Technology Simplified: Leveraging Data in the New Digital Era
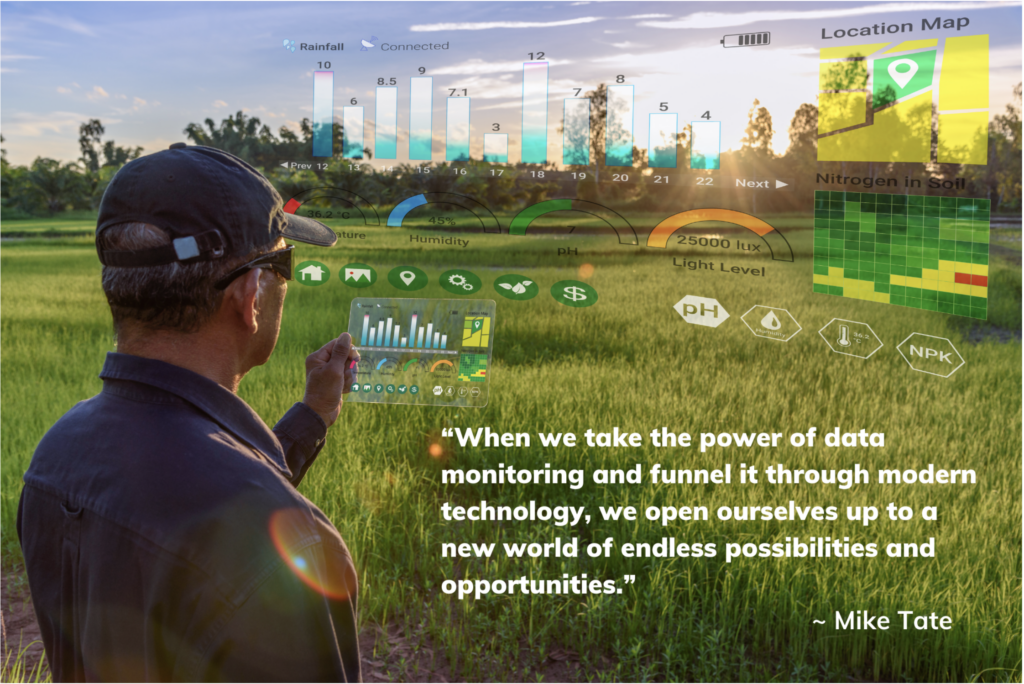
Excited by tomorrow, we face a new world filled with endless possibilities each day. Thanks to modern technology, simple sensors open the doors to our favorite restaurant, edge computing allows manufacturers to spot and correct production glitches before they happen, and high-tech traffic cameras analyze and record thousands of license plates daily to spot stolen and unregistered vehicles while also identifying suspected criminals. It’s no secret that the world is evolving before our eyes, and through the technological advancements of this digital era, we are creating a more efficient world. The power of data Data is a powerful tool of knowledge, and lucky for us, it’s everywhere! Every one of our actions is driven by a manual process of data – like the simple act of putting on a jacket when it gets cold, or an automated process of data – like a valve instinctively shutting off when a water tank gets full. Today we have the technology to effectively process, analyze and distribute data metrics in tremendously impactful ways. What does greater simplification look like for industrial leaders? Remote operations simplified When leveraged effectively, industrial internet of things (IIoT) solutions take remote operations to the next level, simplifying the work process for teams and industries across the globe. Think about some of the most popular high-value remote assets today, like drones, video surveillance, or even center pivot irrigation systems – these entities perform so well because they do what humans can’t. In mere seconds, IIoT technology can process, distribute and respond to data that would otherwise take an entire team hours, days or even weeks to achieve. In the not so distant past, industrial operations relied solely on data consumption (i.e., how much water is in the tank; what temperature is the water), but today, advancements give us the ability to respond nearly instantaneously to that collected data with actionable execution. Today we can view and control the management of an entire operation remotely on our cell phone. We can see how much water is in a tank or what temperature that water is at and automatically change and adjust the water levels and temperatures from near or far. As a result, the amount of time, resources and energy needed to run businesses has transformed entirely, and this evolution allows us to create an enhanced world and standard of work. Simple deployment Remote operations are oftentimes in rugged terrain, making them difficult or even impossible to access. At FreeWave, we solve this complex issue by providing pre-configured ready-to-deploy solutions, complete with everything needed to achieve the mission at hand. For example, through FreeWaves’s joint venture with ModuSense, we’re simplifying connectivity to cloud with a variety of pre-configured and ready to deploy monitoring and sensing solutions by supplying the entire solution with a 12-month data plan, dashboard, 12W rapid recharge solar panel, satellite connectivity and Bluetooth connectivity. You can use your mobile phone to validate the data directly from the gateway without having to wait for satellite transmission. We all know the “gotchas” when it comes to buying technology. Simple deployment means you’re ready from day one, without needing to buy additional components. Real-world impact As Chief Operating Officer and SVP of Global Sales and Marketing at FreeWave, I get a front-row seat to the real-life impact modern-day technology is having on lives, businesses and entire industries. The essentials of life have become simplified, and in the process, more people and businesses receive greater access to the things that matter most like critical information, metrics and potential outcomes. Creating a more sustainable world and preserving