Technology Revealed: Unraveling Data Accessibility for Industrial IoT
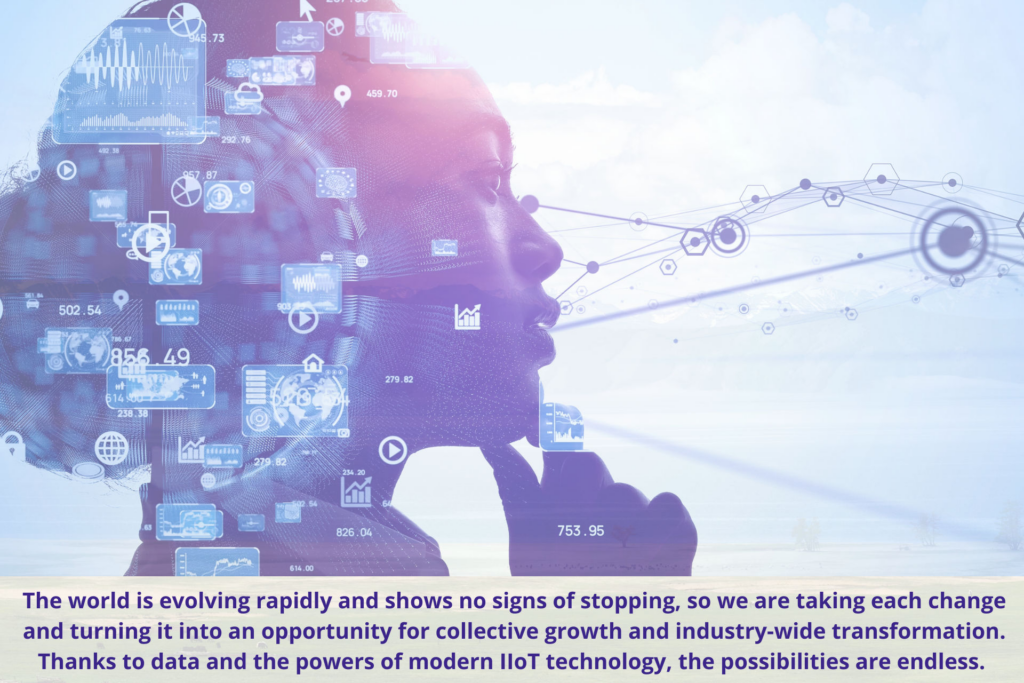
Our world is full of endless possibilities. Thanks to modern technology, we are more digitally connected than ever before. According to Statista, there will be upwards of 30.9 billion connected internet of things (IoT) devices by 2025. From smartwatches and traffic cameras to medical sensors and security systems, the more technology in effect, the more data we are able to collect. If you’ve heard it once, you’ve heard it a hundred times: data is everywhere, and it continues to be an incredible asset for leaders across industrial environments. Today, our widespread access to data allows us to make informed and intelligent decisions based on accurate intel. Something as simple as knowing soil moisture levels or the outside temperatures helps us respond to environmental needs in strategic ways. While data accessibility is undoubtedly a positive thing, it doesn’t mean much if we don’t have the tools needed to act upon those same data insights available to us, and this is where technology makes a tremendous difference, especially for industrial leaders. When we take the revolutionary power of the industrial internet of things (IIoT) and pair it with the wide range of data metrics available, we can intentionally foster better industrial environments across the globe. Our increased access to data, paired with the modern revolution of IIoT technology, allows us to respond to real-world problems with timeliness, precision and contextual intelligence. Together, this dynamic pair fosters safer, faster and more efficient environments for all. The power of time and context When it comes to data accessibility and Industrial IoT, there are many profound revelations of impact, time being just one of them. In industrial environments, timing is everything. It’s the difference between a healthy crop and a wasted harvest for the smart farmer; it’s the difference between an uncontrolled wildfire and a self-contained outbreak for the modern firefighter; it’s even the difference in what could’ve been merely a small oil leak rather than the environmental disaster we now know as the Deepwater Horizon oil spill. Data accessibility provides us with timely information on the surrounding contexts of our environments, and with the right tools, we can respond to this information faster and more efficiently than ever before. Contextual intelligence Next in line to the value of timing, lies the power of contextual data, also known as contextual intelligence. Contextual intelligence is a game-changer for the industrial leader, as it provides a deeper level of understanding and offers an enhanced sense of accuracy for production. Think of any environmental disaster, be it a forest fire, dust storm or even a carbon monoxide leak. While IoT solutions cannot prevent these events from happening, they can provide immediate insight to these occurrences based on contextual analysis. With the right sensors in place, data is retrieved and distributed, making room for timely interception. With the proper insight, operational leaders and manufacturers can observe what’s happening in critical environments and make intelligent decisions based on the contextual data available. Today, IIoT solutions allow us to control external environments virtually anywhere in the world without laborious human intervention. In this modern age, the simple switch of a button or command from a control center can adjust the outputs of remote operations everywhere. We call it a single pane of glass approach. When emergencies arise that need immediate attention, these same IIoT solutions help us respond quickly and efficiently, ultimately maximizing people’s time more effectively. The role of intelligence In addition to time and context, the third component is intelligence. Data takes the guesswork out of problem-solving and invites us to respond with precision-based strategies. Think about smart farmers, for example. With proper insight into the correct data like soil moisture levels, external temperatures, climate measurements and other relevant intel, these farmers can cultivate the most favorable conditions for a quality harvest. Without this information, farming becomes a guessing game that varies from year to year, but when this data is paired with IIoT solutions, agriculture becomes much more about intelligent strategy. Looking ahead, the digitization of farming is quickly becoming a necessary solution. Our world population is rapidly increasing every day, leading us to grow by 2 billion people in the next 30 years alone! A significant increase in people requires a significant need for accelerated food production. In fact, it’s reported that we will need to increase crop yields and harvest more food in the next 30 years than we’ve had to produce for the last 10,000 years combined. Though these statistics are extreme, they don’t have to be alarming because with the right technology in place, society will be up for the task at hand. The interconnected work of data and IIoT takes smart farming to a whole new level, making it less of a gamble and more of a controllable process from seed to harvest. Beyond the world of just smart agriculture, data impacts the role and work of IIoT solutions across every industry, including water and wastewater, electricity, oil and gas, transportation and traffic and many others. Our ability to access data empowers us to leverage IIoT technology most intelligently; it’s the “work smarter, not harder” mindset at its finest. Technological pioneers At FreeWave Technologies, we are passionate about creating real-world solutions for everyday needs across industries. In a world that is changing with rapid succession, connectivity is critically important for industry leaders, remote operations and the basic good of society. We need tools and products that help us act on data quickly and precisely, and our line of products is helping our customers do just that. FreeWave products take the complexity of industrial IoT applications and simplify them for the user, creating a digitization strategy that connects data with life. Our easy-to-use applications allow controllers to respond to their deployed assets from one place with timeliness, intelligence and precision. At FreeWave, we are pioneering a new way forward, promoting connection, safety and innovation along the way. The world is evolving rapidly and shows no signs of stopping, so we are taking each
