Why Choosing Zero Trust Network Access Over Virtual Private Networks is a C-Suite Decision
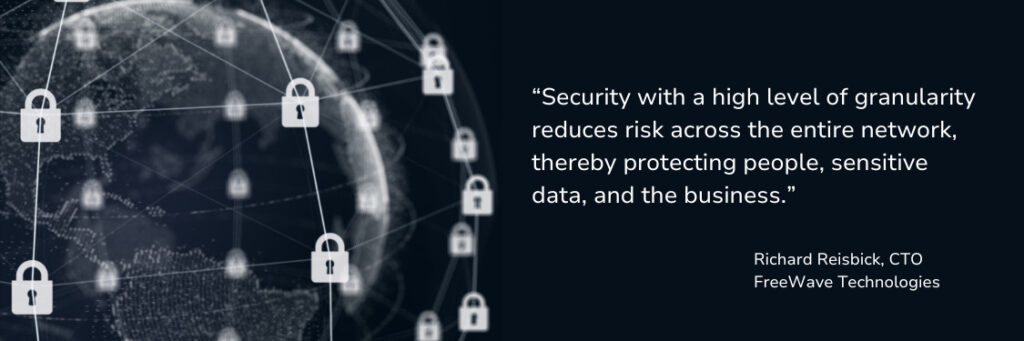
You’re leading the company. Why do you need to care about your business’ network security approach? The answer comes from something all too familiar: the accelerated rate of change – and the quest by modern leaders to build a resilient company. PwC describes today as the “age of continuous reinvention” in its 27th Annual Global CEO Survey report. One of the most startling findings is that 45% of CEOs do not believe their company will be viable in 10 years if it stays on the current path. Part of the challenge is knowing what could take your company down. Cybersecurity vulnerabilities at the network level is on the list. PwC’s report shows that CEOs who believe their organization is viable for more than 10 years perceive inflation (21%) and cyber risks (21%) as top threats with macroeconomic volatility (20%) just a half-step behind. As chief technology officer for FreeWave, part of my role is to find weak spots in a network connected to the industrial internet of things (IIoT). I talk to many senior leaders from companies in the oil and gas, agriculture, mining, water treatment and other remote industries. What’s the number one pushback I run into? They tell me they use virtual private networks (VPNs). I call this “pushback” because, at FreeWave, we don’t let VPNs into our data platform. At their most basic level, VPNs are used to create a secure connection between a user’s device and the VPN server. Through that connection, data is encrypted, and a user’s IP address is hidden. As a result, VPNs can allow remote users to securely access internal networks, including machinery, control systems, and databases. For those who may not be familiar with a VPN (although we’ve all probably used one at some point), here’s a simple analogy. Think of a VPN as a tunnel buried far below intersecting highways. One end of the tunnel is an IIoT device and the other end is the server. Your car (let’s make it a Maserati, while we’re at it) is a data packet. Instead of traveling across potentially dangerous highways where threats abound (a malicious attempt to steal your Italian beauty and hold it for ransom, as an example), you take the tunnel built just for you and other authorized drivers you trust. The challenge today is that the tunnel is no longer safe. Why Are VPNs Insecure? Technology ages faster than a male tsetse fly. Our tiny-winged friends hit their teenage years by week two or so. In contrast, technology ages by the nanosecond. I think the reason why many people use VPNs is the same reason hackers infiltrate them so easily. VPNs are old technology. They have long been the go-to solution for providing remote access to industrial control systems (ICS) and other critical infrastructure. They were born during the rise of the internet late last century. One solution begets other problems. The world wide web went from 3 million to 16 million users between 1990 and 1995 (today, there are 5.45 billion users, around 67% of the population). As a result, a group led by Microsoft sought a solution to growing security concerns. That’s how VPNs were born. To be fair, there are ways to make VPNs secure, but the enormous expense doesn’t make financial sense for most companies. Here are three reasons why VPNs cause concerns when protecting an IIoT network: VPNs have outdated authentication models. Username and a password is all you need. I can get into a VPN easily. VPNs are a single point of failure. If something goes wrong with the server, you can’t get in. If I’m a hacker, the best way to take down every remote access in the world is to take down the VPN server. VPNs are hard to monitor. The actual traffic on the network makes it hard to identify nefarious activity flying across it. Let’s say you have this machine on the edge (edge is simply the source of where your data is – this might be where oil is drilled in upstream oil and gas, for example). The data is being processed on that machine (edge computing) and is connected to the corporate network via a VPN. A disgruntled employee leaving the company can sit in their car and use their username and password to access the device through a cellular system. What is the potential damage? In 2020, several prominent VPNs experienced critical vulnerabilities that allowed attackers to bypass encryption and access systems. The Colonial Pipeline attack, for example, was traced back to a legacy VPN, according to then CEO Joseph Blount. The East Coast company paid hackers $4.4 million to restore service quickly. VPNs create easy targets. Once you’re in, you have free rein to do what you want. Solving the Challenge to Scale Network Security A report by McKinsey and Company predicts 50 billion devices will be connected to the IIoT by 2025. The pace of change, according to the report, has increased tenfold. This means the risks and insecurities behind VPNs for organizations, especially remote industrial leaders, are rising. I talked to a large agricultural company recently that uses a VPN. Here’s how the conversation went: Them: How can we add 20,000 sites to our system? Me: We’d have to add 20,000 VPNs. Them: Wait, what? Me: It’s really difficult. VPNs are hard to scale. One VPN is one thing, but many VPNs are a nightmare. We believe a better way to secure a network is to use Zero Trust Network Access (ZTNA). ZTNA creates a network fabric using the principle of least privilege access (PoLP). The premise: trust no one. Each user accesses only the data they need. See how the lens flips from inside out to outside in? In a ZTNA, each user has a policy. This means they are authenticated for access to specific areas. The disgruntled employee mentioned earlier? They cannot go anywhere in the fabric without authorization. Even better, that user’s access can be easily removed or revoked. Ever
The #1 Strategy Remote Industrial Operators Need to Win the AI Race
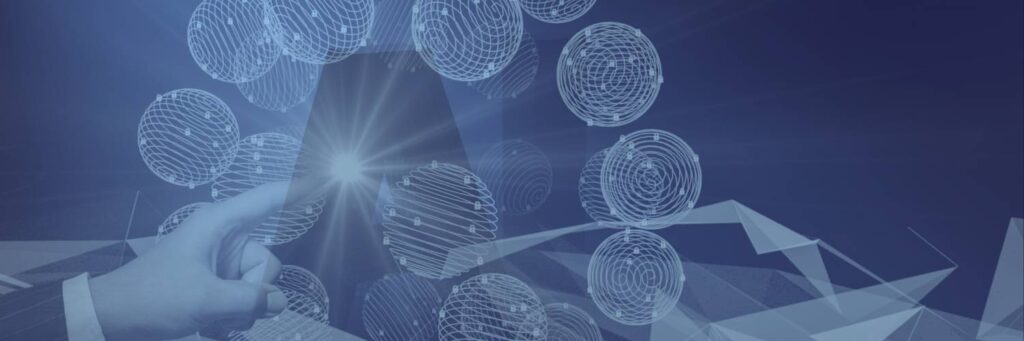
From the inaugural Olympics in 776 B.C. until today, one thing has remained the same: athletes bring gritty, physical prowess to their chosen sport – and the human desire for excellence. Of course, other things like culture, fashion, and technology have changed dramatically (thankfully, since athletes in the first Olympics competed naked!). In the Olympic Games Paris 2024, one game changer is the role of artificial intelligence (AI). Remote industrial operators looking to scale business value and improve decision-making through edge data, take note: the Olympics, watched by 3 billion people from around the world, is deploying AI to improve future performance of their event. According to an article published by the International Olympic Committee (IOC), AI and digital twinning are being used as an efficiency booster for future Olympic games – from energy consumption to identifying the best places to place cameras and power sources. “The expectation for a lot of people is ‘I’ll just AI it.’ It’s like a magic wand.” One thing AI demands is historical data. This is why we are so passionate about industrial operators owning their data. Without data ownership, it’s a false start when using large language models to train and leverage AI algorithms. In the article entitled “AI and Tech Innovations at Paris 2024: A Game Changer in Sport,” Ilario Corna, the IOC’s chief technology officer said, “We started gathering various operational data as far back as 2020, to look at how we can make the management of the Olympic Games more efficient.” Ryan Treece, global business development manager – data platform & AI solutions at FreeWave, has seen AI evolve over the past decade. He says companies that don’t give customers rights to their data are putting them at a disadvantage. “The thing is that those who own their data will eventually win because they can use it while others will start from zero.” Catching up over time, he points out, becomes increasingly difficult as competitors advance. Companies that secure data ownership today are the ones who will lead tomorrow or, in Olympic terms, will earn gold in the AI race. That’s one reason FreeWave drafted the IIoT Bill of Rights (data governance is amendment one) – as a way for remote industrial operators to leverage technology for future growth and opportunities. Importance of Data Ownership in the Age of AI Owning your data is not just a competitive advantage; it’s a necessity. “There are a lot of AI solution providers,” Ryan explains. “The expectation for a lot of people is ‘I’ll just AI it.’ It’s like a magic wand. Look into the future, though, and ask: What do vendors like? Reliance on their systems.” Ryan says there is no one “mega-solution” out there to solve every problem, but, if there’s one thing he hopes industrial operators know it’s that data ownership means leveraging your data for operational and business performance. “We’re targeting predictive maintenance to prevent machines from going down, reduce fuel waste just to see if a machine is running dozens or even hundreds of miles away, and increase efficiencies so people are not wasting time and energy resources. Data creates long-time success.” Just as the IOC is using AI to create more efficiency in the future, he says understanding data over time enables industrial operators to continuously improve. While still under development, FreeWave is building its AI solutions around domain expertise. Through its FreeWave® Insights™ data platform, it’s connecting decision-makers with data at the edge via sensor technology, pulling in SCADA system data as well. He cites vibration tension sensors as an example. If a rotating asset like a bearing, for example, wobbles, an alert is sent to a single pane of glass – a dashboard connected to the Insights data platform. From there, a technician can add the issue to his planning schedule. Ryan shares the story of when he lived in Michigan. An automotive manufacturer that made panels, a “tier one supplier” in the industry, didn’t have the budget to climate control the entire building. In hot, humid weather, the adhesive failed. Since variables change over time, he says, IIoT solved the problem. “Vibration and temperature data from sensors showed the numbers going up and down. Historical data tells us to change the adhesive or turn up the AC or ramp up the climate control when needed. The manufacturer and its solution providers knew what knobs to turn by identifying trends in a specific period.” That’s why, he says, data ownership is so important. Without data, AI becomes impossible. Solve – and Simplify – Operational Problems “We’re working on solutions that reduce the tech stack and address specific problems like predictive maintenance and trends analysis of sensor data,” said Ryan. “When I’m thinking data, I’m thinking of a huge Excel spreadsheet.” Real-time monitoring of temperature, vibration, or water levels, for example, are important variables for industrial leaders: oil and gas producers with fields in remote or rural areas, large-scale agricultural operations with water pump stations dotting thousands of acres, or public and municipal providers with aging infrastructure in need of robust, remote network strength. These are places, Ryan says, that pose a risk for people to perform daily or weekly monitoring. Ryan points to his hometown of Austin, Texas, where the energy grid is unreliable, especially during hurricane season or super hot summer months. The panels on the grid can overheat. Alerts notify engineers to replace components before problems start. Rather than react, alerts and predictive maintenance reduce downtime. Another example he gives is California where water is a precious commodity. Knowing humidity levels, soil moisture, and water consumption allows agriculturalists to invest minimal resources for better outcomes. AI, he says, optimizes sensor data locally, at the edge, by providing analyses crucial to decision-makers. Failure-Proofing Connectivity Keeps Data in Play Oftentimes, industrial operators don’t have ready access to cellular or Wi-Fi, however, satellite is an optimal solution for areas with questionable coverage and those wanting a strong back-up connection. Pairing satellite with the FreeWave cloud-based Insights platform-as-a-service
Industrial Operators – You Own Your Data and Then Some
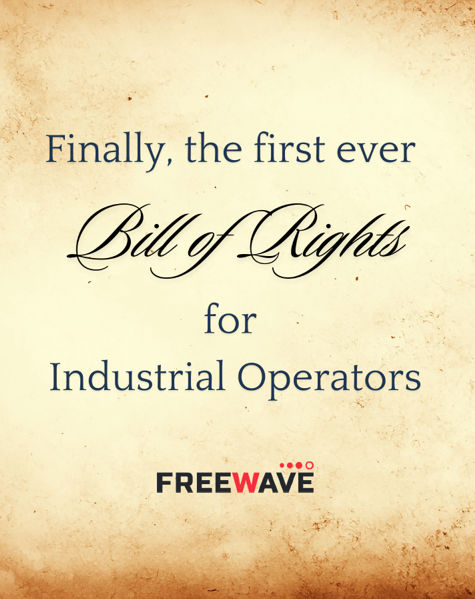
July here in the states is painted red, white, and blue. It’s a time when freedom becomes front and center. We are grateful for our young country. We remember the Founding Fathers and the sacrifices they made. We recognize, if only for a moment, our collective pride. No matter your country of origin, those who came before were brave enough to make a path toward a future with greater freedom. This got us thinking (after all, we do have “free” in our company name!). What does freedom mean when it comes to data? What does freedom mean for remote network industry leaders? Freedom means access to your data. Freedom means ownership of your data. Freedom means visualizing operations through real-time data. Data, in a sense, renders the freedom to take action, make informed decisions, and realize greater business value at scale. At FreeWave, we pledge to make IIoT data a freedom all remote industrial leaders can enjoy. Freedom gives way to growth, learning, and success. For more than 30 years, we have believed in the power of data. Data impacts decisions, business value, and, most importantly, the very future and safety of real people and our planet. Henceforth (to borrow from our Founding Fathers’ lingo), we’ve taken the liberty to create the first-ever industrial internet of things (IIoT) Bill of Rights. This is more than a list of nice-to-haves, they are must-haves for remote industrial operators of every size and industry. The IIoT Bill of Rights is our position on data governance and data democratization. It addresses global reach – that a remote industrial operator can be anywhere in the world and know what’s happening within their operations no matter how far they are spread out and what environmental conditions surround them. We believe a secure cloud environment is the right of every remote industrial leader. Zero Trust Security is not a privilege of a few, but the mainstay of many. Data should be kept safe, no questions asked. We also champion continuous connectivity. This comes by way of unlimited, high-speed, affordable satellite connectivity for all. To round our IIoT Bill of Rights, we lean into one of our four core values: Be a simplifier. This means that IIoT data solutions should be easy, plug-and-play deployments. No hair-pulling. No head-scratching. No unnecessary downtime. Instead: Open box. Power on. Get Data. This means fast deployment because uptime is one of the biggest freedoms IIoT data enables. Data inspires greater uptime because you have knowledge at your fingertips to make amazing decisions that keep operations running smoothly, all while keeping people safer. Another IIoT Bill of Rights amendment calls for cross-translation of protocols so that remote industrial companies can transform existing SCADA networks into data racetracks that carry more data, faster. Cross-translation allows different edge or SCADA protocols on the edge, SCADA, and even devices that speak different protocols to communicate. This is how industrial leaders can unleash the full power of an IIoT network infrastructure. The last amendment is AI readiness – because those who own their data will win the AI race. To see FreeWave’s full IIoT Bill of Rights, read our position paper. Working with our expert technical staff at FreeWave and experienced channel partners to solve your biggest wireless and edge computing challenges, you leverage the full solution for IoT connectivity that includes the FreeWave Insights™ data platform-as-a-service, satellite service connectivity (we’re a Connectivity Wholesale Partner in Viasat’s ELEVATE program), our portfolio of rugged connected devices, and satellite-connected devices (we’re a Global Authorized Reseller of ORBCOMM). If you’re passionate about bringing meaningful technology solutions to remote industrial companies, join us as a channel partner. If you’re a remote operator looking to scale business value leveraging your IIoT data, contact us here. We’re making a path to a future where data serves industrial operators in measurable and positive ways. Let’s do it together.
