Hackathons Giving Birth to Innovative IoT Solutions
One of the fastest growing spaces in tech is the world of connected devices — often called the Internet of Things. In the embedded engineering and software development worlds, this technological shift is so pervasive some have taken to called it “The Internet of Everything.” While organizations and enterprises are increasingly putting the IoT at the root of many of their forward-thinking business strategies, one of the strongest engines of innovation stems from hackathons. Hackathons are essentially software or hardware challenges, where teams of developers or engineers are giving a task (i.e. build a smart city solution), with specified hardware or software (maybe a certain development board or programming environment), in a specific time period (anywhere from a few hours to a few days). In today’s top IoT news, we’ll take a look at a few stories in the industry about hackathons and how they are helping shape the IoT. Functional Fabric Hackathon Leads to eTextiles Innovation One of the fastest growing areas of the IoT revolves around smart clothing — sometimes called eTextiles. Smart clothing can range from simple solutions like integrating sewable LEDs into clothing to craft safer bicycling attire, to embedded sensors that are used to monitor environmental conditions for oil and gas workers. Recently, as noted in this article from “The University Network,” the Massachusetts Institute of Technology hosts a hackathon focusing on “Functional Fabric.” MIT has long been a hub for IoT innovation and is one of the epicenters of eTextiles. In the Functional Fabric Hackathon, teams of students faced the challenge of design clothing solutions that would aid soldiers, first responders and victims of disasters. The teams had three days to come up with their solutions and were competing for two grand prizes of up to $15,000. 22 teams competed and the winning solution came from an MIT student group called “Remote Triage.” Their solution was a sensor system that could be embedded in a soldier’s uniform, that would monitor not only vital signs, but could then report any injuries to field medics, provide location of the injured soldier, and even triage the severity of the injury with a color coding system. Hackathon Challenges Young Women to Build Smart City Solutions “She Builds Tech — Smart City Hackathon” recently challenged young women in India to build the smart city solutions of the future. As noted in this article from The Hindu, there were ultimately five winners — a solar energy harnessing paint, a water grid solution system, geo-fencing, a smart ambulance service, and a routing and scheduling system for tourists. The event lasted for two days and attracted over 300 girls from various engineering colleges. TechCrunch Disrupt Hackathon Coming in Mid-September TechCrunch Disrupt, the event that has becoming one of the world’s biggest stages for innovative new technologies, is rapidly approaching, with the San Francisco version of the event scheduled to kick off on September 12th. The hackathon will pit teams against each other in a two-day sprint to design the most impressive tech. At the end of the hackathon, teams will have just 60 seconds to impress judges for their shot at a $5000 grand prize, a slew of gifts and gadgets provided by sponsors, and all the glamour that goes along with winning one of the countries most elite hackathon competitions. To learn more about the hackathon, or to grab tickets to watch the action, check out this article from TechCrunch. — Hackathons continue to prove that innovations in the worlds of IoT, embedded engineering, and software solutions do not have to come just from the prototyping labs of Fortune 500 companies, but can emerge from groups of students and tech enthusiasts faced with big challenges and short timeframes.