The Unlikely Marriage of Sustainability and IIoT
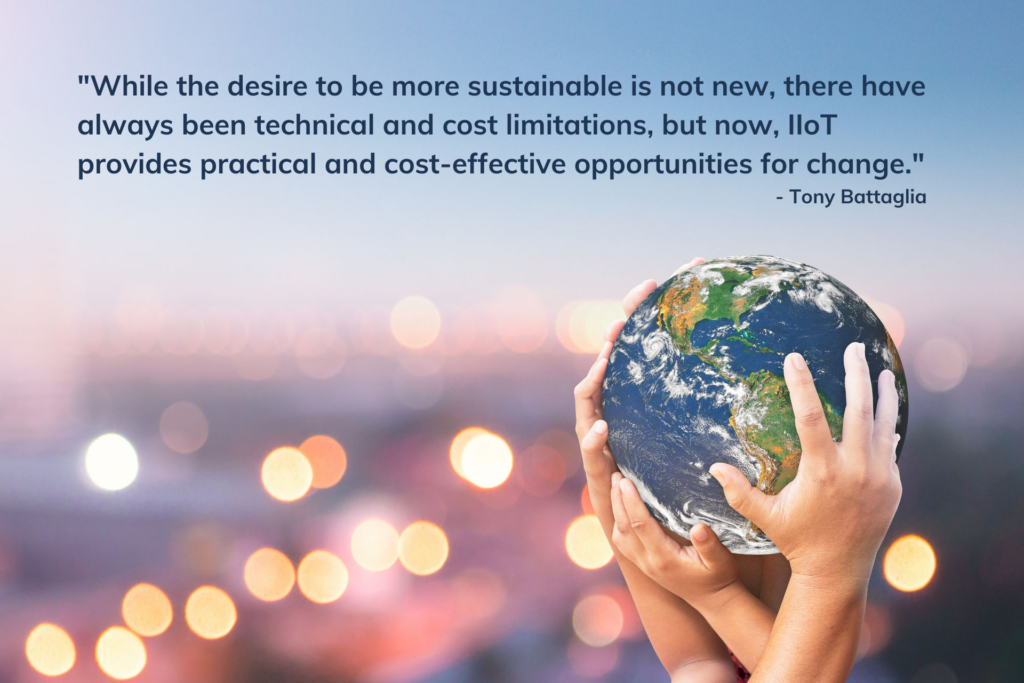
When I think about technology’s impact on sustainability, I think about home. I live in California, and earlier this year there was a fire in my area which, unfortunately, destroyed a lot of houses and affected many families. Luckily, because my city deployed industrial internet of things (IIoT) solutions for fire protection services, they were able to detect this fire early on and prevent further damage in the area. In this scenario, IIoT solutions provided timely insights which allowed the appropriate resources to respond faster, creating a better and safer future for my community. The unlikely pair Sustainability is a widespread conversation these days, and for good reason – a more environmentally conscious world equals better quality of life for us all. As such, electric cars are on the rise, paper straws are everywhere and many companies are doing their part to minimize their carbon footprint. As a collective, we are making great strides in our attempt to create more eco-friendly communities. Amidst our best efforts, however, many may not realize the positive and profound role modern technology, specifically IIoT, can have on our journey towards a greener society. This may come as a surprise, but now more than ever, IIoT is playing a key role in realizing our sustainability goals. Real-world change Today, IIoT technology is completely enhancing our approach to transformative environmental practices by providing the power of response. By implementing IIoT into our data, we can do much more than just monitor data; we can actually respond to data by pulling trends, sending out alerts, leveraging artificial intelligence and so much more. IIoT allows us to take data-driven action, and this is ultimately having a significant impact on the environment and entire industries across the globe. Industry-wide impact In 2015, The United Nations Member States all adopted the 2030 Agenda for Sustainable Development. This global partnership calls countries into action to create a stronger planet by implementing eco-friendly strategic practices to achieve 17 different Sustainable Development Goals (SDGs). Technology plays a significant role in realizing these SDGs. In fact, there are a variety of industries becoming more sustainable because of IIoT. Let’s look at energy, for example. Recently, the energy space began implementing environmental and social governance (ESG) criteria. Now, different organizations can receive access to various federal funds depending on their ability to meet ESG standards. Without the use of IIoT practices, procedures and functions, these organizations could not make the improvements needed to contribute to their environmental goals. With the use of IIoT, these same companies can effectively monitor and manage environmental assets through automated procedures that contribute to more efficient industries and remote work environments across the board. Ultimately, IIoT technology offers the insight and practical solutions needed for these companies to create positive structural changes. The benefits don’t stop there. We’ve all heard or read that our water supply is endangered, and this is not just a California issue, like many assume; it’s a widespread problem that needs immediate attention. The rapid rate of water decrease is not just a byproduct of human consumption, it is also a direct result of everyday processes, industrialization and the ever-changing climate. Today, IIoT products are providing simple solutions to monitor timely data metrics like rainfall rate and water consumption. These solutions respond to water shortages and water waste in innovative ways. Through IIoT, we now have the ability to adjust and adapt our behaviors based on data visualizations, and throughout the process, greater sustainability is achieved worldwide. The IIoT difference on finite resources With sustainability, the goal is really to manage the lifespan of an existing asset, be it drinking water, livestock, oil and gas, the list goes on, and with IIoT technology, we can better control our ability to manage these assets. While the desire to be more sustainable is not new, there have always been technical and cost limitations, but now, IIoT provides practical and cost-effective opportunities for change. At FreeWave Technologies, we’re committed to improving life’s essentials through Industrial IoT solutions. Our full line of connected IIoT network solutions bring most needed data to operations teams wherever they are and our ready-to-deploy solutions play a significant role in environmental monitoring ultimately leading to safer and more sustainable communities. When it comes to Environmental IoT™ we are spearheading a new way forward, offering solution-based products that empower industrial leaders to manage their assets simply and intentionally. Our single pane of glass dashboard creates a singular view for our customer, allowing them to track, control and respond to timely data metrics in one place instead of multiple dashboards across applications. Products that solve problems are important, and that’s exactly what we’re providing at FreeWave. We’re shifting the culture of sustainability from altruism to action, and it’s making a substantial difference. At the end of the day, I care about the world that I’m leaving for the next generation. Every day I think about my two children and the world they’ll grow up in; I want to do my best to create a place where they can thrive, and I’m excited to be a part of an organization that is achieving just that.