Latin America, Oil and the Race to Retrofit
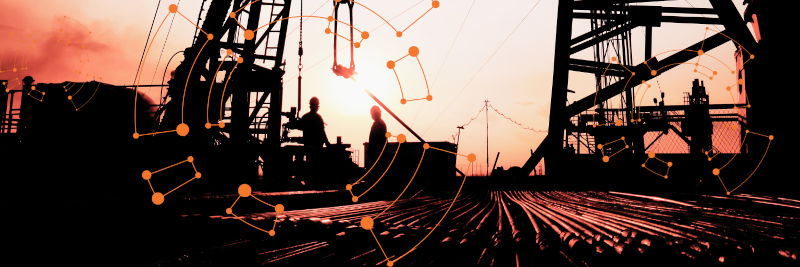
Latin America has the second-largest proven oil reserves in the world behind the Middle East, yet it’s never been known as an oil-producing maverick due to external and internal hindrances, including U.S. sanctions against Venezuela and a regulatory framework in Mexico and elsewhere that tends to dampen competition. All that is about to change. With geopolitical disruptions wracking the Middle East and Russia, importers looking to diversify their oil supply have set their sights on Latin America — and for good reason. The discovery less than a decade ago of around 11 billion barrels of crude oil reserves off the coast of Guyana made headlines globally, with news coverage reaching a fevered pitch when the oil started gushing into pipelines. The “incredibly short” five-year timespan between discovery in 2015 to full-blown production in 2020 was “unprecedented,” according to Oilprice.com. The discovery, and the oil-and-gas exploration since then, has huge implications for the global market and for Latin American oil producers. It offers a partial solution to a looming problem: a source of clean, cost-efficient oil, which will be in high demand during the decades-long energy evolution. To stay competitive and claim its stake as part of the solution, Latin America’s existing onshore oil fields, which historically operate well below their production potential, have shifted into high gear to optimize performance, increase operational efficiencies, and reduce greenhouse gas emissions. There is a challenge, however, faced by many existing producers: aging infrastructure. Data Within Reach Aging infrastructure located in harsh, remote environments like the Maracaibo Basin in Venezuela, which is surrounded by mountain ranges and an almost constant veil of overhanging clouds, or the Sureste Basin in Mexico where more than 50% of the basin area is located in a deep-water Campeche slope, are not be built for data at scale. The challenge of outdated infrastructure lies in leveraging data from the increasing number of sensors at the edge for data collection, storage, analysis, and connectivity across the enterprise. IIoT devices have long been MacGyvered with twine and duct tape. They use different protocols within decades-old SCADA systems. These disparate systems hurt production potential with two significant barriers: equipment from a variety of vendors along with little or no historical documentation to reveal who or what the modifications were and machine languages that don’t talk “nicely” to one another. While we don’t have statistics showing the number of aging pipeline networks in Latin America, there is evidence that outdated equipment reduces oil and gas opportunities. In early 2024, the U.S. Energy Information Administration looked at Venezuela’s energy landscape and found that “much of Venezuela’s crude oil production capacity and infrastructure have suffered from a decade-long lack of capital and regular maintenance.” Yet, replacing a network from scratch is costly – and unnecessary. Retrofitting existing infrastructure makes sense, leads to increasing business value from your operations, and funnels data to key decision-makers throughout the business (yes, even beyond the operations team – more on that in a bit). To support our worldwide network operator customers, we often team up with in-region trusted distribution and system integrator partners. This helps our customers experience the FreeWave difference – an end-to-end Industrial Internet of Things (IIoT) data solution – with local expertise and ongoing support. One project we’re working on is based in Peru. The infrastructure is more than 15 years old. Over the years, personnel have changed and there has been no consistent tracking of data and processes. All this has led to knowledge gaps, with questions like: What equipment do we have in the field? Where can we increase efficiency? What data do we have that we don’t access? How can data help us reduce costly downtime? What data do decision-makers in different parts of our business need? How can satellite connectivity improve uptime and data access? In established oil fields, a rise in IIoT sensors measuring things like temperature, pressure, and flow is generating massive amounts of data. But too often, data generated at the edge remains siloed, beyond the reach of decision-makers. Or, because IIoT devices have been MacGyvered with twine and duct tape and, therefore, use different protocols within decades-old SCADA systems, standard protocols simply don’t communicate well. Retrofitting aging SCADA infrastructure means leveraging data for better data management, transfer, analysis, and visualization. The solution integrates IIoT sensors, edge computing, cloud analysis for extensive processing of data from different sources, and satellite connectivity. First, though, comes the convergence conversation. Unpacking IT/OT Convergence for Better Decision-Making FreeWave’s end-to-end solution includes the FreeWave® Insights™ data platform, connected devices like our FreeWave Fusion™ platform for edge processing and connectivity, ORBCOMM’s feature-rich satellite terminals, and satellite service plans through our partnership with Viasat. The unmistakable trend we’re seeing from our work in Latin America and other regions is is Information Technology (IT) and Operational Technology (OT) convergence. In the past, these two areas were worlds apart – and it was understandable. Each had its own agenda. They didn’t play in the sandbox together. Today, they must and can. Oil producers racing to retrofit their infrastructure are recognizing that convergence is essential. In an article by McKinsey & Company, “While the rationale for converging IT and OT originated years ago, the emergence of IIoT is driving momentum today—particularly IIoT’s need for data from a vast number of sources. Compared with a traditional IT stack, the IIoT-based industrial automation stack adds a new layer for analytics, end-user digital applications, data management, and storage.” An operation and IT alliance amps up computational power in the cloud and gives a clearer insight to more users. FreeWave is closing the IT/OT gap for oil producers in Latin America that have aging infrastructure needing to get data from sensors and machines in the field, converting that data through our platform and delivering it via a single pane of glass – a user interface that provides uninterrupted visualization of data to real people, alerts, and alarms that enable data-driven decision at the point of decision-making. While technology has evolved, OT has always been