The Next Generation of IIoT: Micro & Macro Connectivity
From a consumer standpoint, the impact of IoT connectivity is clear. People can purchase smart home systems and automobiles with increasingly autonomous features. Looking at the potential changes to our daily lives in the coming years, all things point to connectivity. We are eyeing a future where we can monitor and control our homes, vehicles and business around the clock. The news stories are exciting and tangible because new products are frequently unveiled and we see them being used in our everyday lives. This impact has spread beyond the scope of the consumer market, which ultimately led to the Industrial Internet of Things (IIoT). Traditional businesses, like those in utilities, oil/gas and agriculture, face a future that has the potential to transform entire industries due to the power of digital disruption. Despite the growing pains and challenges of “going digital,” industrial businesses face almost limitless potential to streamline operations and control large distributed networks with a level of precision that was previously impossible. As these industries pick up on the value of data and connectivity, next generation applications have emerged that will drive competition and increase productivity. Data and analytics will be available via the cloud and accessible from any device. And even better, the quality of data will be controlled through automation and the incorporation of third party applications. What this means for businesses is they will be able to monitor their networks on a micro level. This allows problems to be stopped in their tracks and for precise process adjustments that streamline operations. With third party applications, there is not only substantial business opportunity for developers, but there are endless possibilities for process control, security and operational apps that will drive down costs and support increased production. Most business decision makers are aware that there is no stopping digital transformation because research shows that it’s already happening. Many businesses are in the process of digital transformation and have already thought about these next generation systems and the research proves this: 75 percent of IoT providers say that big data and analytics are among the top skills they look for when adding talent to their teams. 50 percent of companies look to hire specialists in mobile development. A recent TechBullion article states: “they already have noticed the close relationship of mobile and IoT and plan to launch IoT projects for their businesses within the nearest 5 years.” Gartner says that by the end of 2017 demand mobile application development will grow five times faster than the number of IT companies able to meet this demand. A new report from Frost & Sullivan anticipates a trend in the transition from connected devices to the use of cognitive or predictive computing and sentient tools in the next 12-18 months. So what does this mean for industrial business? It means they need to invest now in the communication technologies that will deliver the data that is absolutely critical for future networking needs. It means they need to think about how they can enable programmability at all network endpoints – even at the edge. And lastly, it means they need to start working through the challenges of a digital shift now so they are prepared for an automated, connected future.
Node-RED: The IoT Programming Language No One is Talking About
Sussing out the key pieces of the Internet of Things is usually accompanied by caveats ranging from the established uncertainty of the future, the security problems of the present, and the legacy system integrations of the past. Industry gurus and thought leaders predict growth in the billions – dollars, devices, deployments, Cloud applications, etc. Networking experts waffle on standardization. Hardware providers sprint to keep up. But one of the critical pieces of the Industrial IoT is something you won’t find jumping off front-page headlines – yet: Node-RED, the programming tool for wiring together hardware devices developed by IBM, is the power behind the IoT throne, and no one is really talking about it. Lost amid the noise about ‘smartifying’ the world is the practical reality that unless you can figure out a way to seamlessly connect the hardware devices that comprise a smart network, you are essentially relying on the Cloud to run an overwhelming number of disparate applications – and that is assuming your network is near invincible. Since the Industrial IoT relies, in theory, equally upon Cloud and Edge device processing, developing software applications that can effectively run in both settings is crucial. This is where Node-RED comes in. According to Nodered.org, the open-source Node-RED ” … provides a browser-based editor that makes it easy to wire together flows using the wide range of nodes in the palette that can be deployed to its runtime in a single-click … [making it] easy to wire together flows using the wide range of nodes in the palette.” The essence of this tool is that engineers and operating technicians can create and configure applications easily, in real time, on Edge devices. Ideally, the pieces of code being used to create programs are reusable, meaning that the process can be learned by field operators without the need for a degree in computer science. The code is built on Node.js, the JavaScript runtime that frequently pops up on Raspberry Pi platforms due to its ease of use. So, if it is so easy, and so important, why is no one talking about it? The ongoing problem for the IIoT is the Wild West mentality: the no-holds-barred land grab has resulted in disparate hardware and software products that often require a combination of proprietary and open-sourced solutions. As a result, the actual mechanisms that drive the building of an IIoT network are often less talked about than the tangible pieces that come together to build that network. There are several considerations to keep in mind. First, the idea of IT/OT convergence has only just started to gain traction, so legacy solutions (especially in certain industries) haven’t quite crossed the threshold of multi-function. Second, the changing demographic of the workforces in the industrial sector means that the traditional gatekeepers, often not versed in software or computer programming, have been loathe to adopt solutions that require a whole new skill set. The result is that the idea of programming between devices and Cloud applications is in a relative infancy. Third – and still related to the workforce demographic – creating an entire workforce of people versed in both hardware engineering and computer programming is impractical. Those factors, along with several others related to the need for network functionality and data analytics, means that a solution like Node-RED is still not completely understood, and perhaps even more pertinent, still not widely adopted by industry leaders on both the hardware and software side. But it also means that it is more necessary than ever.