Technology’s Impact on Air Quality Control Monitoring
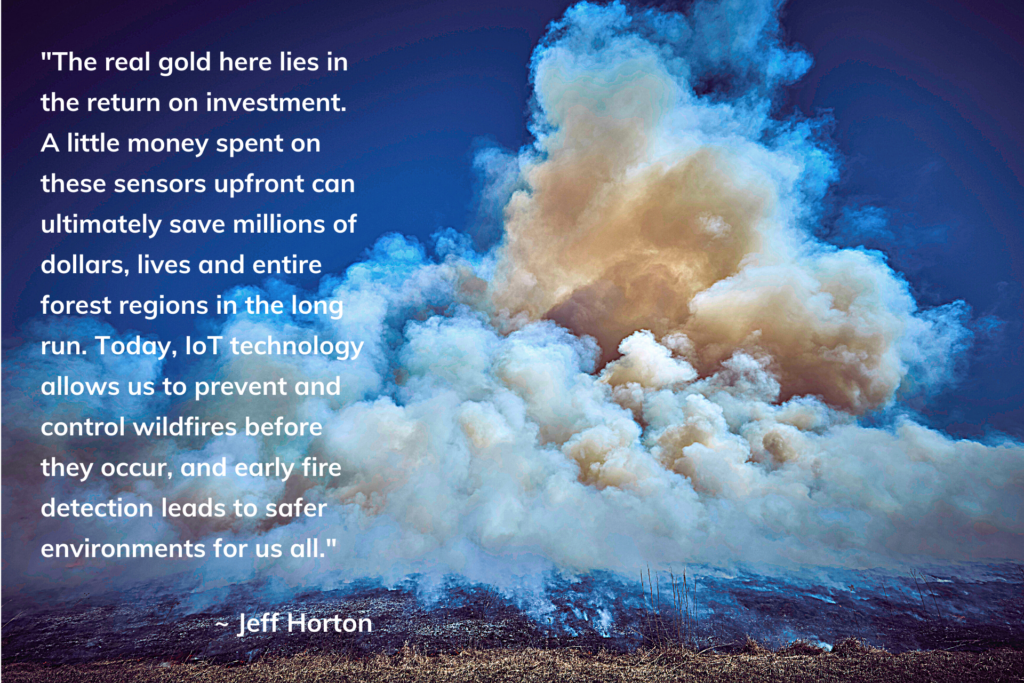
At this very moment, wildfire season is currently underway in North America, and since the start of this year alone, more than 27,000 wildfires have consumed nearly two million acres according to the National Interagency Fire Center (www.nifc.gov). Though many people hear the word “wildfire” and immediately picture a forest in California, the reality is these natural disasters are prevalent across the country. Wildfires are everywhere The Verge, a technology news website, announced recently that roughly 56% of homeowners in the United States face some sort of wildfire risk in the upcoming decades. Bottom line: wildfires are becoming more prevalent and costly every day, and these fires are affecting more than half the population and significantly changing our quality of life. Just a few decades ago, we didn’t have the technology to prevent or predict changes in the surrounding air quality, but now we do, and through it, we can create a better world. Today’s technological advancements allow us to be proactive rather than reactive when it comes to our overall health and safety. By leveraging sensor technology, we have a better chance of predicting and preventing significant changes in the environment, like a drastic shift in air quality before a wildfire begins. This insight allows us to make better decisions based on intentional insights, and our increased access to data provides us with the right information to better control our surrounding environments. Technology is powerful, and this power can and should be used to our advantage. One of my favorite ways to witness the power of technology transforming real-world issues is by exploring the ways sensor technology has a tremendous impact on air quality control monitoring. Today, internet of things (IoT) technology and satellite are the best tools for early detection and prevention of wildfires. Our approach to air quality control Believe it or not, air quality has as much impact on the world as the daily temperature. With climate change causing drastic shifts in the environment, it’s important that we pay close attention to the quality of the air we breathe, as it affects our overall quality of life. As you know, trees play a critical role in our ecosystem, so we must be very intentional and proactive about protecting the forests around us. This is where sensor technology makes a big difference. With a small machine, we can now track and predict changes in the environment and our surrounding air quality, which ultimately helps us control, prevent and predict conditions that lead to wildfires. At FreeWave, we provide autonomous sensors that are strategically placed in remote locations to track and record relevant data metrics such as temperature, humidity, wind, direction and particulate matter. These readings help industry experts know what’s in the air and how the air is changing. Once this data is collected and transmitted to the cloud, we are then able to analyze it and provide alert and proactive responses where needed. We have created a single pane of glass approach, where anyone with access can log into a portal and see in real-time what is happening in the areas surrounding their deployed sensors. The interesting thing about our sensors is that they are fully powered by solar energy, and satellite signals transmit the recorded data. We are basically offering a “buy, install and forget” resource that makes life significantly easier for industry and environmental experts. There is a ton of value here. Not only are we taking an in-depth look at what’s going on in the environment through air quality control monitoring, but we are also taking that information and transforming it into action. The real gold here lies in the return on investment. A little money spent on these sensors upfront can ultimately save millions of dollars, lives and entire forest regions in the long run. Today, IoT technology allows us to prevent and control wildfires before they occur, and early fire detection leads to safer environments for us all. A unique human aid We are making life simpler and safer for all by using technology to do what humans can’t. Back in the day, people had to sit in an operation tower for hours, looking out to catch any major changes in the environment. Today, there is a major shortage of people willing to do this kind of work, and can you blame them? As humans, we can only be in one place at a time doing one thing at a time, but with technology, this is not the case. With simple sensors, we can now monitor and control a lot more environments at a much more affordable rate. All this to say, the goal here is not to replace humans with technology as some might think; what we are really doing is enhancing human ability through the power of technology. I’ve worked in technology for over 30 years, and every day I witness its evolution. I know it’s hard to imagine a world without cell phones, but I can still clearly recall the days when cell phones took up the entire trunk of a car, and now look at the world, most of us carry the same ubiquitous smartphone in our pockets. Technology is amazing, and we have the opportunity to use it to our advantage. At FreeWave, we are taking the capabilities of mobility – LTE, 4G, Satellite, Wi-Fi, Bluetooth, 900 MHz– and marrying them with sensors. The data we gain from these sensors is saving us time, money and resources. At the end of the day, we’re taking away the need to “overthink” industry issues, like how to better prevent forest fires, and instead are replacing our questions with data-informed predictions and timely proactive responses. Every day, we strive to provide industry leaders with the tools and technology needed to spearhead faster and safer environments for us all. This is certainly not a boring business, and I thoroughly enjoy working for a company that is using technology to have an impact on the things that matter most.
Got Data? Now what?