Edge Security in an Era of Distrust
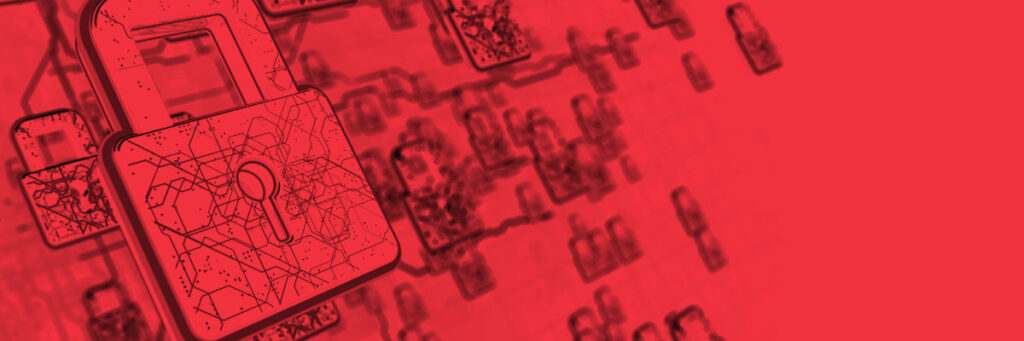
Unlike other IIoT security models that rely on a trusted perimeter, a Zero Trust Security framework provides broader coverage by distrusting every network device and user along the data path. Working in cybersecurity, the good guys are expected to think like the bad guys. Let me explain. Institutions world-wide are still guarded when it comes to cloud computing, and while the cloud generally offers greater protection against cyberattacks than on-premise data storage and processing, it is not impenetrable to hackers. Despite this leeriness, roughly 60 percent of all corporate data already exists in the cloud. And cloud migration continues to accelerate. By 2025, 85 percent of corporate IT departments will have adopted a “cloud-first” strategy, prioritizing cloud technologies over on-premises solutions. That’s why, when developing the FreeWave® Insights™ cloud-based data platform, our team assumes the “bad actor” role. To ensure the integrity and security of data in the cloud, our team is charged with finding and exposing any weak spots. We must anticipate every conceivable threat and vulnerability. We think like the enemy so we can forge armor that guards against brute attacks and sneaky infiltrations alike. Zero Trust, Cloud, and Cybersecurity And that brings me to another part of my job: helping customers see the good in the cloud (in cyberspace), sometimes convincing them that it truly does not harbor threats as ubiquitous and unconquerable as the “vicious, Lovecraftian monsters” that lurked in the low-lying cloud (of the atmospheric variety) in the horror film The Mist. I can do so with confidence because our Insights platform — in conjunction with FreeWave’s Fusion™ radios — uses a Zero Trust Security framework to keep data secure all along the data pipeline and into the cloud. We’ll delve into Zero Trust Security in a bit, right after this plot twist: concerns about cloud security are indeed legit, but in the IIoT world, the cloud represents just one part of an ever-expanding attack surface of potential entry points for cybercriminals. It’s not so much cloud adoption as the rapid expansion of IIoT ecosystems — where numerous devices are connected and continually exchange data — that poses the greater cybersecurity threat. The proliferation of IIoT devices broadens network vulnerabilities, as each device becomes a potential cyberattack vector. That’s why a cybersecurity framework must extend from the cloud all the way to the edge, encompassing every networked IIoT device. This is where Zero Trust Security comes in. Never Trust; Always Verify A Zero Trust Security framework regards all network devices and users as suspect and ignores data from any source until the sender provides verifiable proof of identity. Unlike Virtual Private Networks (VPNs) and other conventional security models that control access to a trusted perimeter, Zero Trust Security requires multiple layers of authentication and authorization as part of a continuous process. A Facilities Management Advisor article aptly illustrates the difference by likening a VPN perimeter to airport security: You show your ID at the checkpoint, and once inside, you can “roam freely and check out all the shops, terminals, and gates.” Potentially, a fake ID could provide entry to the perimeter and unimpeded access within it. But if Zero Trust were in play, “you can access only the terminal, gate, and plane you are authorized to use when you get through security.” And what does it take to pass through security? Strict access controls include various cryptographic techniques including encryption (public) and decryption (private) “keys” and digital certificates. (I Googled “How to explain public and private keys to laymen” and up popped this discussion, which paints a clearer picture than the way I tend to describe Zero Trust cryptographies: as an elaborate secret handshake known only to card-carrying club members.) Besides assuming that every network-access seeker is an impostor or a malicious actor until proven otherwise, Zero Trust Security limits access based on the principle of least privilege, meaning that devices, users, and applications are only granted the minimum level of access required to perform their tasks. In addition, Zero Trust Security divides firewall-protected network zones into smaller, isolated micro-segments — each with its own access controls and encryption — to further prevent lateral movement by evil geniuses who manage to circumvent the first line of defense. End-to-End Data Pipeline Security The FreeWave Insights data platform takes Zero Trust Security all the way to the edge. The platform allows for the secure flow of information from IIoT devices and other data sources to the cloud for analysis and then to an onscreen user interface, or dashboard, which custom-displays different data sets for different users depending on their position and permissions. FreeWave’s Zero Trust Security framework starts with our Fusion radio gateways (coming soon!) that collect and transmit data from IIoT devices in the field. An easy-to-install application is all it takes to transform Fusion radios into cybersecurity fortresses by activating Zero Trust verification and encryption. The encryption process essentially wraps data in a Zero Trust packet for secure transfer to the cloud, where another app unwraps, or decrypts, the data and delivers it to the end user. But first, the Insights platform prioritizes, analyzes, and graphically represents the data based on the user’s dashboard preferences. FreeWave customers might have hundreds of IIoT sensors — many of them unsecured — operating across several industrial sites. All of these devices are integrable with our Fusion-based data encryption software and our cloud-based Insights data platform. Notwithstanding my penchant for envisioning the worst-case scenarios, I know a good thing when I see it. And Zero Trust Security is a good thing. But don’t take my word for it. According to IBM’s most recent Cost of Data Breach Report, Zero Trust strategies reduced the average cost of a data breach by $1.76 million in 2023. And, in its Market Guide for Zero Trust Network Access, Gartner asserts that Zero Trust architecture “erects true, identity-based barriers that are proving more challenging for attackers to circumvent than traditional network-level VPNs and firewalls.” Bottom line: Zero Trust Security is the best defense against cyberspace villainy.
What is “Platform as a Service” and How Does it Improve Efficiencies in IIoT Ecosystems?