FierceWireless: FreeWave Delivers Rugged IIoT to Mount Washington Observatory
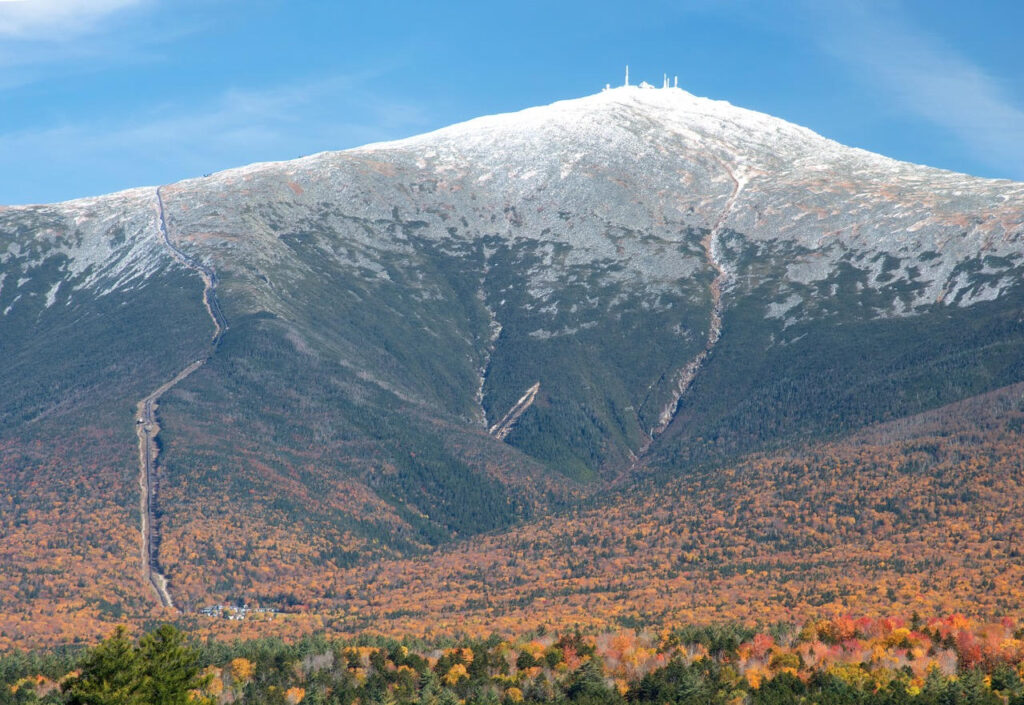
Earlier today, FierceWireless published an article highlighting a recent joint case study from Mount Washington Observatory’s use of FreeWave’s FGR and FGR2 radios to collect vital climate data. Editor Monica Alleven pointed out several key factors that drive the success of the project: FreeWave says it’s known for its ability to maintain connectivity in environments where other technologies have succumbed to the elements. At Mount Washington, FreeWave’s FGR and FGR2 radios connect a network of 28 sensors and devices on five remote weather stations and deliver data in spite of the area’s year-round harsh weather. The weather stations are solar-powered and only receive sunlight 40% of the year, another reason that FreeWave’s low-power solutions are ideal for the network. According to Freewave, these capabilities have enabled 24-hour, year-round network connectivity. To read the full article, visit FierceWireless: http://www.fiercewireless.com/wireless/freewave-delivers-industrial-iot-at-mount-washington-observatory-n-h To read or download the Mount Washington Observatory case study, visit: https://www.freewave.com/mount-washington-observatory/ FreeWave also recently published a joint case study with the British Antarctic Survey, which uses similar ruggedized IIoT technology to aggregate and transmit data reliably in conditions that could arguably be called some of the most extreme on the planet. As with Mount Washington, FreeWave’s FGR and FGR2 radios are the backbone of the network deployment, as they have consistently proven to function in temperatures well below the approved -40 degrees Celsius. To read or download the British Antarctic Survey case study, visit: https://www.freewave.com/case-studies/british-antarctic-survey/
Rugged Wireless Radios for International OEM Applications
For original equipment manufacturer (OEM) and military applications around the world, operational success requires reliable data delivery. This 100 percent achievable with rugged wireless radio solutions. As Industrial IoT pushes for more connectivity, coupled with the surge in commercial use of unmanned aerial systems (UAS), the pressure for around the clock command and control (C2) links is higher than ever – and it’s happening on a global scale. To support these growing needs, FreeWave has announced the general availability of the MM2-5 Watt 1.3 GHz (13X5W) integrated radio. Offered in a small package for ease of integration, the MM2-13X5W features an external 5 Watt output, making it ideal for UAS, OEM and military applications where reliability is paramount and space is at a premium. These solutions can be leveraged to deliver important data in the U.S. and abroad for a wide variety of mission critical applications. The MM2-13X5W has a lot to offer starting with it’s built in versatility and the ability to function as a gateway, endpoint, repeater or endpoint/repeater. Security is a priority – each MM2 13X5W is equipped with proprietary frequency hopping spread spectrum (FHSS) technology. It also features a line-of-sight range of up to 90 miles, and can be deployed in international settings where lifesaving communications and security are paramount. A number of these use cases include UAS applications, soldier training, environmental monitoring and other government and defense needs. Next Generation UAS Applications As the commercial drone market rapidly expands, the number of use cases is filtering into new markets. Beyond the military scope, commercial UAS applications have the potential to completely transform the monitoring, control and data analysis processes for many industries. The MM2-13X5W is equipped to support this next wave of these UAS applications, including: Pipeline monitoring as a service – drones can help maintain safe and consistent visibility of the pipeline and deliver that critical data to the network. The small form factor and proven reliability means uninterrupted data transmission in remote settings. Homeland security apps – recently, in the U.S., there have been many heated conversations around border protection. Many drone supporters believe that UAS can offer a cost effective way to monitor the nations borders. The U.S. border patrol even recently solicited contractors to build facial recognition drones. Drone delivery service – As we look at the future use of commercial UAS, drone delivery is a popular topic of conversation. We’re also seeing use cases where drones can deliver food and medicals supplies to high risk areas in third world countries. Precision Agriculture: Drones can enhance crop visibility, enabling smarter decisions and more food output. The potential impact of drones in precision agriculture is becoming recognized throughout the world. As the possibilities for commercial UAS continue to multiply, so does the need for secure C2 links for successful operations – and this is where the MM2-13X5W is an ideal solution. Additional Product Features The MM2-13x5W also features the following: 115.2 and 153.6 kbps selectable RF data rates TDMA, Super Epoch TDMA, and AES Encryption Performance tests from -40 degrees Celsius to +85 degrees Celsius Data link range up to 90 miles For more information about the MM2-13X5W, please visit: https://www.freewave.com/mm2-m13-series/
5 Reasons Why Your IIoT Network Needs Wireless Programmability
If your company is grappling with the shift towards wireless connectivity and automation, you’re certainly not alone. As more processes are automated, especially within industrial markets like oil and gas or utilities, data has become a valuable asset that provides critical information for operations and performance. Up and coming industry leaders are pushing for modern Industrial IoT (IIoT) networks, as the older, more traditional workforce heads towards retirement. As a result, the processes of yesterday are being phased out – especially when it comes to choosing between hardwire and wireless for remote deployments. For many, wireless solutions have been accepted for some time as the primary means in which data is collected, transported and analyzed. Frequency Hopping Spread Spectrum (FHSS)-based technology in particular is proven to be a reliable and maintainable wireless option. Now, however, we are facing an entirely new realm of opportunity with FHSS-based programmable wireless technology that is molding the future of data collection. Here are five reasons why you need to consider programmable wireless technology for your IIoT network: Bring it all to the Cloud – Programmable wireless solutions are equipped with the ability to incorporate custom, third party applications at the Edge. When we talk about the Edge, we essentially mean the outermost layer of the network. For industrial networks, the Edge is often a remote area where mission critical operations occur. In order for the business to capture a holistic view of their entire network, many have added sensors and other data-capturing devices at the Edge. By adding third party applications with new programmable wireless technology, businesses are able to expand automation capabilities, reduces costs, simplify operations and enable data transmission directly to a private or public cloud. Smart Data Over Big Data – The goal of achieving ‘Big Data’ is common practice in most modern IoT and IIoT networks. Decision makers recognize the power of data and know they need to receive it from every network end-point. We’ve seen this to be true purely in the proliferation of sensors and IoT devices deployed across the U.S. that continues to grow. Having programmability at the edge of the network offers a big advantage, because you have the ability to control of the quality of the data. Even better than Big Data is access to the specific, timely data that is most pertinent to your business operations. Robust and Reliable Technology: Programmable wireless solutions are equipped to embrace the future of data collection. The beautiful thing about these solutions is that the backbone of the technology is FHSS. This particular Radio Frequency (RF) technology has been proven in some of