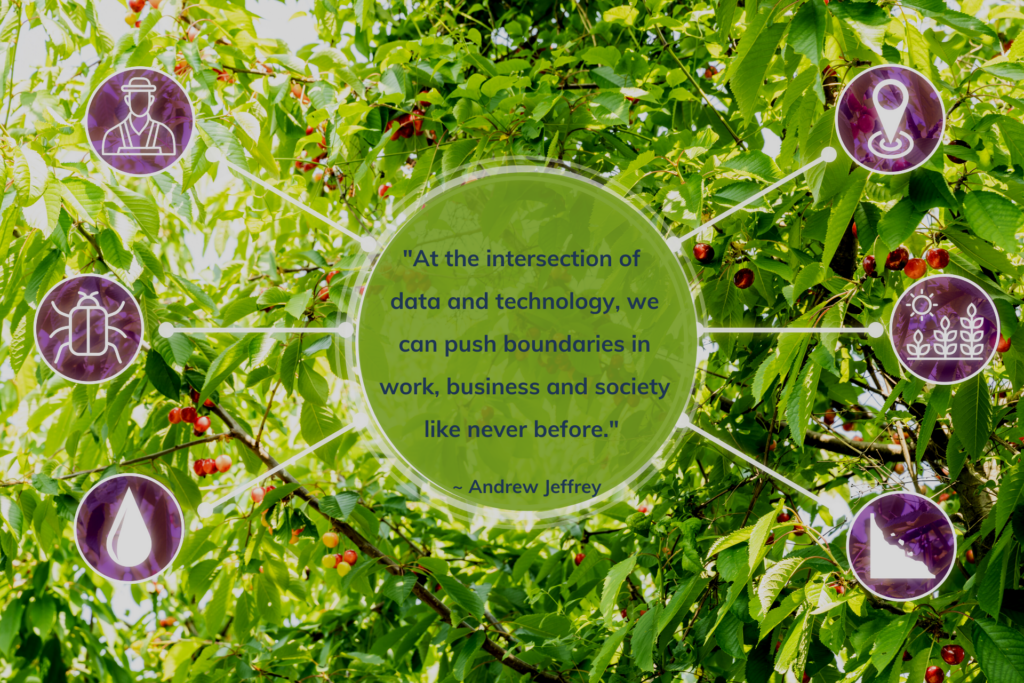
It’s hard to imagine a world without the daily convenience of modern technology. Just yesterday, I joked with my kids about the world before the internet – a time when we actually had to go to the library to look up unknown information. I can still remember the early days of my college career back in the late 90s, the internet had just come out, and we were all getting used to this new phenomenon called a “search engine.” Life has drastically changed over the last 25 years. Now, nearly all the information we want and need is at our fingertips. Today, we have more access to data than most people know how to handle. Data is all around us, collected through the day-to-day actions and reactions of our lives. When we take the time to intentionally analyze, interpret and distribute the data metrics available to us, we can make smarter and more efficient decisions. There is so much to explore, and while our increased access to data is pretty interesting, the reality is that the combination of data and modern technology can change the world. Like many things, though, there are two sides. Sure, industrial companies can capture huge amounts of data, but it also raises the question: now what? How do you put all that data to work? Breaking barriers and pushing boundaries At the intersection of data and technology, we can push boundaries in work, business and society like never before. Data insights allow us to be more precise and accurate in our day-to-day work, which allows us to be more effective and efficient. The operational benefits here are endless, including improved quality control, reduced energy consumption, enhanced safety and increased operational consistency. Just take a look at the food industry, for example. Many field workers in smart agriculture rely heavily on data insights to control, predict and create the best environments for quality crops and harvest. The more accurate their predictions, the better their harvest, and the better their harvest, the faster we receive our food through the supply chain. Today, internet of things (IoT) technology can connect remote and mobile assets, like a tractor, for instant data access, making it easier for farmers to be more efficient and effective in their work. It’s really amazing when you think about it. Data is transforming how we operate in this world, creating better environments for us all. The FreeWave impact At FreeWave, we are constantly pushing the boundaries of technology to create faster, smarter and more efficient work environments. I’ve been a part of the FreeWave team since 2019, and I am constantly amazed at the ways our technology provides innovative solutions for real-world issues. Our products enable our customers to improve their work processes, and through our single pane of glass approach, we offer a simplified experience for businesses and industry leaders to receive automated technology that transforms data metrics into real-time execution. One of my favorite use cases to discuss is FreeWave customer that uses drone technology to deliver food and other valuable resources to far-reaching areas across the globe. With FreeWave products, they can run a smarter and more efficient operation. Their robotics delivery system is combating many of the complex access challenges the world faces on a daily basis. Our IoT technology is helping them solve complex issues with simplified tech solutions, and simple solutions create more time, energy and space to focus on what matters most: people. If you need a product to help you bridge the gap between technology and data, FreeWave is your solution. We are enablement partners, helping every one of our customers accomplish their complex goals. It’s inspiring to work with brands and businesses striving to create a difference in real-world issues. Our technology plays an intricate role in sustaining work environments and supporting entire industries around the globe. Data makes the difference At the end of the day, data is more than mere statistics; data is the key to our efficiency, productivity and safety. Data makes the difference in energy consumption reduction. Data makes the difference in the overall quality and safety of our daily environments. Data makes the difference in everything. Every day we have the opportunity to use data to our advantage, and at FreeWave, we are helping industrial innovators do just that. As technology continues to evolve, we will continue to provide top of the line IoT solutions that transform data into actionable insights and execution so you can not only access a treasure trove of data, but also know exactly how to answer the age-old question: now what?
Data is everywhere, even on Mount Everest: Sensor-to-cloud and extreme environments
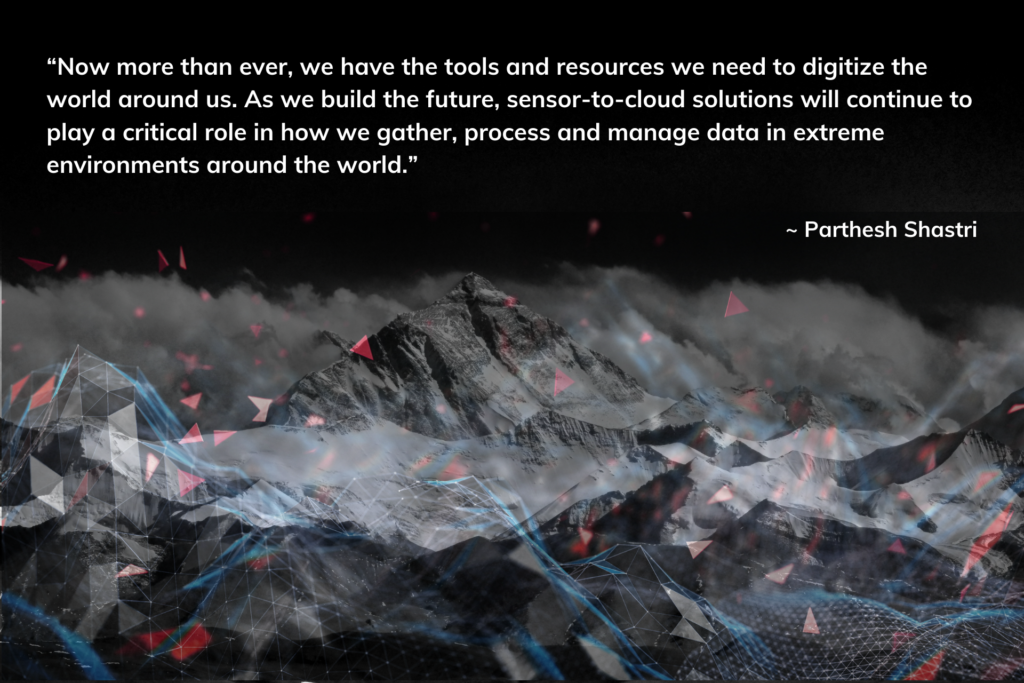
Technology – from Mount Everest to the farm It’s amazing what technology can do when paired with human will. Just a few years ago, a team of scientists made history as they trekked up Mount Everest with the goal of running environmental studies. With backpacks full of sensors (which included FreeWave technology), these men pushed boundaries to create a new normal. When we intentionally use modern technology to our advantage, we can create better, safer and more productive environments within every industry. Today, the same technology used on Mount Everest is now powering multiple earth science programs transmitting sensor data from remote environments to earth scientists, climatologists and meteorologists through cloud servers. This is just one example of many where sensor-to-cloud solutions have transformed our ability to interact with extreme environments in the modern world. A deeper look at extreme environments Typically, when someone thinks of an extreme environment, they imagine harsh, rugged terrain in a far-off remote location; however extreme environments aren’t limited by this definition. Take a large farm, for example, with a multitude of deployed assets and equipment across hundreds of acres. Traditionally, an operation like this requires an employee to physically check on the farm equipment multiple times a week, manually turning valves on and off, in addition to monitoring and controlling the overall farm environment. These day-to-day tasks are not only time-consuming but physically draining. In this case, the operational output required on the farm makes it an operationally extreme environment, and extreme environments are just one space where sensor-to-cloud solutions shine. Sensor-to-cloud in the real world Today, sensor-to-cloud systems utilize deployed sensors to collect and transmit data from remote locations. These sensors send the gathered information back to cloud servers for further research and analysis, enabling entire teams to utilize their limited time and resources more effectively. With sensor-to-cloud systems, we eliminate the often-laborious mechanics of middlemen procedures so that industry leaders can focus on what matters most. Let’s revisit that farming example. With sensor-to-cloud