natural resources like food, air, energy and water have been at the forefront of IIoT since FreeWave began almost three decades ago when we brought long range, low power consumption, C1D2, 900 MHz connectivity and radio technology products to our customers. Since then, our connectivity options have greatly expanded by adding EDGE Compute, Software, Industry Protocol Conversions, Data Broker & Cloud, a complete end to end solution and with it comes the responsibility for greater environmental stewardship. We’ve all seen the devastating impact an environmental catastrophe, like the 2010 Deepwater Horizon oil spill, can have on the globe. Simple mistakes can and do cause enormous repercussions that affect us all. The truth is, with human interaction there will always be the cost of time and possible room for error. Technology, however, is different, as it allows us to not rely solely on human capacity and depend more on interconnected and advanced systems. Now, we don’t have to wait for someone to run into a situation or crisis and manually pull a lever or travel to turn off a valve. Instead, preprogrammed automation or a simple click of a button or flip of a switch from virtually anywhere in the world can control your high value remote assets. FreeWave is a technological pioneer in the 21st century. We have connected the unconnected with a reliable ecosystem of edge intelligent radios and solutions to optimize the extreme edge of remote industrial operations. Through our single IIoT platform, we provide expanded capabilities for data capture, analysis, control and automation. Our single pane of glass approach provides a simple, single vendor, one-stop-shop solution for remote operations worldwide. At the end of the day, when we take the power of data monitoring and funnel it through modern technology, we open ourselves up to a new world of endless possibilities and opportunities. It’s one thing to have data; it’s an entirely different thing to know how to leverage that data. At FreeWave, we are constantly pushing the boundaries of data monitoring and modern technology through our IIoT solutions and creating a better, safer and faster world of work for industries around the globe.
Data Connects Life: A Deeper Look at the Power of Connection for IoT Champions
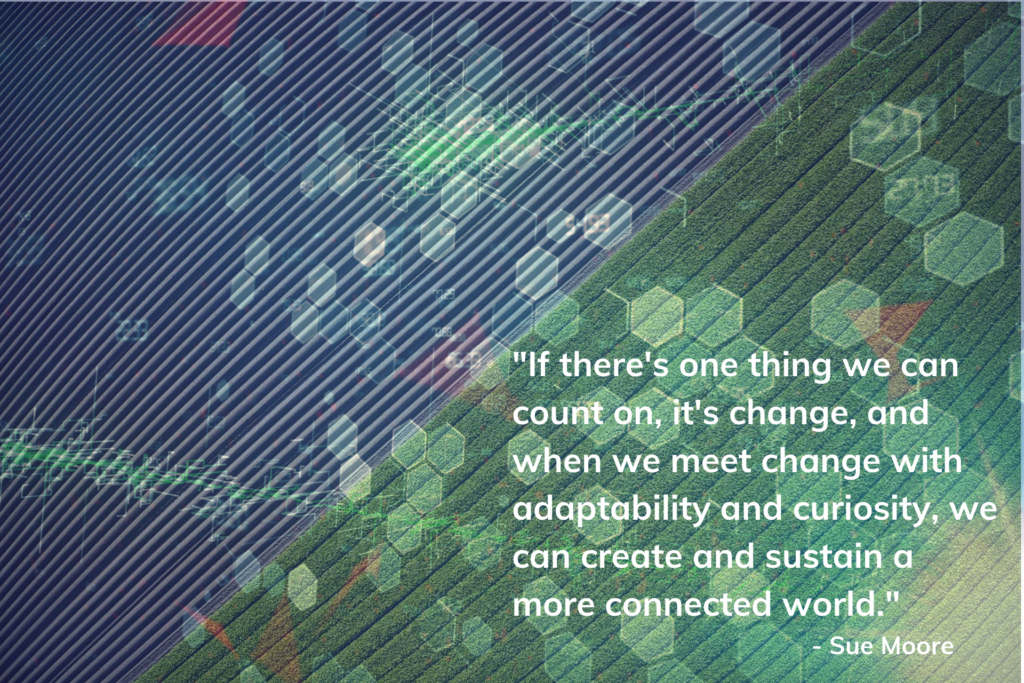
Every day, the world shifts in a new digital direction, making our lives simpler and equally more complicated all at the same time. I can vividly remember the introduction of email. I had just started my career in tech, and I kid you not, my coworkers and I questioned the efficiency of this new digital communication system. Back then, taking the time to craft an email, when I could easily make a phone call or walk to the office next door, felt foreign and unproductive, but now, decades later, I can’t imagine my life or work without the power and ease of email communication. If there’s one thing we can count on, it’s change, and when we meet change with adaptability and curiosity, we can create and sustain a more connected world, one where technology invites us to innovate, collaborate and engage with each other and the environments we live in! More technology. More data. The Mckinsey Global Survey has found that our global response to the pandemic has accelerated the rate of technology by several years. What does that mean for real people? Over time, we have discovered a new world filled to the brim with data that both informs and transforms our day-to-day lives. From smartphones to traffic management systems, the Internet of Things (IoT ) is revolutionizing life as we know it, connecting us to more people, places and systems than ever before. Connection is a powerful tool, and when harnessed effectively, it can change the world. The interdependent relationship between our natural and digital world is quite profound; in today’s society, we operate as