) learning is an integral apart of the expanding world of Industrial IoT. Over the past few months we have given attention to manufacturing and its current digital disruption, but have failed to show the direct impact smart M2M and IoT technology is having on the industry. So, this week we are diving deeper into the term machine learning and how it connects to manufacturing both today and in the future. Before we get to our news round up let’s start by re-defining M2M, to ensure we are all on the same page with its purpose and meaning. Gartner has defined machine-2-machine communications as “something used for automated data transmission and measurement between mechanical or electronic devices.” Now, that we have defined M2M, its time to check out our top news round up for the week on how M2M applies to both manufacturing and IoT. 10 ways machine learning is revolutionizing manufacturing Machine learning is poised to improve manufacturing by streamlining the process of OT and IT, thus increasing efficiency and lowering overall operation costs. Louis Columbus at Forbes believes that “Every manufacturer has the potential to integrate machine learning into their operations and become more competitive by gaining predictive insights into production.” IoT will recharge Machine Manufacturers Manufacturing can look to software companies as an example of how IoT can implement creating a smarter M2M network. Timothy Chou with CFO.com writes, “Today, manufacturers of machines — whether seed drills, chillers, or CT scanners — can leverage the path paved by the software product companies through three new business models: service and support; assisted services and machine-as-a-service.” Climbing the IoT Mountain–by adding M2M to manufacturing Manufacturing is only at the beginning of its ascent into IoT and M2M, so there are many more bumps and obstacles a long the way for the industry to fully integrate. Ronnie Garrett with Supply & Demand Chain Executive describes IoT and M2M manufacturing implementation as, “Standing at the foot of Mount Everest, ready to climb the world’s tallest mountain. You know you want to get to the top but you aren’t really sure how you will get there or what obstacles you’ll encounter along the way.” Cybersecurity is manufacturing’s biggest risk factor Manufacturing needs to continue to add M2M automation and big data analytics to the shop floor, but a threat to the overall industry is manifesting itself in the cybersecurity world. Ian Wright with Engineering.com informs writes, “A new report from BDO indicates that 92 percent of manufacturers cited cybersecurity concerns in their SEC disclosures this year. According to BDO, this represents a 44 percent increase compared to the first Manufacturing Risk Factor report in 2013.” As we wrap up our top news for the week, we realize the need to fully implement advanced machine learning across the manufacturing world will take more than a simple flick of the wrist. With that said, we leave you with a cautionary tale of when automation goes wrong. It was recently discovered an airport in India had an sign translated with automation software which read, “eating carpet strictly prohibited” — of course this was not the translation they had meant to display. Regardless, as we move towards a fully integrated M2M world, we will have to adjust our equations depending our our intended outcome, much like the world is finding with the love/hate of language automation. Hope you have enjoyed this week’s top news, as always tell us your thoughts on M2M and how it might impact your world!