technology, farmers can automate the repetitive tasks of their operations. Something as simple as discrete soil sensors further allow farmers to virtually monitor their crop health, creating more time and space to focus on other high-value tasks. This gives them time, often an invaluable asset, to do what’s needed. In a sense, we can improve the productivity of an operation with an automated suite of sensor systems. Imagine the difference a network of sensors can make. The FreeWave difference For several years now, FreeWave products have been a leading resource solution for extreme environments. Our sensors were a part of the great Mount Everest expedition, and today, we have deployed sensors in many areas, including pipelines in Alaska, ice shelves in Antarctica, smart farms across the country and many other locations – rugged and traditional. We are providing the groundbreaking technology needed to monitor data in extreme environments so that our partners and customers can make the best, informed decisions for their operations. As the Chief Technology and Product Officer at FreeWave, I am constantly amazed at the impact our products have on the world. We are working with some of the major brands of our time, helping them solve massive problems affecting society at large. Our technology solutions serve entire industries, like oil and gas, agriculture, transportation and traffic, as well as many others that contribute to the well-being of the globe. It is great to be a part of a company where we can say our products are a part of the solution for life’s essentials. Every day, we help industry leaders identify their pain points and provide them with a single pane of glass product solution that helps them see the data wherever they are without the drain of additional resources. Our rich portfolio of radios, gateways, cloud software and analytics allows us to stitch together a range of packaged ready to use applications that solve our customer’s problems through simple, turn-key solutions. Sensor-to-cloud in the future Data is everywhere, and now more than ever, we have the tools and resources we need to digitize the world around us. As we build the future, sensor-to-cloud solutions will continue to play a critical role in gathering, processing and managing data in extreme environments around the globe. As I look at the world before us, I see endless opportunities to continue to leverage technology and data to build a better and more informed life.
Technology Simplified: Leveraging Data in the New Digital Era
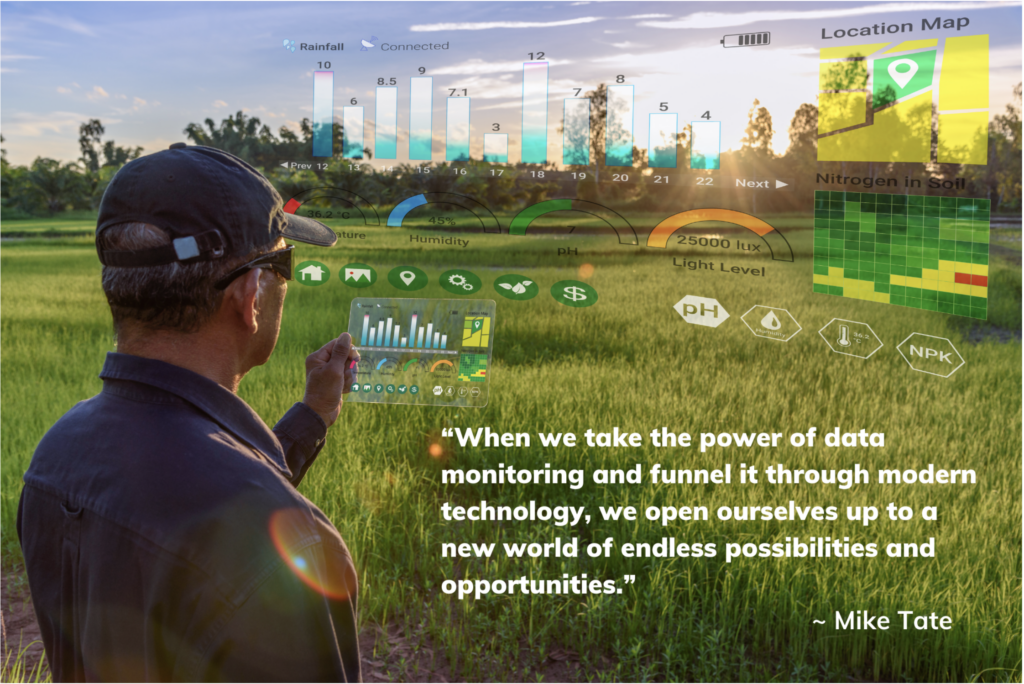
Excited by tomorrow, we face a new world filled with endless possibilities each day. Thanks to modern technology, simple sensors open the doors to our favorite restaurant, edge computing allows manufacturers to spot and correct production glitches before they happen, and high-tech traffic cameras analyze and record thousands of license plates daily to spot stolen and unregistered vehicles while also identifying suspected criminals. It’s no secret that the world is evolving before our eyes, and through the technological advancements of this digital era, we are creating a more efficient world. The power of data Data is a powerful tool of knowledge, and lucky for us, it’s everywhere! Every one of our actions is driven by a manual process of data – like the simple act of putting on a jacket when it gets cold, or an automated process of data – like a valve instinctively shutting off when a water tank gets full. Today we have the technology to effectively process, analyze and distribute data metrics in tremendously impactful ways. What does greater simplification look like for industrial leaders? Remote operations simplified When leveraged effectively, industrial internet of things (IIoT) solutions take remote operations to the next level, simplifying the work process for teams and industries across the globe. Think about some of the most popular high-value remote assets today, like drones, video surveillance, or even center pivot irrigation systems – these entities perform so well because they do what humans can’t. In mere seconds, IIoT technology can process, distribute and respond to data that would otherwise take an entire team hours, days or even weeks to achieve. In the not so distant past, industrial operations relied solely on data consumption (i.e., how much water is in the tank; what temperature is the water), but today, advancements give us the ability to respond nearly instantaneously to that collected data with actionable execution. Today we can view and control the management of an entire operation remotely on our cell phone. We can see how much water is in a tank or what temperature that water is at and automatically change and adjust the water levels and temperatures from near or far. As a result, the amount of time, resources and energy needed to run businesses has transformed entirely, and this evolution allows us to create an enhanced world and standard of work. Simple deployment Remote operations are oftentimes in rugged terrain, making them difficult or even impossible to access. At FreeWave, we solve this complex issue by providing pre-configured ready-to-deploy solutions, complete with everything needed to achieve the mission at hand. For example, through FreeWaves’s joint venture with ModuSense, we’re simplifying connectivity to cloud with a variety of pre-configured and ready to deploy monitoring and sensing solutions by supplying the entire solution with a 12-month data plan, dashboard, 12W rapid recharge solar panel, satellite connectivity and Bluetooth connectivity. You can use your mobile phone to validate the data directly from the gateway without having to wait for satellite transmission. We all know the “gotchas” when it comes to buying technology. Simple deployment means you’re ready from day one, without needing to buy additional components. Real-world impact As Chief Operating Officer and SVP of Global Sales and Marketing at FreeWave, I get a front-row seat to the real-life impact modern-day technology is having on lives, businesses and entire industries. The essentials of life have become simplified, and in the process, more people and businesses receive greater access to the things that matter most like critical information, metrics and potential outcomes. Creating a more sustainable world and preserving natural resources like food, air, energy and water have been at the forefront of IIoT since FreeWave began almost three decades ago when we brought long range, low power consumption, C1D2, 900 MHz connectivity and radio technology products to our customers. Since then, our connectivity options have greatly expanded by adding EDGE Compute, Software, Industry Protocol Conversions, Data Broker & Cloud, a complete end to end solution and with it comes the responsibility for greater environmental stewardship. We’ve all seen the devastating impact an environmental catastrophe, like the 2010 Deepwater Horizon oil spill, can have on the globe. Simple mistakes can and do cause enormous repercussions that affect us