one. In smart agriculture, for example, effective data can make a significant difference in overall crop and herd health, which, in the end, affects us all. Whether we’re on the farm, on an oil rig in the middle of the ocean or in our own backyards, technology connects us. Data is everywhere, and when this data is measured and distributed carefully, it transforms entire industries. Accessing the data you need on your terms For the last 28 years, FreeWave Technologies has pioneered a unique IoT revolution, reinventing the way industrial IoT is used in the modern market. We connect the unconnected with a reliable ecosystem of edge intelligent radios and solutions to optimize the extreme edge of remote industrial operations. Through our software, we provide IoT champions with real-time data insights to create better and more sustainable businesses. To achieve transformative operational optimization, industrial leaders need visibility into data and the ability to proactively manipulate that data and act on the insights gained from it. Our vision is to build an ecosystem of edge intelligent radios and solutions to transform the extreme edge of industrial operations into a connected part of their enterprise. Our integrated edge connectivity and computing solutions provide expanded capabilities for high-fidelity data capture, analysis, control and automation via a single industrial IoT platform that is readily scaled as each edge computing need evolves. We call it a single pane of glass. With a legacy of solving thousands of customer changes across multiple industries and deployment in 39 countries, the goal is to continue to future-proof operations so that remote work becomes more autonomous and, dare I say, simpler. It all brings us more connected with our collective purpose to create a better and more sustainable world. Data connects life. The more we see, the more we understand, and the more we understand, the more equipped we become to make better decisions. As the Director of Marketing at FreeWave, I am closely connected to the people and operations most impacted by our work. I know firsthand how powerful connection is for the IoT champions we serve, and every day I witness the power of data to transform the world. Putting it in perspective Take the water and wastewater industry, for example; in this industry, clear and controllable data insights are key to achieving effective operational management. At FreeWave, we provide these actionable data insights such as moisture levels and weather predictions through our sensor and weather monitoring technology, which ultimately allow water and wastewater industry leaders to be proactive in their business rather than reactive. A proactive and informed approach to operational management makes the difference in creating a more sustainable environment, and a more sustainable environment transforms our communities and the surrounding world. FreeWave’s productivity technology is removing barriers to data and helping industry leaders solve unique challenges like never before. Where some people may only see tech software – a little box with some wires, chips, and sensors – a much deeper reality occurs. We are all connected, and today, IoT champions get to leverage the power of this connection, along with technology and data, to create a better world, one industry at a time. I am so proud to work for a company that is connecting the world in unique and innovative ways. Every day, I see the impact of technology and what it means to be more connected through data, giving us critical insight. What we do with that data is where the magic happens. This is where we can use connectivity to push boundaries for greater innovation, make best use of our people, create safer work environments by understanding what’s happening in hard-to-reach terrain, and even take bold action to architect a more sustainable world.