the most adverse conditions imaginable. These technologies are trusted by the government to maintain their links and have proven to operate in some of the most dreadful and intense environments in the world . Where performance is critical – these solutions have proven to work for decades and now programmable options can reliably bring this data directly to the cloud. Flexible and customizable– We are all privy to the fact that no two networks are the same. With programmable options, radio functionality is customizable to the specific needs of the network. Despite the variances, remote networks likely have one thing in common – data needs to be transported across significant distances. Programmable wireless technology is built to be deployed at nearly any point in the network where sensors are collecting data. This is an area in which traditional hardwire solutions almost always fall short, as most businesses cannot afford the cost of running hardwire to these remotes sites. Besides, there are wireless options that are built for easy installation and long-range communications that simply make the most sense for remote deployments. Meeting Modern Demands– Today, IT and OT departments are one in the same. These modern networks eliminate barriers which is conceptually great for operations. However, like any major disruption, convergence has created a number of challenges from visibility, to cultural difference, to security. To ease some of these tensions, modern wireless solutions are designed to drive connectivity for the entire network, and are even able to tie in legacy systems from the field. Many FHSS-based technologies offer secure-data transmission, and by leveraging the programmable wireless technology, and you can bring data to the cloud. Wireless technology is recognized as a necessary solution for remote operations. As IIoT networks mature, there are stark advantages in leveraging programmable solutions. Not only do they rack up cost savings and streamline operations, but they are deployed at the edge of the network with minimal hassle and are built to deliver in any environment.
Remote Tank Level Monitoring and Automation
Industrial livestock operations have several critical needs in order to function smoothly, but perhaps most important is also the most fundamental: water. On remote sites, tank level monitoring and automation are tools that can essentially make or break the entire operation. In many of these situations, the needs of the site managers are different, so in order to maximize the technology being deployed to drive the automation process, they need to be able to customize the functionality. For operations using radio communication networks, those radios need to provide maximum programmability in order to host third party applications specific to the needs of the site managers. We recently finished a deployment that serves as an excellent case study for remote site tank monitoring deployments and included some interesting uses of radio programmability: The operator of a Rocky Mountain based livestock facility approached FreeWave to assist in remote data visualization of water tanks that are vital to its operations. The pain point was that the tank levels could only be observed visually on premise. After consideration of the terrain (mountainous, remote and big temperature swings), sensors and communications infrastructure, FreeWave engineers recommended ZumLink IPR with the Node-RED programming language for intelligent tank data visualization via browser or mobile device. The facility has minimal to zero staff most of the time. If a fault occurs such as a leak that prevents a tank from filling, the facility operators are unaware until they visually inspect the remote faulty tank, located a half mile from property headquarters. The operators wanted to reduce the number of trips to the tank facility and remotely monitor all tanks via web-based browser or mobile device. For the complete case study, visit this link: https://www.freewave.com/case-studies/remote-tank-monitoring-automation/.
Do Drones Help or Hurt Wildfire Fighting?