all. The truth is, with human interaction there will always be the cost of time and possible room for error. Technology, however, is different, as it allows us to not rely solely on human capacity and depend more on interconnected and advanced systems. Now, we don’t have to wait for someone to run into a situation or crisis and manually pull a lever or travel to turn off a valve. Instead, preprogrammed automation or a simple click of a button or flip of a switch from virtually anywhere in the world can control your high value remote assets. FreeWave is a technological pioneer in the 21st century. We have connected the unconnected with a reliable ecosystem of edge intelligent radios and solutions to optimize the extreme edge of remote industrial operations. Through our single IIoT platform, we provide expanded capabilities for data capture, analysis, control and automation. Our single pane of glass approach provides a simple, single vendor, one-stop-shop solution for remote operations worldwide. At the end of the day, when we take the power of data monitoring and funnel it through modern technology, we open ourselves up to a new world of endless possibilities and opportunities. It’s one thing to have data; it’s an entirely different thing to know how to leverage that data. At FreeWave, we are constantly pushing the boundaries of data monitoring and modern technology through our IIoT solutions and creating a better, safer and faster world of work for industries around the globe.
Data Connects Life: A Deeper Look at the Power of Connection for IoT Champions
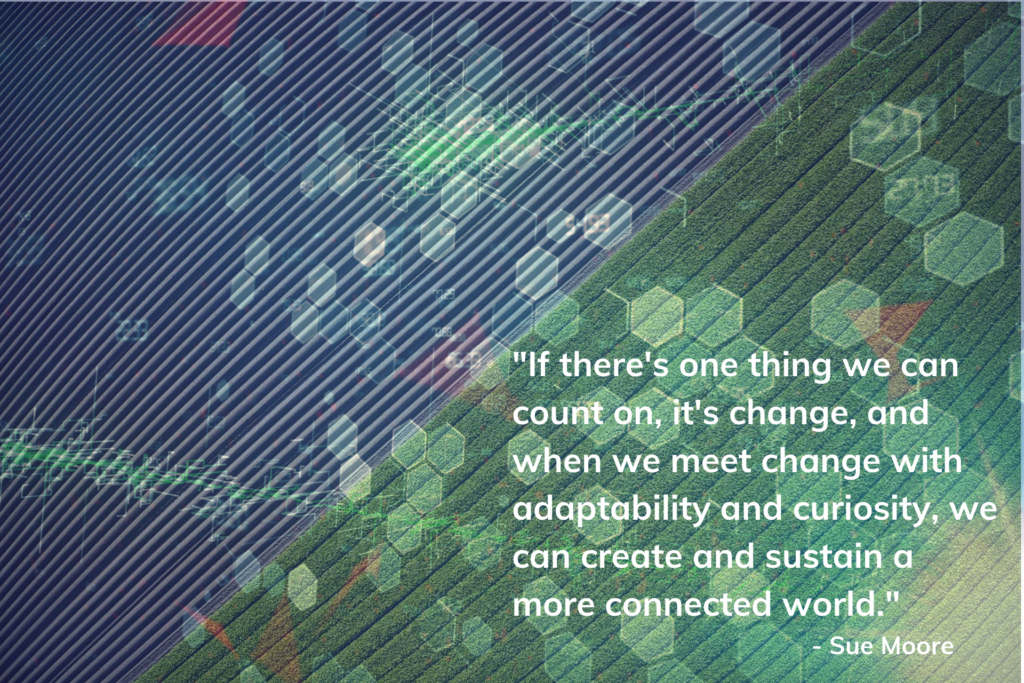
Every day, the world shifts in a new digital direction, making our lives simpler and equally more complicated all at the same time. I can vividly remember the introduction of email. I had just started my career in tech, and I kid you not, my coworkers and I questioned the efficiency of this new digital communication system. Back then, taking the time to craft an email, when I could easily make a phone call or walk to the office next door, felt foreign and unproductive, but now, decades later, I can’t imagine my life or work without the power and ease of email communication. If there’s one thing we can count on, it’s change, and when we meet change with adaptability and curiosity, we can create and sustain a more connected world, one where technology invites us to innovate, collaborate and engage with each other and the environments we live in! More technology. More data. The Mckinsey Global Survey has found that our global response to the pandemic has accelerated the rate of technology by several years. What does that mean for real people? Over time, we have discovered a new world filled to the brim with data that both informs and transforms our day-to-day lives. From smartphones to traffic management systems, the Internet of Things (IoT ) is revolutionizing life as we know it, connecting us to more people, places and systems than ever before. Connection is a powerful tool, and when harnessed effectively, it can change the world. The interdependent relationship between our natural and digital world is quite profound; in today’s society, we operate as one. In smart agriculture, for example, effective data can make a significant difference in overall crop and herd health, which, in the end, affects us all. Whether we’re on the farm, on an oil rig in the middle of the ocean or in our own backyards, technology connects us. Data is everywhere, and when this data is measured and distributed carefully, it transforms entire industries. Accessing the data you need on your terms For the last 28 years, FreeWave Technologies has pioneered a unique IoT revolution, reinventing the way industrial IoT is used in the modern market. We connect the unconnected with a reliable ecosystem of edge intelligent radios and solutions to optimize the extreme edge of remote industrial operations. Through our software, we provide IoT champions with real-time data insights to create better and more sustainable businesses. To achieve transformative operational optimization, industrial leaders need visibility into data and the ability to proactively manipulate that data and act on the insights gained from it. Our vision is to build an ecosystem of edge intelligent radios and solutions to transform the extreme edge of industrial operations into a connected part of their enterprise. Our integrated edge connectivity and computing solutions provide expanded capabilities for high-fidelity data capture, analysis, control and automation via a single industrial IoT platform that is readily scaled as each edge computing need evolves. We call it a single pane of glass. With a legacy of solving thousands of customer changes across multiple industries and deployment in 39 countries, the goal is to continue to future-proof operations so that remote work becomes more autonomous and, dare I say, simpler. It all brings us more connected with our collective purpose to create a better and more sustainable world. Data connects life. The more we see, the more we understand, and the more we understand, the more equipped we become to make better decisions. As the Director of Marketing at FreeWave, I am closely connected to the people and operations most impacted by our work. I know firsthand how powerful connection is for the IoT champions we serve, and every day I witness the power of data to transform the world. Putting it in perspective Take the water and wastewater industry, for example; in this industry, clear and controllable data insights are key to achieving effective operational management. At FreeWave, we provide these actionable data insights such as moisture levels and weather predictions through our sensor and weather monitoring technology, which ultimately allow water and wastewater industry leaders to be proactive in their business rather than reactive. A proactive and informed approach to operational management makes the difference in creating a more sustainable environment, and a more sustainable environment transforms our communities and the surrounding world. FreeWave’s productivity technology is removing barriers to data and helping industry leaders solve unique challenges like never before. Where some people may only see tech software – a little box with some wires, chips, and sensors – a much deeper reality occurs. We are all connected, and today, IoT champions get to leverage the power of this connection, along with technology and data, to create a better world, one industry at a time. I am so proud to work for a company that is connecting the world in unique and innovative ways. Every day, I see the impact of technology and what it means to be more connected through data, giving us critical insight. What we do with that data is where the magic happens. This is where we can use connectivity to push boundaries for greater innovation, make best use of our people, create safer work environments by understanding what’s happening in hard-to-reach terrain, and even take bold action to architect a more sustainable world.