NFL Advances In-Stadium Wireless Connectivity
(Image courtesy of www.sportsauthorityfieldatmilehigh.com) With the NFL season kicking off, we decided to investigate one of the more overlooked aspects of the game: in-stadium wireless communication. Surprisingly, several aspects of the game experience rely heavily on wireless communication: coaches headsets on the field and in the booth, concession stand payment processing, and, of course, fans with smartphones. Anyone who has attempted to connect to publicly available wireless internet in a stadium, concert venue or otherwise generally crowded area knows that connectivity is finicky at best and nonexistent at worst. In the era of instant score updates, fantasy leagues, Twitter and other social media applications, fans expect to be able to use their smartphones during a live-game experience. Additionally, even just a few years ago coaches themselves dealt with connectivity problems: … The tablet computer in his left hand — a high-tech replacement for the black-and-white printed pictures coaches have used for decades to review plays — kept losing its Internet connection, leaving Belichick unable to exchange images he and his coaches rely on to make in-game adjustments. The fault is apparently in a new private Wi-Fi network the NFL installed in stadiums this year to great fanfare. Internet service is erratic, making a system financed by one of the world’s richest sports leagues little better than the one at your local coffee shop. … Of course, since then, the NFL has gone out of its way to better incorporate wireless communication technology into the stadium experience for fans and personnel alike. This year, the Denver Broncos 3,000 5 GHz wireless antennas in Mile High Stadium (we should note, the claim of ‘most of any NFL venue’ is unverified): To increase fan connectivity, Broncos announce install of 3,000 5GHz wireless antennas at stadium, believed to be the most of any NFL venue. pic.twitter.com/ES2CWZhJ0z — Patrick Smyth (@psmyth12) September 5, 2017 For the NFL, and other large events, the question of connectivity has more to do with bandwidth capacity than access to a wireless network. Most cellular carriers provide access to LTE networks in the populated areas where stadiums and event centers are located, but the sheer amount of data being used during an event like the Super Bowl has grown exponentially over the years. In 2014, data usage at Super Bowl XLVIII totaled around 2.5 terabytes. Super Bowl LI, played in February 2017, saw nearly 12 TBs transferred throughout the game over WiFI alone, with Facebook and Snapchat accounting for almost 10 percent of the total bandwidth. Verizon and AT&T customers combined to use another 20 TB of data over those networks. With those numbers in mind, it makes far more sense to utilize high-bandwidth technology like WiFi, rather than relying on the LTE networks to support those big data figures. When IIoT and the NFL Collide The average consumer thinks of WiFi as a broadband service facilitated by a router in one’s home or office. When scaled to the usage size of a football stadium-worth of bandwidth consumption, however, a regular router will not suffice. Instead, these stadiums use wireless communication technology that has been deployed with regularity in the Industrial IoT for years: signal repeaters and access points peppered strategically throughout the necessary coverage areas. Just like companies in the utilities, oil and gas, precision agriculture and smart city industries, these stadiums are relying on industrial-strength WiFi platforms to handle the data demands of teams, vendors and fans. An additional consideration for stadiums and critical industries is the security of these networks, so tech vendors must be able to supply built-in security measures within the access points. These networks must be secure, flexible and reliable in order to support the massive demand being made for hours on end. The New Generation of Stadium Experiences We tend to take internet access for granted these days. Connectivity is already nearly ubiquitous and only growing each year, so it makes sense that stadiums would eventually start to catch on to the technology being used to propagate these industrial-strength networks. At this point, it is not just the NFL that is working on pushing the stadium experience into the next generation, other professional sports leagues, music venues, and festival sites are catching up to the IIoT technology that is proving to be a literal game changer.