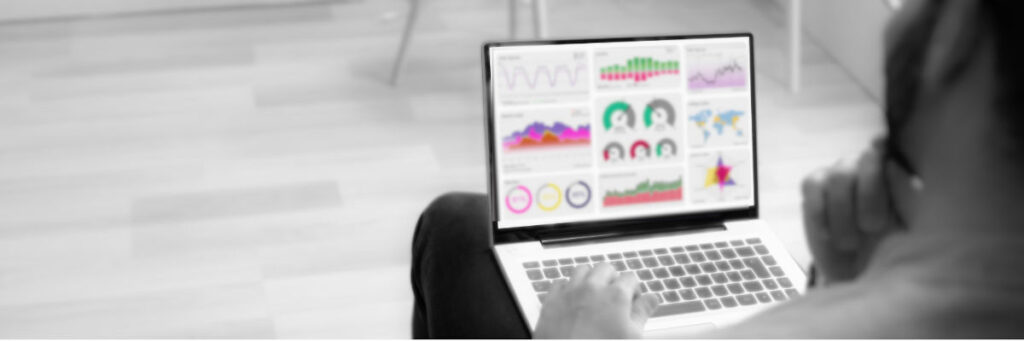
What I’m about to tell you will change a year from now — and even by the time you read this: As I write, there are about 17.08 billion connected IoT devices worldwide. That figure mushrooms daily. In fact, by 2030, the number of active IoT devices is expected to double. Put another way, according to IDC data, 152,200 IoT devices will connect every minute by 2025. Why am I mentioning these fun facts? Remote asset monitoring is the most popular use case for IoT. Yes, the MOST popular. At industrial production sites the world over, IIoT sensors (short for Industrial Internet of Things sensors, as IoT devices are referred to in such applications) continually measure pressure, temperature, water level, wind speed, air quality, ambient conditions, safety parameters — the list goes on. I’ve worked with IIoT technology in various capacities since its infancy, so it’s impossible for me to see the proliferation of IIoT sensors and not envision the enormous potential the data offers to different decision-making levels, from engineers in the field, to regional managers, to top leadership. But in recent years, as the IIoT sensors market expanded, the promise of efficiency was tempered by something else I couldn’t help but notice. Wasted effort. And lots of it. With each new IIoT device brought to market, manufacturers spent untold amounts of time and money making it live up to its potential. Time and again, they were building and rebuilding the same technology to enable data-based decision making, miles away from the device itself. Essentially, IIoT manufacturers kept reinventing the wheel. That is, until my colleagues and I saw the way to a solution. Platform as a Service Comes to the Rescue I live in Colorado, and while I’m not far from the woodsy mountains, I can honestly say I’ve spent zero time pondering the age-old question: If a tree falls in the forest, and there’s no one there to hear it, does it make a sound? And yet I ask you to consider this: If an IIoT device on an offshore oil rig (or some other remote location) senses something amiss, and there’s no one onsite, does anybody hear? For all practical purposes, the answer is no. The device itself is just a piece of hardware. It can emit a signal of sorts, but in order to be understood and acted upon by humans, the signal must not only be transferred but also translated into intelligible data. And just because a transmission is intelligible doesn’t make it meaningful. For that, the data must undergo software analysis on its way to a user interface, or point of human interaction. What starts out as zeros and ones becomes knowledge along the way. Onscreen, the user sees an interactive IIoT dashboard, which graphically represents — or “visualizes” — data so as to provide at-a-glance, actionable insights regarding remote operations. So, when a sensor detects a pressure spike or something else awry, the aberrant measurement doesn’t fall on deaf ears but takes the form of an alert, which is “heard” and heeded at the end of the data chain. At the start of the data chain — commonly called the edge — is your sensor. On the other end is the user interface. In between is a middle layer of sorts, which connects sensors to software and, ultimately, humans. This middle layer is called a platform, and every sensor needs one. The platform allows for the flow of information from end to end and also contains the tools needed for analysis. It gets the data where it needs to be, in a format that’s useful to the person receiving it. So, for every IIoT device developed, manufacturers also built out a platform. Over time, a pattern emerged: Regardless of the manufacturer or specific type of device, the resulting platforms were mostly all the same. These platforms shared so many basic functions and requirements that their makeup was roughly 70 percent identical. The remaining 30 percent of platform design varies by use case and other factors. Take, for example, a fictitious tech company called Joe’s Tree Growth Sensors (a nod to both my passions: Colorado and technology!). Several of Joe’s sensors monitor the growth of trees intended to provide shade in a public park. Elsewhere, Joe’s sensors monitor the growth of trees on a pine plantation. Sitting at his computer in the comfort of his office, the park manager wants to see his tree-growth data presented in a certain way, with emphasis on crown measurement. The sales manager of the plantation, however, needs to see alerts when the trees are ready to harvest. And across the hall from the sales manager, the plantation’s Director of Tree Health needs to see indicators that trees have a growth-stunting nutrient deficiency. Still, the thought that every device represents a specific and representative platform gave me pause. That is a lot of dashboards, proprietary links, and so on. Data overload. Clearly, it would be more cost-effective to invest resources on customizable parts unique to each application and end user while outsourcing the development of the platform’s all-purpose — or “generic” — design elements. And Joe can accomplish this feat by leveraging Platform as a Service (PaaS) as opposed to building a platform from scratch for each newly invented IIoT device. Joe’s tree-loving customers win big, too, because the platform, with its customizable dashboard, delivers data they predefine as relevant. Introducing the First Customizable Data Platform for Industrial Operators While Joe is imaginary, IIoT manufacturers and remote operators are already seeing real results with the very real and available FreeWave® Insights™ cloud-based data platform, which comes complete with user-friendly tools for dashboard creation and customization. (The words dashboard and platform are sometimes used interchangeably, but we consider the dashboard as the user interface within the IIoT platform.) The dashboard is both a control panel and a visual representation of key data your IIoT devices and sensors collect. A well-designed dashboard conveys information hierarchically through charts and other data visualizations, empowering users
IIoT Data Delivery in Oil and Gas Production: How to Cut Through the Noise and Cut Down the Costs
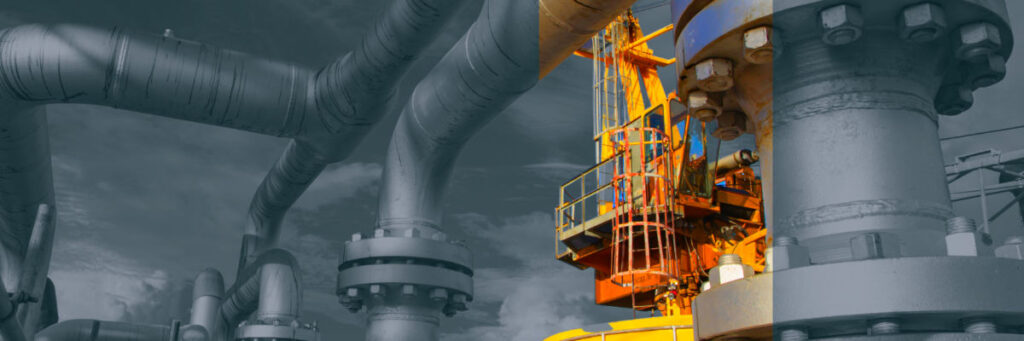
When it comes to IIoT data transmission, “talk” isn’t cheap. Here’s how to reduce data transmission costs and make sense of endless, ever-increasing chatter across IIoT devices. In the oil and gas (O&G) industry, where remote and harsh production sites abound, reliance on the Industrial Internet of Things (IIoT) is growing by the day. Sensors in the field transmit real-time data on equipment performance, environmental conditions, and safety parameters — often to a SCADA system that’s been in service long before IIoT devices became ubiquitous. Some data points mean the difference between success and failure — or even life and death. By reporting elevated pressures in pipelines, for example, IIoT sensor data helps avert disaster. By measuring the volume of oil that flows from a wellbore into pipelines, companies can collect every penny owed to them for what they extract. Because safety, profitability, and other business imperatives rely so heavily on vital measurements, this data is sometimes hailed as priceless — provided companies alchemize it into insights. Nevertheless, companies don’t want to overspend on leveraging data regardless of its potential ROI. At the same time, however, they keep adding more and more IIoT devices out in the field, raising costs as well as other concerns associated with data transmissions. What’s That Noise? One concern is the unintelligible noise created by devices using all sorts of different messaging protocols that the SCADA system can’t understand. Imagine for a moment that the United Nations has erupted into bedlam. Representatives from different nations are shouting in different languages. The poor secretary charged with taking minutes only speaks English and can’t make sense of the rapid-fire information coming at