Automation in Oil and Gas: A Starter’s Guide
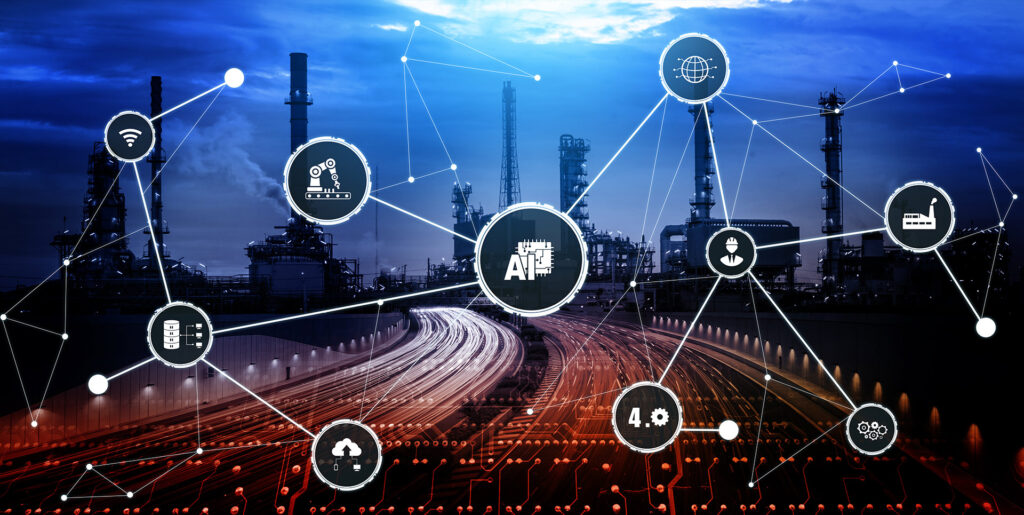
From drilling to logistics to preventing theft, automation in oil and gas is quickly becoming the standard. Learn how tech helps increase ROI and improves safety in this starter guide. Since the 1990s, businesses have looked at how automation in oil and gas can improve worker safety, improve efficiency, and increase the bottom line. Today, digital tools are being used in every facet of oil and gas cultivation. From improved efficiency when drilling for new oil to real-time weather monitoring and theft prevention, tech tools are quickly becoming the norm for the $2.1 trillion (according to IBISWorld) industry. In this starter guide, you’ll learn how innovation and automation in oil and gas is being used to connect, collect and analyze data, and increase ROI. What Is Automation In Oil and Gas? Oil and gas automation refers to the growing number of digital techniques and processes used to help producers cultivate energy. Automation and agility have found their way into nearly all oil and gas industry divisions, like drilling, logistics, supply chain, and safety. Tools such as rugged wireless radios and AI-powered real-time sensors for remote monitoring allow drilling sites to be run safely and efficiently from afar—protecting employees and increasing revenue simultaneously. Benefits Improved production yield while lowering costs Improved safety for employees in hazardous conditions Real-time insights 24/7 monitoring Theft protection at drill sites and along pipelines Sustainability Predictive technologies can be used for future application Where Does Automation In Oil and Gas Happen? Approximately 94 billion barrels of oil are produced every day worldwide, according to U.S. Energy Information. Here are some specific examples of how automation impacts the production and monitoring of two of the world’s most important resources. Drilling Autonomous drilling control systems (ADCs), such as those implemented in the North Sea (between England and Scotland) in 2020, enable safe and efficient oil drilling. In the past, “automatic” tools used to drill for oil were just manually assisted. Today, though, ADCs are believed to reduce drilling costs by as much as 50 percent. Diagnostics In an industry where downtime can severely disrupt a business and lead to financial downfall, remote diagnostics help predict future issues or pinpoint current ones to prevent delays and disruptions. For example, tools that measure pressure loss, temperature, and mercury levels can help businesses disrupt downtime and minimize costly delays. They also reduce the risk of oil rig disasters, such as the infamous Gulf of Mexico explosion on the Deepwater Horizon oil rig that left 41 miles of oil in the ocean. Weather Monitoring Oil and gas production are both contingent on weather patterns. Issues that can affect (or even shut down) drilling sites include: Tropical cyclones (most common) Extreme cold Extreme heat Earthquakes Automation in gas and oil includes the adoption of real-time sensors and monitoring tools, which detect changes in seismic activities and atmospheric levels, giving companies the ability to adjust in real-time to changing weather patterns. Security Theft in oil and gas is a real threat. In fact, a 2021 report said that Nigeria loses an average of 200,000 oil barrels per day (b/d) to theft, primarily from pipeline sabotage. Rugged, wireless radios allow oil and gas professionals to communicate safely without fear of interception or lost connection. Along with real-time monitoring of sites and pipelines, this can create a formidable defense against criminals. Trends in Oil and Gas Automation Oil and gas automation is quickly becoming standard, and with it, innovation in the field is coming. A significant push towards sustainability. Tech tools that help reduce a business’s carbon footprint and improve operating efficiency will be both sought after (and possibly required) in the coming years. Greater use of AI at oil rigs. Businesses are shifting away from manually assisted technologies in favor of artificial intelligence devices that make real-time, autonomous decisions on-site. More tech jobs. As on-site employees are phased out to make for a safer work environment, new jobs, such as coding, system architecture, and cybersecurity, will be created in the oil and gas industry. Contact FreeWave to learn how our technologies can boost your oil and gas business’s ROI today.