Node-RED: The IoT Programming Language No One is Talking About
Sussing out the key pieces of the Internet of Things is usually accompanied by caveats ranging from the established uncertainty of the future, the security problems of the present, and the legacy system integrations of the past. Industry gurus and thought leaders predict growth in the billions – dollars, devices, deployments, Cloud applications, etc. Networking experts waffle on standardization. Hardware providers sprint to keep up. But one of the critical pieces of the Industrial IoT is something you won’t find jumping off front-page headlines – yet: Node-RED, the programming tool for wiring together hardware devices developed by IBM, is the power behind the IoT throne, and no one is really talking about it. Lost amid the noise about ‘smartifying’ the world is the practical reality that unless you can figure out a way to seamlessly connect the hardware devices that comprise a smart network, you are essentially relying on the Cloud to run an overwhelming number of disparate applications – and that is assuming your network is near invincible. Since the Industrial IoT relies, in theory, equally upon Cloud and Edge device processing, developing software applications that can effectively run in both settings is crucial. This is where Node-RED comes in. According to Nodered.org, the open-source Node-RED ” … provides a browser-based editor that makes it easy to wire together flows using the wide range of nodes in the palette that can be deployed to its runtime in a single-click … [making it] easy to wire together flows using the wide range of nodes in the palette.” The essence of this tool is that engineers and operating technicians can create and configure applications easily, in real time, on Edge devices. Ideally, the pieces of code being used to create programs are reusable, meaning that the process can be learned by field operators without the need for a degree in computer science. The code is built on Node.js, the JavaScript runtime that frequently pops up on Raspberry Pi platforms due to its ease of use. So, if it is so easy, and so important, why is no one talking about it? The ongoing problem for the IIoT is the Wild West mentality: the no-holds-barred land grab has resulted in disparate hardware and software products that often require a combination of proprietary and open-sourced solutions. As a result, the actual mechanisms that drive the building of an IIoT network are often less talked about than the tangible pieces that come together to build that network. There are several considerations to keep in mind. First, the idea of IT/OT convergence has only just started to gain traction, so legacy solutions (especially in certain industries) haven’t quite crossed the threshold of multi-function. Second, the changing demographic of the workforces in the industrial sector means that the traditional gatekeepers, often not versed in software or computer programming, have been loathe to adopt solutions that require a whole new skill set. The result is that the idea of programming between devices and Cloud applications is in a relative infancy. Third – and still related to the workforce demographic – creating an entire workforce of people versed in both hardware engineering and computer programming is impractical. Those factors, along with several others related to the need for network functionality and data analytics, means that a solution like Node-RED is still not completely understood, and perhaps even more pertinent, still not widely adopted by industry leaders on both the hardware and software side. But it also means that it is more necessary than ever.
Rugged Wireless Radios for International OEM Applications
For original equipment manufacturer (OEM) and military applications around the world, operational success requires reliable data delivery. This 100 percent achievable with rugged wireless radio solutions. As Industrial IoT pushes for more connectivity, coupled with the surge in commercial use of unmanned aerial systems (UAS), the pressure for around the clock command and control (C2) links is higher than ever – and it’s happening on a global scale. To support these growing needs, FreeWave has announced the general availability of the MM2-5 Watt 1.3 GHz (13X5W) integrated radio. Offered in a small package for ease of integration, the MM2-13X5W features an external 5 Watt output, making it ideal for UAS, OEM and military applications where reliability is paramount and space is at a premium. These solutions can be leveraged to deliver important data in the U.S. and abroad for a wide variety of mission critical applications. The MM2-13X5W has a lot to offer starting with it’s built in versatility and the ability to function as a gateway, endpoint, repeater or endpoint/repeater. Security is a priority – each MM2 13X5W is equipped with proprietary frequency hopping spread spectrum (FHSS) technology. It also features a line-of-sight range of up to 90 miles, and can be deployed in international settings where lifesaving communications and security are paramount. A number of these use cases include UAS applications, soldier training, environmental monitoring and other government and defense needs. Next Generation UAS Applications As the commercial drone market rapidly expands, the number of use cases is filtering into new markets. Beyond the military scope, commercial UAS applications have the potential to completely transform the monitoring, control and data analysis processes for many industries. The MM2-13X5W is equipped to support this next wave of these UAS applications, including: Pipeline monitoring as a service – drones can help maintain safe and consistent visibility of the pipeline and deliver that critical data to the network. The small form factor and proven reliability means uninterrupted data transmission in remote settings. Homeland security apps – recently, in the U.S., there have been many heated conversations around border protection. Many drone supporters believe that UAS can offer a cost effective way to monitor the nations borders. The U.S. border patrol even recently solicited contractors to build facial recognition drones. Drone delivery service – As we look at the future use of commercial UAS, drone delivery is a popular topic of conversation. We’re also seeing use cases where drones can deliver food and medicals supplies to high risk areas in third world countries. Precision Agriculture: Drones can enhance crop visibility, enabling smarter decisions and more food output. The potential impact of drones in precision agriculture is becoming recognized throughout the world. As the possibilities for commercial UAS continue to multiply, so does the need for secure C2 links for successful operations – and this is where the MM2-13X5W is an ideal solution. Additional Product Features The MM2-13x5W also features the following: 115.2 and 153.6 kbps selectable RF data rates TDMA, Super Epoch TDMA, and AES Encryption Performance tests from -40 degrees Celsius to +85 degrees Celsius Data link range up to 90 miles For more information about the MM2-13X5W, please visit: https://www.freewave.com/mm2-m13-series/