Summer wildfire season is in full swing across North America, and the question of the utility of drones is once again in the headlines. The technology has proponents on both sides, but it has also been linked to several incidents, including the grounding of critical aircraft in a firefighting effort in Arizona. A key point of differentiation in this discussion is the use of personal drones, similar to the one mentioned in the article above, and commercial drones designed to serve a specific purpose in operations, similar to military or first responder deployments. The problem that firefighters face is the unauthorized use of personal drones, which can create dangerous situations for support aircraft like helicopters and tanker planes. Because firefighting aircraft fly at such low altitudes, they share the same airspace as commercial or personal drones, and at that altitude, one instance of interference can be deadly. A recent Quartz article pointed out the correlation between drone interference and the effect it can have on the people most impacted: civilians and the firefighters themselves: The drone problem has plagued fire departments for the last few years; In 2016, during Utah’s massive Saddle fire, a drone prevented firefighting planes from taking off—if the planes had been able to attack the fire from above, people would not have needed to be evacuated, according to Utah governor Gary Herbert. So far, in 2017, there have been 17 incidents of unauthorized drone disturbance in wildfire areas. In 2016, 40 such occurrences were recorded. In Colorado, firefighting crews are figuring out the most effective ways to use authorized unmanned aerial systems (UAS) to aid fire suppression tactics. When used in an official capacity, drones can be extremely useful. They can be used to survey landscape during a lightning storm when manned aircraft are grounded, or they can be used to deliver supplies to ground crews working in remote areas. Further, with new infrared technology, drones can be used to essentially automate the response protocol process to identify fires with the greatest threat potential, and dispatch the necessary resources before the fires explode out of control. Other leading-edge UAS applications for firefighters include drones that can be pre-programmed with Google Maps flight plans prior to launch, or drones that can stay in the air for hours with greater line-of-sight communications than ever before. The true difference between unauthorized and authorized UAS in wildfire fighting situations is the communication capabilities. When deployed correctly, authorized UAS can use TDMA technology to communicate with other aircraft in the area and ensure that no collisions or interference incidents occur. TDMA is a frequency channel access technique for shared communication networks, essentially enabling a more sophisticated way to drive Point-to-Multipoint communications. It allows multiple transceivers to access and share a single radio frequency channel without interference by dividing the signal into different transmission time slots. This enables swarming applications that enable multiple unmanned systems to operate autonomously, in tandem. For many personal drone users, the temptation to use this emerging technology to capture images or video is strong. Better cameras, greater operating distances and stronger communication capabilities have created a tool that can be both fun and useful for the average user. However, for wildland firefighters, the use of these unauthorized drones pose a serious threat to both their safety and the safety of the civilians they are tasked with protecting.
The Importance of Frequency Hopping
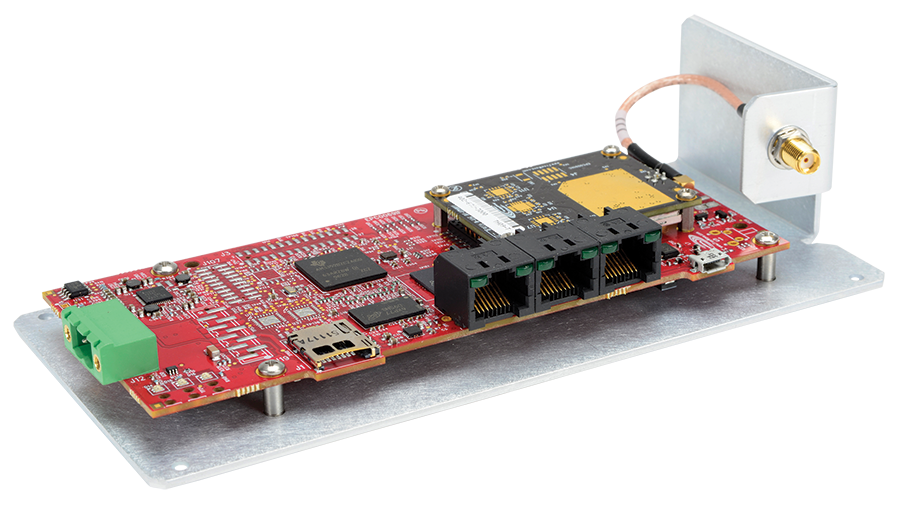
(Original blog can be found on the Texas Instruments website) Are you a fan of those 1940s black-and-white movies where a damsel in distress gets rescued by a rough-and-ready private eye? If so, then you’ve probably seen actress Hedy Lamarr. In real life, Hedy was no damsel in distress. She was one of the primary inventors of frequency hopping technology now seen in Wi-Fi®, Bluetooth® and code-division multiple access (CDMA). The technology Hedy Lamarr helped invent is frequency-hopping spread-spectrum (FHSS) radio technology. FHSS is a wireless technology that spreads signals over rapidly changing frequencies. Each available frequency band is divided into subfrequencies. Signals rapidly change, or “hop,” among these subfrequency