9 Critical Reasons to add Wireless Thief Hatch Management
A thief hatch is a closeable lid at the top of a low-pressure holding tank for hydrocarbons such as oil or condensate, or water. It allows access for measurement, however, if left open it can allow hydrocarbon vapors to escape into the atmosphere as fugitive emissions. Hydrocarbon tanks are almost always Class 1 Div 1 hazardous locations. If your thief hatch pops open from overpressure conditions, or if an operator accidentally leaves it open, you could be in violation of strict air pollution compliance rules on fugitive emissions. The Colorado Department of Public Health and Environment (CDPHE) Regulation 7, Section XII, “Volatile Organic Compound Emissions from Oil and Gas Operations”, requires facilities to control venting of natural gas from many oil and gas emission sources. The CDPHE has determined that improperly secured thief hatches, visible emissions from a flare, and audible emissions from a thief hatch or pressure relief device (PRV) are violations of Regulation No. 7. Many of the 23 oil producing states (including Ohio, Utah, Wyoming) are looking at the CDPHE rulebook as a possible blueprint for their state rules. The minimum fine by CDPHE for an open thief hatch, visible emissions from a flare or audible emissions from a thief hatch or PRV is $15,000/day. The duration of each fugitive emission violation is assumed to be at least one day unless evidence gathered by the CDPHE and/or provided by the source proves otherwise. The USEPA’s new regulations affecting methane (CH4) and VOC emissions from the oil and gas sector became effective August 3, 2016. Updates to NSPS OOOO list storage thief hatches as one of the fugitive emission leak components that will be periodically checked for leaks using optical gas imaging (OGI). Thief hatches are usually easy to see and make easy pickings for regulatory compliance inspectors. Inspectors will often check thief hatches first, and use them as indicators of other violations for a site. Open thief hatch detection is a powerful tool to minimize fugitive emissions. Most solutions on the market to detect an open thief hatch are wired and expensive to install and integrate into an existing SCADA system. FreeWave delivers an inexpensive and easy to deploy Class 1 Div 1 wireless solution for Thief Hatch Monitoring with the WC30i-AXIS Angle Sensor. FreeWave’s new WC30i-AXIS Wireless Angle Sensor is a solid-state inclinometer that measures the opening angle of a Thief Hatch and reports as closed, cracked or open. It links wirelessly to the WC45i Gateway, which communicates to the PLC or SCADA system with Modbus communication protocol. Together with the WC45i Gateway, the WAVECONTACT system is easily and quickly deployed to implement industrial automation where wired installations are cost prohibitive. The WAVECONTACT System has been designed for deployment in Class 1 Div 1 locations. Contact Sales to Learn More
Injecting Agility and Automation at the Well Pad
Small-to-medium-sized oil and gas companies understand what it takes to be agile. They must survive and thrive in an industry led by giant producers. While no recipe to success is the same, the smaller players need to maximize production while simultaneously keeping costs down if they want to compete in the market. By adopting technology solutions that will make them agile and effective, these organizations can secure fast and significant ROI, while meeting production and operations demands. However, technology selection in a constantly changing landscape is murky at best. Take an operations manager at a small oil and gas company, for example. They are likely tasked with ensuring that operations are running smoothly at the wellhead while delivering critical data back to the business office in real time. It seems simple enough, but the operator is probably facing constant pressure to provide insights into their production sites and new solutions for operational efficiencies. At the same time, the IT team wants monitoring at the well pad 24/7/365, and they want to access that data whenever they please from anywhere. Perhaps, they have attempted to tack on several different technology solutions to help provide said data – but the new demands require a more sophisticated approach. The pressure is on to find a way to optimize data collection, monitoring and control of the assets in the field (including the communications network) or the company won’t be able to compete with the “always on” oil and gas producers. The good news is that there is hope. There are programmable wireless communication solutions for the well pad that are available today. With a little research, it is possible to find a rugged, easy to use solution that will deliver massive ROI. What Does Well Pad Automation Look Like? In modern oil and gas operations, well pad automation builds analytics and intelligence into the wellhead environment. This takes a step beyond traditional communications because it enables intelligent applications and programmability that establish an advanced operating environment. Automation can also present the opportunity for predictive analytics, remote command and control, new protocol translations, and modern cloud-based services at the wellhead. Automation helps an operator streamline their job and provides the IT decision makers with data that helps them understand daily operations. Automation technology makes this possible by powering data transmission, improving data quality and enabling intelligent data analysis. The oil and gas company then has the power to make informed decisions that drive higher production outputs, with ROI often achieved in a matter of months, along with substantially lower CAPEX. Bringing an Automated Monitoring System All Under One Roof The financial and business benefits of industrial automation are clear, however selecting technology solutions can be challenging. Operations managers need a wireless communication solution that can support next generation of well pad automation needs. The solution must include a combination of data monitoring, logic execution and data visualization. This is especially beneficial at the well pad sites that are remote and isolated. The big advantage today is that these decision makers are no longer limited to disparate technology solutions: Wi-Fi Automated Monitoring Systems establish Wi-Fi at the wellhead to enable voice, video, sensor data access and perimeter security. They can also leverage Wi-Fi for rapid maintenance across the wellhead, saving maintenance staff hours of time. Instead of driving to the remote wellhead, they are now troubleshooting issues from a truck or office. Wi-Fi also supports the collection of information from RFID devices and wearable devices designed to protect workers in the field. FHSS When the Wi-Fi is bridged with a Radio Frequency (RF) solution, particularly Frequency Hopping Spread Spectrum (FHSS) technology, the data can then be collected from tank farms, PLCs, and sensors on the well and within the well. The wireless intelligence that is located on the devices in the sensor network, enables local execution on the RF devices, which supports data storage or data collection and analysis. Through cloud-based services, the data can be published globally, allowing mobile access from virtually anywhere. Additionally, an automated monitoring system may enable wireless telemetry in hazardous environments through modular wireless I/O solutions that leverage sensors to monitor specific points along the wellhead. Programmability With built in programmability on top of Wi-Fi and RF technology, the automated monitoring system is not only optimizes today’s operations, but it prepares the organization for the future as industries shift towards digital technology and total connectivity. For example, an engineer can write a simple application using open source technologies like Node-RED and Python that will display a dashboard of real-time data from the well pad as it collects information from sensors. The organization could also automate tank-level monitoring by developing or leveraging a third-party application to monitor water levels in the remote tanks from the cloud – which would then be accessible anywhere with a wireless internet connection. Benefits that Stretch Beyond ROI Automation at the well pad not only leads to ROI through wireless automated monitoring and control, but it has the power to transform operations and streamline production. When a small-to-medium-sized oil and gas producer leverages automation, they can make highly intelligent decisions through the technology features that enable enhanced monitoring, logic execution and visualization. They can also leverage these solutions to create a more secure operating environment and communications network. These solutions note only benefit the operators today, but they prepare them for future technology needs.