Remote Tank Level Monitoring and Automation
Industrial livestock operations have several critical needs in order to function smoothly, but perhaps most important is also the most fundamental: water. On remote sites, tank level monitoring and automation are tools that can essentially make or break the entire operation. In many of these situations, the needs of the site managers are different, so in order to maximize the technology being deployed to drive the automation process, they need to be able to customize the functionality. For operations using radio communication networks, those radios need to provide maximum programmability in order to host third party applications specific to the needs of the site managers. We recently finished a deployment that serves as an excellent case study for remote site tank monitoring deployments and included some interesting uses of radio programmability: The operator of a Rocky Mountain based livestock facility approached FreeWave to assist in remote data visualization of water tanks that are vital to its operations. The pain point was that the tank levels could only be observed visually on premise. After consideration of the terrain (mountainous, remote and big temperature swings), sensors and communications infrastructure, FreeWave engineers recommended ZumLink IPR with the Node-RED programming language for intelligent tank data visualization via browser or mobile device. The facility has minimal to zero staff most of the time. If a fault occurs such as a leak that prevents a tank from filling, the facility operators are unaware until they visually inspect the remote faulty tank, located a half mile from property headquarters. The operators wanted to reduce the number of trips to the tank facility and remotely monitor all tanks via web-based browser or mobile device. For the complete case study, visit this link: https://www.freewave.com/case-studies/remote-tank-monitoring-automation/.
Manufacturing in the Age of IIoT
Few industries can claim such a foundational impact on the United States as the manufacturing industry. Modern manufacturing began with the birth of the assembly line and the transformational effect it had on the automobile industry. Companies then adopted that approach to product manufacturing and logistics. The early phases of the next generation of manufacturing appeared as machine-to-machine (M2M) communication, a forbearer of the concept behind the Internet of Things (IoT). Eventually, IoT became so broad that specific designations were needed to differentiate between the consumer and industrial side of things, thus paving the way for the Industrial IoT (IIoT). Today, manufacturing companies, while often on the leading edge of automation technology, are still scrambling to adapt to the explosion of sensors, communication platforms, big data and high-speed analytics to maximize efficiency and future-proof their products or designs. Some companies are touting the idea of retrofitting – a concept that has existed for some time – but some plant engineers may be wary of the need for continual updating to a system that is bound to become irrelevant at some point. Still, the process can be relatively painless, and is quickly becoming necessary, as Plant Magazine notes: … Most food manufacturing and processing plants have motors powering essential equipment such as mixers, conveyors and packaging machines. But they’re just motors. They don’t play in the same league as other intelligent devices. With years of service to go, it’s difficult for plant managers to justify replacing motors that work just to make an upgrade with smart features. But motors can connect to the IIoT without a complete overhaul. Instead of investing in new, more intelligent/smart equipment, consider investing in sensors that provide similar functionality to connected devices. Smart sensors attach to almost any standard low-voltage induction motor. Sensor technology is sophisticated enough to be small, functional and energy efficient. For certain kinds of manufacturing plants, a complete overhaul may not be necessary, and a ‘simple’ retrofitting process might easily solve the first part of the problem. The second part of the problem, or challenge, is that along with smart hardware, plants also need the software and data processing capabilities to keep pace. Some plant engineers are solving these challenges by deploying programmable radios capable of hosting third-party applications so that the data can be transmitted in smaller, highly specific packets, making the transport both fast and easier to push into predictive analytics platforms. From there, software companies are building in the ability to process data in the cloud, essentially running all critical data and software operations through either a fog or cloud computing process. Cloud software services have the potential to be highly customizable based on the needs of the manufacturing plant. These technologies are good examples of the ongoing convergence between traditional information technology (IT) and operations technology (OT) needs in industrial markets. Currently, the manufacturing industry is sitting in an interesting spot: leaders in the M2M world, but still adapting to the IoT world. Where the industry ends up in the next 10 years could be a strong indicator of the economic and financial temperature of the domestic and international marketplaces.