bands in a pre-determined order. Used in global industrial applications for over 60 years, 900MHz FHSS radios equipped with TI’s chipsets like the SimpleLink™ Sub-1 GHz CC1310 wireless microcontroller (MCU) now have the ability to host process-automation apps for the intelligent command and control of remote sensors and devices. Without having to leverage expensive Wi-Fi bandwidth, lay fiber or employ cost-prohibitive cellular, companies can now take advantage of proven low-power FHSS technology to automate processes at the network edge. The proliferation of smart sensors and high-bandwidth devices makes low-power FHSS technology a viable and cybersecure wireless data option for oil and gas, unmanned systems (like unmanned aerial vehicles [UAVs] and robots) and original equipment manufacturer (OEM) wireless integration. Because innovators like TI have developed such powerful chips, FHSS is no longer restricted to pure telemetry or input/output (I/O). Indeed, FHSS increasingly supports voice and video, and can scale to form self-healing mesh networks. Moreover, FHSS transmits data over much longer distances than Wi-Fi, Bluetooth, LoRa or zigbee – up to 60 miles in some cases. Because FHSS is a wireless technology that spreads its signal over rapidly hopping radio frequencies, it is highly resistant to interference and is difficult to intercept. Interference at a specific frequency only affects the transmission during that extremely short interval, making FHSS inherently cybersecure. By employing intelligent TI-based FHSS technology, organizations can take advantage of real-world fog computing and intelligent edge communication devices that are cybersecure and resilient. When deployed as process-automation nodes, these devices (pictured in Figure 1) can make decisions and take action at the access level (or at the sensor or device). Indeed, not only is FHSS a reliable and robust option for Internet of Things (IoT) networks, it is also a low capex and opex solution that can work for years without maintenance. Contact FreeWave to learn more about FHSS technology and order a couple of TI-powered radios that you can program (in Python, Node-RED and Node.js) for real-world fog and edge applications. Also, find out more information about the CC1310 wireless MCU and other products within the SimpleLink MCU platform.
Rugged IIoT Solutions That Can Weather Any Storm
Mount Washington Observatory (MWO) is a research facility located at the heart of what many consider the “home of the world’s worst weather.” Think thick ice, dense fog, drifting snow, powerful winds, sub-arctic temperatures, rapidly changing conditions and more fog. The New Hampshire-based facility provides critical research data on the Earth’s climate and doubles to protect the lives of the MWO crew, US Forest Service Snow Rangers and New Hampshire Fish and Game employees by providing real-time weather updates. Collecting data is critically important for MWO operations and the safety of those it helps protect. In this vicious and unforgiving environment, FreeWave’s rugged IIoT solutions are responsible for delivering the data that is invaluable to research and safety efforts. Powering through Fog and Ice The extreme conditions at the MWO facility range from fog with 50-100 mph winds to sub-arctic temperatures that are accompanied by 140+mph winds and thick ice. The weather is known to change frequently and fast, with ice accretion rates of up to 12” per hour — and visibility is often limited or non-existent. These extremes make it the ideal location for studying the environment and climate. However, when search and rescue teams are deployed the situation can quickly become dangerous. They rely on MWO’s real-time data to assess conditions. As you can imagine, there is little room for connectivity issues when people are out in the elements. Ruggedized IIoT Solutions The key to establishing a network at Mount Washington is robust and hardened technology that will perform in the Summer and Winter extremes. For more than 13 years, FreeWave 900MHz spread spectrum radios have delivered the data that the crew relies on to survive some of the most intense weather in North America. While the technology is constantly exposed to the rough conditions, it performs day-in and day-out, providing critical data around the clock. Check out the full case study, including a description of the network here: https://www.freewave.com/mount-washington-observatory/