her in French, Italian, Mandarin Chinese, and a whole host of other languages. The scene is chaos. Something similar happens on a production site where IIoT devices use different protocols, or “languages,” to transmit and receive data. Existing SCADA systems can be scaled to “comprehend” more than one language, but implementing this capability for various and sundry protocols can be cost-prohibitive. Adding to the confusion, some sensors have a voltage output as opposed to a protocol output. Some communicate via an Ethernet port while others use a data or digital link. Some devices use obsolete or proprietary protocols that aren’t readily understood by SCADA systems. By and large, companies that use SCADA networks experience this as a massive problem, as though a Tower of Babel is impeding dataflow and, therefore, operational efficiency. But the solution to the problem is rather simple and comes in the form of an actual tower — a radio tower, to be exact. Translating IIoT Data for SCADA Networks Atop of this tower is a radio that serves as a communications hub, or gateway, collecting data from all the IIoT devices within its range and sending it to FreeWave Insights® Data Platform for instantaneous cloud-based translation into language the SCADA system understands. It’s a plug-and-play solution that works with any SCADA system, with limited — if any — upgrades or installations required. For example, FreeWave’s Fusion Bridge radio gateway offers these and other benefits, as well, including cost savings on cellular data. Where cellular is used for connectivity, it’s sometimes the case that each and every IIoT sensor connects to its own cellular device, which transmits the data. This is a spendy setup because each of those cellular devices, which could number in the hundreds or thousands, costs between $8 and $20 per month to keep in service whether data transmits or not. Cell phone users of a certain age can recall being billed for every outgoing text message. Later, your provider only charged you for text sent to users of a different provider. Next, you could buy data plans and send texts to whomever, so long as you didn’t exceed your plan limits — in which case you’d be charged a pretty penny for the overage. Today, consumers can buy unlimited data plans for cellular phone usage. As of yet, however, there’s no such thing as an unlimited data plan for IIoT data transmission. Data plans are available for purchase, and providers — knowing that data stream disruptions can upend business operations — have mastered the art of the upsell: persuading companies to pay for more data than they’re likely to use as a “just in case” insurance measure. The alternative is exceeding the data limit and getting stuck with a hefty surcharge. By connecting directly to the IIoT sensors and sending the combined data in fewer packets, FreeWave’s radio gateways reduce the number of cellular data transmissions, thereby reducing costs. The Business Case for Satellite Remote Monitoring for SCADA Systems So far, we’ve focused on data transmission via cellular, but many O&G operations are located in remote places where cellular service is spotty or even nonexistent. That’s where satellite connectivity comes into play, but satellite’s playing field is about to expand. In a bid to reduce telemetry costs, O&G companies have started to deploy satellite networks even in situations where cellular is a viable option. That’s because the cost of data transmission via satellite has decreased so much that it’s practically neck-and-neck with cellular. Cellular still outpaces satellite in terms of latency, but the distance is narrowing. As a Global Authorized Reseller of ORBCOMM© and a Connectivity Wholesale Partner in Viasat’s ELEVATE program, FreeWave believes that satellite is a future-proof connectivity solution for remote operations. But why not have the best of both worlds? ORBCOMM’s dual-mode terminals switch from LTE to backup satellite transmission when needed for cost-effective, fail-safe routing. You Have More Control Over Transmission Costs Than You Think When it comes to IIoT data transmission, “talk” isn’t cheap. Whether hitched to cellular or satellite, overly “chatty” sensors are another driver of data transmission costs and bandwidth consumption. You know how you can set up bank alerts to tell you when transactions occur and your balance changes? Imagine if your bank app pinged you constantly to let you know where your balance stands regardless of whether it changes.
SCADA + Satellite Equals Industry’s Latest Power Couple
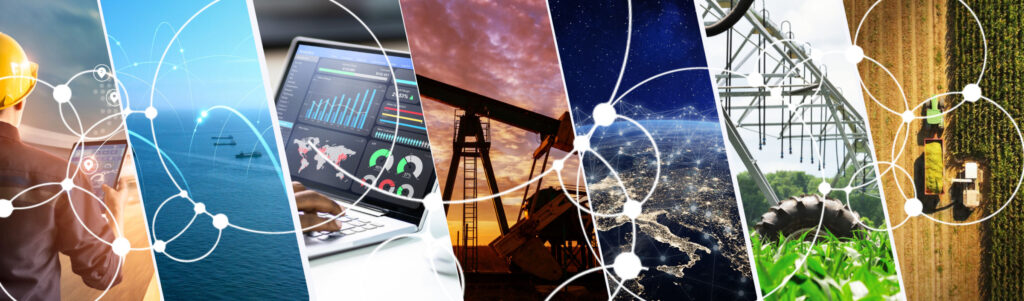
When it comes to remote industrial operations, there’s only one constant, and that is change. Change can occur in an instant — a burst pipe, an equipment malfunction, a flash flood. But, more often, change creeps up slowly and then suddenly looms large. Take, for example, the worsening labor shortage. Nowadays, if something does go wrong in the field, you might be hard-pressed to find someone to go out and fix it without leaving a gaping hole in another part of your operations. Changes give way to more changes, but they also give rise to certainties. For instance, industries with large-scale remote operations know that automating equipment and functions — and monitoring those automated systems from afar — is imperative in today’s world, where resources are short yet production demands are a tall order to fill. That’s one reason why the global industrial internet of things (IIoT) market size is projected to reach a staggering $1,683.30 trillion by 2030, up from last year’s value of $321.81 billion, according to a market analysis by Grand View Research. It’s also certain that, in some respects, the more things change, the more they stay the same. As digital transformation across various industries kicks into high gear, Supervisory Control and Data Acquisition (SCADA) — a decades-old but highly implemented technology heavily used by oil and gas, water treatment, energy and manufacturing — is adapting to meet the demands of the modern industry, proving it’s not going anywhere anytime soon. And that brings us to another certainty that still comes as a surprise to some SCADA users: Satellite connectivity has emerged as one of the fastest, most reliable, and most secure methods of transferring data from remote IIoT devices to existing SCADA systems. Today’s satellite systems are easy and inexpensive to deploy, and they make IIoT technology easier to scale. Space, it turns out, is the next new frontier for industrial leaders. During “McKinsey and the World Economic Forum 2023,” futurists predicted the space market to reach $1 trillion in the next decade with the number of satellites tripling during that time. While quick to acknowledge and adapt to changes that affect day-to-day operations and key performance indicators, SCADA users by and large have not been early adopters of satellite technology over the past decade, in part because of its historic reputation of being pricey, having high latency, and providing limited bandwidth. The world of satellite has changed. And FreeWave is stepping up to play matchmaker. We’re building an evolutionary path toward an end-to-end solution (more on that in a bit). Reliable, consistent connectivity is key. FreeWave is a Global Authorized Reseller of ORBCOMM and a Connectivity Wholesale Partner in Viasat’s ELEVATE program (Viasat, headquartered in Carlsbad, California, just completed its acquisition of London-based Inmarsat). It’s time, in the midst of the Fourth Industrial Revolution, for one of industry’s long-standing staples, SCADA, to join forces with modern industry’s rising star — satellite connectivity. Satellite Adoption’s Meteoric Rise How can companies be certain that satellite is the future-proof connectivity solution for remote operations? Follow the money. Satellite IIoT revenue is expected to surpass $130 million by 2032 in North America alone, according to Viasat. Globally, the compounded annual growth rate in that time span is estimated