7 Tips for OEMs to Improve SCADA Networking Communications
From remote field sensors to Supervisory Control and Data Acquisition (SCADA) and I/O modules, industrial wireless radios connect your device and sensor ecosystems with robust and reliable links. Furthermore, wireless data radio networking technology connected to I/O modules for SCADA applications have become faster, smarter and their firmware now easier to upgrade. More options and frequencies, including 2.4 GHz for short range I/O and 900MHz for long range data networking, continue to improve SCADA-based network communications for robotics, industrial automation, unmanned systems and heavy machinery. So what do Original Equipment Manufacturers (OEMs) need to know when deciding upon which technology to use? Below are seven tips for OEMs to consider when reviewing industrial wireless communication options. 1) Assess Technology Options for the SCADA Network Start first by identifying your needs, goals, and limitations. When it’s time to research technology options, observe what’s available today and what’s going to be available in the future, heeding the “buyer beware” saying. Communication products vary in many ways, and each manufacturer and/or technology has advantages and disadvantages. No single product—and likely not a single manufacturer—can meet all application needs. 2) Reduce Costs While some companies seek to continue to preserve existing investments of wired and wireless technologies, wireless options have clear advantages for SCADA systems. Most obviously, wireless installations reduce labor and material costs by avoiding hard-wiring remote assets. Speed of deployment adds savings. Wired systems can take days or weeks to be properly installed. Wireless networks generally require only the end points to be installed, saving substantial time and costs. Networks need to scale gracefully as the number of end points increases. After installation savings, scalability is the biggest advantage of wireless over hard-wiring, including slow integration into wired systems as it’s implemented. 3) Consider Hybrid Benefits Toss out any old perceptions. If you need mobile SCADA network access, find somebody that offers it. If you have a microwave tower place, use it. Piggyback slower licensed radio networks with faster 902-928 MHz frequency hopping, AES encrypted networks. Know that you can install I/O capable radios (analog and digital signal, 4 to 20 and 1 to 5) to relay contact closures or other data without adding a new Progammable Logic Controllder (PLC) or Remote Terminal Unit (RTU). 4) Maximize SCADA System Value With telemetry technologies, such as spread spectrum radios, the same radio used in RTUs can act as a slave device sending data back to the SCADA host, and as a repeater to other field devices or other RTUs. This allows almost limitless network expansion by using remote sites as a series of repeaters, and by using radios in the RTUs to poll the instrumentation. Polling the instrumentation creates a second network reporting wirelessly back to the RTU. This shorthaul network is the equivalent of a local area network (LAN). 5) Don’t Use a Proprietary SCADA System By using a non-proprietary SCADA system, users gain real-time access, control, and monitoring of their network (including all the devices and functions of their network). They can manage requirements of an ever-growing system allowing them to manage their network in real-time with fewer bodies and hours invested. Security and safety improves with better monitoring. For instance, some industrial systems don’t contain a process for monitoring the cathodic integrity for corrosion (like in water/wastewater and oil and gas) to avoid disaster. But with deployment of a wireless system, they can. They can begin by monitoring simple things, such as pump stations at wells, using I/O radios communicating back to the central SCADA system to get up-to-date information on the tanks’ or pipelines’ status. End users can more quickly resolve an emergency wirelessly, instead of manually. 6) Seek SCADA System Flexibility Advanced flexibility of radio communications offers benefits to new SCADA system deployments and upgrades performance of existing SCADA systems. For example, in water/wastewater industrial applications, there need to be generation/distribution, lift stations, system monitoring, and treatment facility systems in place (or planned) to meet the expanding growth of a community’s population and/or service areas to meet future requirements. Each year, many industries deploy more frequency hopping spread spectrum (FHSS) SCADA solutions to help monitor and manage critical infrastructure. Several manufacturers (including FreeWave Technologies) offer FHSS radios capable of retrieving data from remote locations. And although wireless IO (input/output) has been available, only recently have both capabilities been offered in one communication solution. 7) Seek Easy-to-Use SCADA Software OEMs implementing and using a SCADA network systems for data communications want a simplified, rapid setup and easy management of a network. That includes ability to manage multiple frequencies and multiple networks within one system. A centralized storage and management center provides easy access to system configuration and diagnostics data. Technicians in remote or harsh weather environments need robust reporting capabilities. Software like FreeWave’s ToolSuite can manage data communication diagnostics and configuration.
Connected Oil Fields in Peru
China National Petroleum Corporation (CNPC) is one of the largest energy companies in the world with operations in 28 countries. In May 2017, CNPC announced it would invest $2 billion in an oil and natural gas block in the southern part of Peru. Beyond the recent investment, CNPC has had a presence in Peru for more than 20 years, including oil fields in the northern portion of the country. To optimize operations in 2009, CNPC ran a pilot test in Piura, Peru to find the ideal communication solution for monitoring, collecting and transporting data. Piura is a coastal city located near the equator where the average temperatures hover around 95 degrees Fahrenheight. To connect the oil fields into the Supervisory Control and Data Acquisition (SCADA) system, CNPC needed a communication technology built to withstand harsh weather, such as high temperatures, large amounts of rain, wind and a variety of other environmental factors. The goal of the pilot was to have several test sites reporting to a gateway and then into a SCADA system to monitor several pumping devices and equipment including: Pump of Controller (POC), Pump Cavity Progressive (PCP), Balance Oil Recovery System (BORS) and plunger lift. FHSS for Oil and Gas In the Piura test case, the distances between links weren’t long, but depressions, canyons and steams made line-of-site (LOS) a challenge. CNPC, who tested multiple Machine-to-Machine (M2M) communication solutions in Piura, found that FreeWave’s Frequency Hopping Spread Spectrum (FHSS) technology solutions offered the most reliable connectivity in comparison to other solutions used during the test. FreeWave solutions also use repeaters that helped establish and maintain connectivity despite the lack of LOS. Additionally, the links were established easily and fast in comparison to other solutions that were a part of the test. During the entire three-month pilot, the FHSS-based M2M solutions did not lose communication or the ability to send data to the SCADA system. Industrially hardened, ruggedized FHSS technology has proven to be reliable in in many oil and gas installations around the world. As the Industrial IoT (IIoT) drives connectivity, we continue to see the demand for reliable communication links in environments like Piura that can have challenging conditions. FHSS technology offers not only a reliable, easy to install communication link, but it easily integrates into today’s modern IIoT networks. To get the full story about the test sites in Piura, read the case study: https://www.freewave.com/case-studies/china-national-petroleum-company/
Industry 4.0 Top News Roundup
Industry 4.0, another term being batted around for the Industrial Internet of Things (IIoT) to explain the next-generation of industrial manufacturing and a new data exchange paradigm, is bleeding into multiple industry dialogues to describe the new landscape of how things are being made. With all the hype surrounding the idea of a “smart factory,” it seemed fitting to turn our attention towards highlighting our top news being reported on Industry 4.0. Industry 4.0: the urgency of data standardization By @Antoine_Rizk1 | Published on @ManufacturingGL “Sometimes presented as the new industrial revolution, Industry 4.0, primarily represents an advance in production means and practices. Characterized by interconnected machines and systems, it involves making production and supply chains smarter in order to improve efficiency in resource allocation and increase agility in production processes.” Industrial Analytics Based On Internet Of Things Will Revolutionize Manufacturing By @LouisColumbus | Published on @Forbes “Industrial Analytics (IA) describes the collection, analysis and usage of data generated in industrial operations and throughout the entire product lifecycle, applicable to any company that is manufacturing and selling physical products. It involves traditional methods of data capture and statistical modeling. However, most of its future value will be enabled by advancements in connectivity (IoT) and improved methods for analyzing and interpreting data (Machine Learning).” Drones will transform the way food is grown next year By @Harri8t | Published on @CNBC “Drones are transforming agriculture — giving farmers new tools to supervise crops and check on fields from the air — and 2017 will be be a pivotal year for adoption, say industry experts.” US Manufacturers Too Slow to Adopt Industry 4.0: BCG Study By IW Staff | Published on @IndustryWeek “Nearly 90% of manufacturing leaders surveyed by BCG regarded adopting Industry 4.0 technologies as a way to improve productivity, but only about one in four see opportunities to use these advances to build new revenue streams. Many are pursuing isolated initiatives scattered throughout the company, BCG found in its new report, “Sprinting to Value in Industry 4.0,” without a clear vision and coordination from the top.” Embracing ‘Industry 4.0’ By @alansmurray | Published on @FortuneMagazine “There’s a interesting new report out from BCG this morning on “Industry 4.0” – the German’s preferred term for how big data, cloud computing, sensors, advanced analytics, augmented reality and improved robotics are dramatically changing the world of manufacturing (known in GE-land as the “Industrial Internet”).” As we conclude another round of top news, we hope you were inspired and informed about the latest in Industry 4.0. It’s clear that business digitalization will only continue to add more technology, whether that be IoT, sensors, cloud computing and other solutions. Our job is to be ready and informed about how tomorrow’s technology could help enterprise digital transformation today.