at 27 percent. By sector, the oil and gas (O&G) industry leads the pack, with satellite IIoT investment more than doubling over the next decade to about $115 million worldwide in 2032. Smart agriculture, transportation and mining also are pack leaders, with the utilities industry not far behind. Growth might accelerate even faster were it not for the persistence of outmoded notions about satellite communications. When they think of satellite, some corporate decision makers picture a dish as wide as an above-ground swimming pool that costs about $5,000 just to set up, plus $500 to $1,000 a month to operate. But that’s like judging a job candidate based on his 10-year-old paper résumé instead of his up-to-date LinkedIn profile. It’s true that satellite communications were relatively slow and clunky a decade ago, but satellites these days can be as small as a petri dish and cost as little as $500, with monthly service available for as low as $30. Companies with remote operations have relied mostly on cellular connectivity and other terrestrial solutions to transmit remote data to their SCADA networks. But as IIoT continues its push into underserved locations — from remote grazing pastures in Wyoming to rugged open-pit lithium mines in Western Australia — satellite offers distinct advantages. Going back to our earlier example of a burst pipe, equipment malfunction or unexpected weather crisis – that is all too common for remote industrial operators – satellite provides reliable and real-time connectivity. Here’s why this is important. In sparsely populated or harsh environments, cellular service might be limited, spotty, or altogether unavailable. In especially isolated areas, where a cell tower sighting is about as likely as a Yeti sighting (not the outdoor product goods, but the fabled ape-like creature), satellite connectivity may be the only viable solution for monitoring SCADA equipment. Where cellular coverage is available, sensor data travels wirelessly from tower to tower until it reaches the SCADA master station. Along the way, landscape features like mountains, buildings, and even clumps of trees can interfere with transmission. For this reason, satellite is a great “insurance policy” for remote connectivity that needs continuous uptime. By contrast, satellite communication does not depend on land-based transmission, so landscape features won’t block the signal. Data travels from sensors to a satellite in space and bounces back to the master station without interference except for extreme weather events that can sometimes cause a signal delay commonly called “rain fade.” FreeWave and its partners have an answer for that. With the acquisition of Inmarsat, Viasat’s fleet provides full global coverage via 19 satellites in space spanning the Ka-, S-, and L-bands. L-band signals can penetrate through rain, snow, and other inclement weather, so signal reduction is not an issue. L-band communication also offers
3 Customer Impacts for Satellite Connectivity from Viasat’s ELEVATE Partner Event
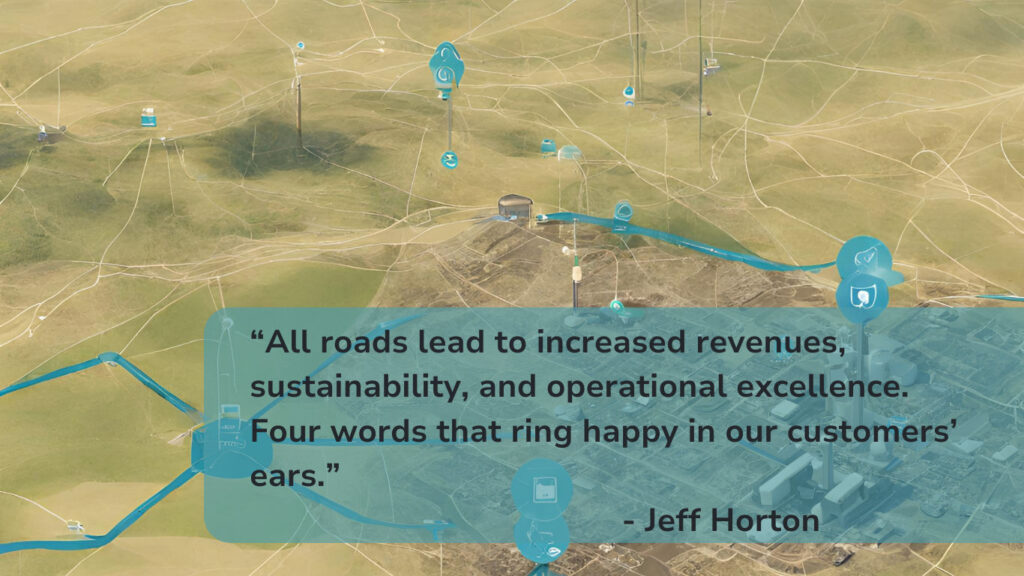
With a plate of bangers and mash in front of me and a bank of windows, I marveled at the views. We were on the 40th floor of Duck & Waffle, with a bird’s eye view of Buckingham Palace, the Tower of London, London Bridge, and Wembley Stadium. We were at the epicenter of everything British. I visited none of these places. Instead, I experienced something even better: a front row seat into the dramatic impact satellite connectivity is defining success for industrial companies. The Viasat ELEVATE Partner Event was the first of its kind. Tech innovators from around the world gathered to learn and share stories about how satellite is transforming communications for remote operators in oil and gas, agriculture, mining, logistics, and more. Viasat’s ELERA coverage map Beyond the event, ELEVATE is also a partner program to ramp up the IoT ecosystem through education, collaboration, and idea-sharing for IoT solution providers like FreeWave, system integrators, machinery manufacturers, and OEMs. Viasat is a global company of more than 8,000, a rising Fortune 1000 enterprise, which acquired UK-based Inmarsat in early 2023. Viasat covers 99% of the U.S. with Inmarsat’s ELERA satellite network providing satellite access to many parts of the world using the reliable and weather-resistant L-band network. Together, they are driving new terminal development, lowering the cost of satellite connectivity, and speeding up real-time, two-way information for remote operators who previously felt satellite communication was cumbersome, expensive, and slow. And it was. But that’s the old story. That’s why I’m excited to share three themes that emerged for me during our visit across the pond. 1. Radical innovation is driving IoT adoption in new markets and lowering the cost threshold. Here’s a non-scientific way of summing up the first theme: there’s a whole lot of R&D going on in the world! Viasat has 19 satellites in orbit with 11 on order. Impressive. They are investing in teleports for the L-band network, undeniably the best spectrum for data transfer over satellite. Translation for the rest of us? Mobile satellite communication became 20x faster in Q1 of this year. Using the same terminals with new software, this means you can send data more efficiently and more affordably. Spectral efficiency will exponentially increase the functionality of IoT devices for many solutions. Technology, and specifically data, only has meaning when people use it to better their lives. Earlier this year, as part of our 30th Anniversary vision for the future, FreeWave recommitted to not only building great tech, but to understand our customers’ day-to-day needs, tech stack outlook, revenue goals, challenges, and business vision. We talked to hundreds of customers, beta testers, and potential customers. At the top of their list: zero trust security, compliance monitoring, a leaner tech stack, real-time connectivity, remarkably better operational performance, and cost effectiveness. This is why we went to ELEVATE: to keep delivering on that wish list. And while we may have missed the sights of London, we saw our collaboration with other partners as being like a pit crew for remote industrial companies in hard-to-reach places. One company, for example, has reduced video compression by 80%. This is a game-changer for a rancher with thousands of acres because while sensors might show how much water is in a tank, ranchers are spending 100K a year to see their cattle. With video compression integrated into FreeWave solutions, they can save time and money on truck rolls. Many applications, from homeland security to smart oilfields to refrigerated cargo on a ship, can benefit from this. With the progression of satellite reliability, we’re excited to be able to bring solutions that include data-intensive video streaming requiring IP cameras. We’re designing solutions for a customer installing electric fences around government and private campuses. New IoT tech tied to satellite defies the myth that we can’t be everywhere all the time. Turns out we can. 2. Channel partners are not afraid to build things, together. The ROI of mobile satellite communication is really impressive when you are able to enhance production, throughput, and safety. Fearlessly building things together, for the betterment of our collective customers, is definitely a second theme we took away from the event. Companies we align with have deep roots in specific technologies: push-to-talk, remote employee safety, cameras, backhauling unmanned vehicles for government, just to name a few. Bringing complementary pieces into our portfolio solves customers’ bigger problems. Attending ELEVATE signaled the dawn of a new age where technology is amplified by software, satellite terminals, and collaboration of many great minds thinking together. In the end, we are made better together as channel partners, leveraging strengths, knowledge, and abilities. It makes us better, faster, stronger. It makes us better for our customers. That’s our goal as an innovator. 3. Satellite aligns with a more sustainable future. While Sputnik, the first satellite, was launched in 1957, I feel like the Space Age is just beginning here on earth. It is a key part of a more sustainable future. In an article in SpaceRef, Inmarsat’s President Mike Carter put it this way: “The ELEVATE community will play an active role in addressing the planet’s really big challenges, helping build a more sustainable, efficient, and safe global supply chain.” After experiencing ELEVATE, I’m a believer. Here’s why. If you can get real-time data remotely, you’re not burning fossil fuels to gather insight. If there is machine-to-machine “dialogue,” you streamline people’s time. If you let the ground reveal what a sprayer needs to know, you might use water more efficiently. The role of satellite communication helps solve today’s critical issues. Increasing yield and output without increasing the percentage of cost keeps consumer goods affordable. Making lives and work better is what IoT is about. It’s what FreeWave is about. Helping make lives better has been a core belief of ours for decades. FreeWave’s Platform-as-a-Service Brings Remote Operators Closer to the Truth We’re not alone. For me, that was the big takeaway from Viasat’s ELEVATE. We have access to many different ELEVATE partners and their technology superpowers. These will help us bring to market
Shedding New Light on Industrial Solar Power System Performance
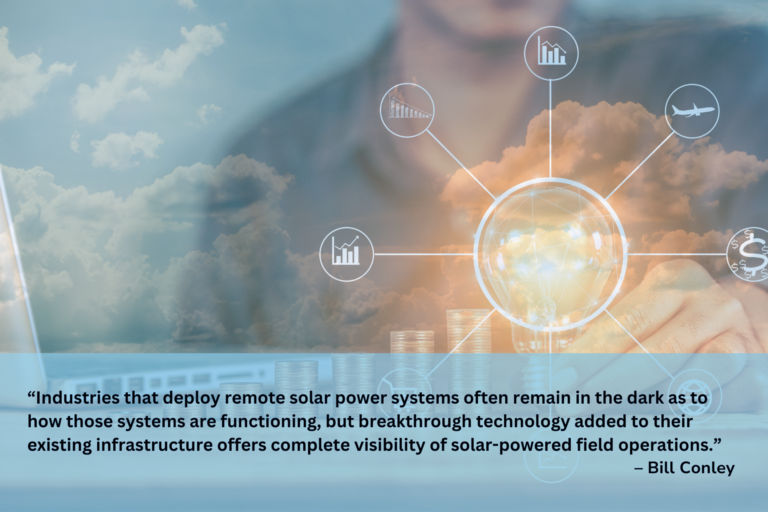
It’s not easy to write about solar energy without getting carried away with metaphors. In a world facing a worsening climate crisis, solar power — as a renewable energy source — represents a ray of hope, a bright spot, a beacon of light. Solar power’s day in the sun has been a long time coming. Before he died in 1931, inventor Thomas Edison reportedly told friends, “We are like tenant farmers, chopping down the fence around our house for fuel, when we should be using nature’s inexhaustible sources of energy — sun, wind, and tide. … I’d put my money on the sun and solar energy. What a source of power!” Today, many diverse industries are putting their money on solar power. But, in many cases, it’s not a sense of urgency about “going green” that drives them. In industries operating in farflung, remote locations, the use of solar power is usually driven by pure necessity — there’s simply no other viable power source. While there’s excitement around the promise of solar energy, my conversations with industry leaders often center on the problems associated with remote solar power systems, including a lack of visibility around solar-powered battery performance. Since battery failure can cause safety hazards and even halt production, operators take extreme — and expensive — measures to prevent it. Our customers’ pain points led to the development of a breakthrough, all-in-one-box solution that can be easily added to existing infrastructure to slash maintenance costs and reduce risk factors by providing critical data on remote solar power system performance. I invented this technology, but before I tell you all about my “baby,” let’s look more closely at the pain points it helps to address and the cost savings and other benefits it provides. Eliminating the Guesswork Around Solar-powered Battery Performance While solar-powered devices reliably monitor field operations as a whole, a lack of visibility around the performance of the solar-powered batteries themselves is a huge blind spot and cost driver. Oil and Gas (O&G), wastewater management, and utilities are among the major industries that rely on solar power, principally to operate remote sensors and devices that send critical information back to a centrally located SCADA system. This data tells the SCADA operator what’s going on in the field. For example, O&G personnel are alerted if equipment goes down or if various pressures and temperatures reach unsafe levels. Powering the devices that relay this information depends on reliable battery performance, which, in turn, depends on the availability of sunlight to power the batteries. Touting the pros of solar power, Elon Musk famously said the sun “shows up every day” and “just works.” In reality, the sun doesn’t always shine sufficiently to fully charge solar batteries, and, as we all know, it clocks out every night without fail. So, operators have tried to optimize battery performance by doing calculations to determine the amount of current needed to power the devices, including an estimate of autonomy time — the number of days that a battery charge will last should the solar panels stop absorbing sunlight. While these calculations initially suggest which sizes and configurations of solar panel and battery systems are needed to produce the required current, they don’t take into account equipment deterioration over time or the power requirements of any equipment added down the line. Hours of autonomy, so painstakingly calculated in what amounts to a paper exercise, are also affected by extreme ambient temperatures and other conditions. To avoid power disruptions and production downtime, O&G producers have taken to replacing all of the batteries every six months, regardless of need or individual battery performance. It’s not uncommon for a major producer to have several thousand remote, solar-powered sites, so battery storage and replacement are substantial budget items. One major producer mentioned they spend $1.4 million annually — just on batteries. Callouts and lockups are also expensive — and less predictable. A callout occurs when a system goes offline and stops sending SCADA communications, triggering a truck roll to the site to determine the cause. Equipment lockups require technicians to drive to the site to power-cycle the affected assets no matter where that site is, all for a process that takes 20 seconds to perform, sandwiched between hours of drive time. Considering that each and every truck roll costs as much as $2,400, eliminating set-schedule battery replacements, manual power cycling, and most service calls could easily save millions of dollars. So, let’s talk about the solution. Introducing Solar Site Analytics Having collaborated with customers to understand the problems and limitations they were experiencing with solar-powered operations, we developed a patent-pending solution that provides complete visibility of solar-powered field operations, along with other essential features. Contained in one compact box, the product packs smart monitoring and analytics capabilities that prevent production losses, reduce labor costs, improve worker safety, and predict power system degradation or failure, including: Accurate hours-of-autonomy calculations in real time Real-time updates on battery and solar panel sizing requirements for maximum efficiency Battery capacity levels, which indicate when a battery actually needs to be replaced Automatic power cycling in the event of a lockup Analytics that detect anomalies and predict maintenance needs before solar power system components go down Automatic load shedding and load prioritization to protect batteries from excess voltage As an added feature, it also includes a maximum power point tracking (MPPT) charge controller — the most efficient controller for industrial solar power system applications The product can connect to a customer’s existing SCADA system or connect directly to the FreeWave cloud-based data analytics platform. With it, operators can monitor temperatures, pressures, and other metrics, along with battery and solar panel status and performance — from capacity levels and days of autonomy to predictive maintenance forecasts. FreeWave’s patent-pending remote solar power system manager has been in development for years and, in nearly a decade of field testing, not one instance of critical failure to monitored system components has been reported. And, the monitor offers a swift return on investment, paying for