VanZandt/Eagle Automation Joins FreeWave Technologies’ Partner Program to Expand IIoT Solutions to Energy and Industrial Markets
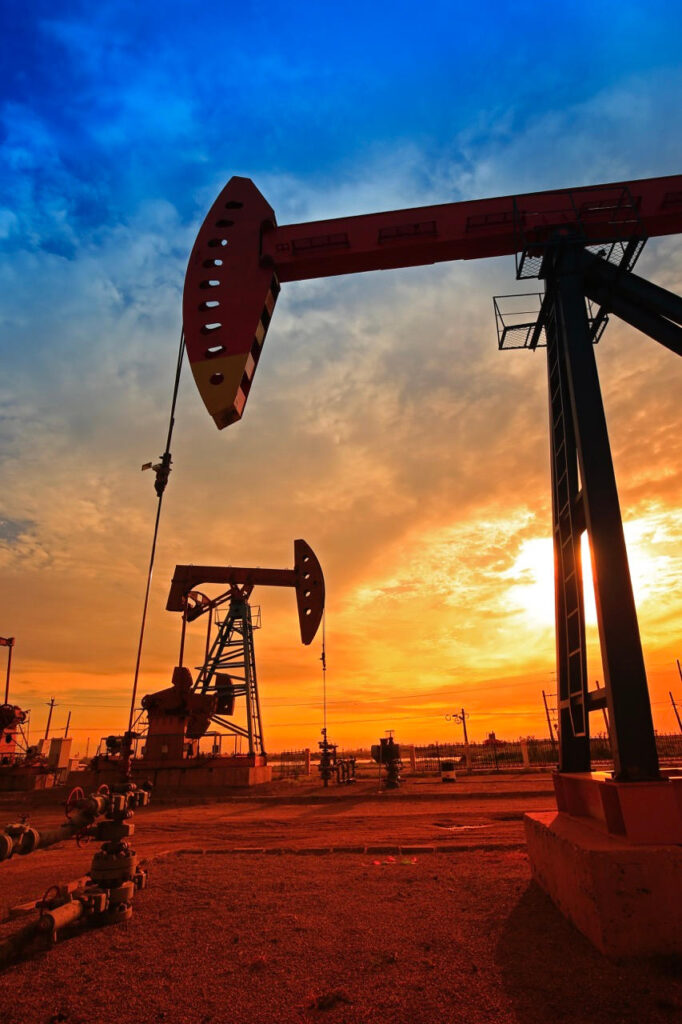
April 27, 2023 – Boulder, Colo. – FreeWave Technologies, Inc. today announced that VanZandt Controls/Eagle Automation, an industry leader in Valve Automation, Flow Measurement, Instrumentation and Controls, joined its solutions program as a value-added distributor. VanZandt/Eagle recently acquired Commercial Radio, Midland TX. Since 2003, Commercial Radio has become a trusted distributor of Industrial Communications products including wired, Wi-Fi, radio, microwave, cameras, solar, antennas and towers. This acquisition now provides VanZandt/Eagle the ability to offer FreeWave solutions in its 13 branch locations. FreeWave Technologies is widely known in the industry for its remote site connectivity, Industrial Internet of Things (IIoT), and Edge computing solutions producing robust, rugged, and reliable connectivity options for remote industrial operations. “We look forward to serving VanZandt’s expansive customer base with FreeWave solutions that bring their data closer to them no matter when they need it or where they are,” said Steve Wulchin, FreeWave CEO and Chairman. “VanZandt is a proven leader in many industrial segments where we can align to bring the best solutions for remote data.” “FreeWave and VanZandt/Eagle have a tremendous opportunity to expand the industrial data-connected solutions market.” Don Maness, CEO of VanZandt commented. “We provide customers with intelligent field devices, controllers, and SCADA solutions. The addition of Freewave allows us to offer a complete and secure IIoT solution. We are excited to collaborate with a company that shares our vision and value of providing the best solutions to the market.” About FreeWave Technologies Based in Boulder, Colo., for 30 years, FreeWave Technologies has connected the unconnected with a reliable ecosystem of edge intelligent radios and solutions – manufactured in the United States – to optimize the razor’s edge of innovations for remote industrial operations. FreeWave has a legacy of solving thousands of customer challenges globally across multiple industries and can help transform and future-proof operations. About VanZandt/Eagle Automation Headquartered in Fort Worth, Tex., VanZandt Controls/Eagle Automation has over 200 employees across 13 branch locations serving Texas, New Mexico, Colorado, Louisiana, Oklahoma, Wyoming, Utah, Montana, Kansas, and Arkansas. The company is a Lifecycle Provider of products, solutions, and services to industrial customers. Key offerings are valve automation, flow measurement, instrumentation, and controls. “Faith, Family, Integrity and Diversity” are the core values of the company. The brand promise is “First to Quote, First to Deliver, Reliable Service.” This promise is supported by top tier product manufacturers, a highly skilled sales force, inventory in every branch location, vendor managed inventory solutions, a panel shop, board repair shop, valve production, four machine shops, and a branch service team.
FreeWave Leverages ORBCOMM’S Satellite IoT Technology
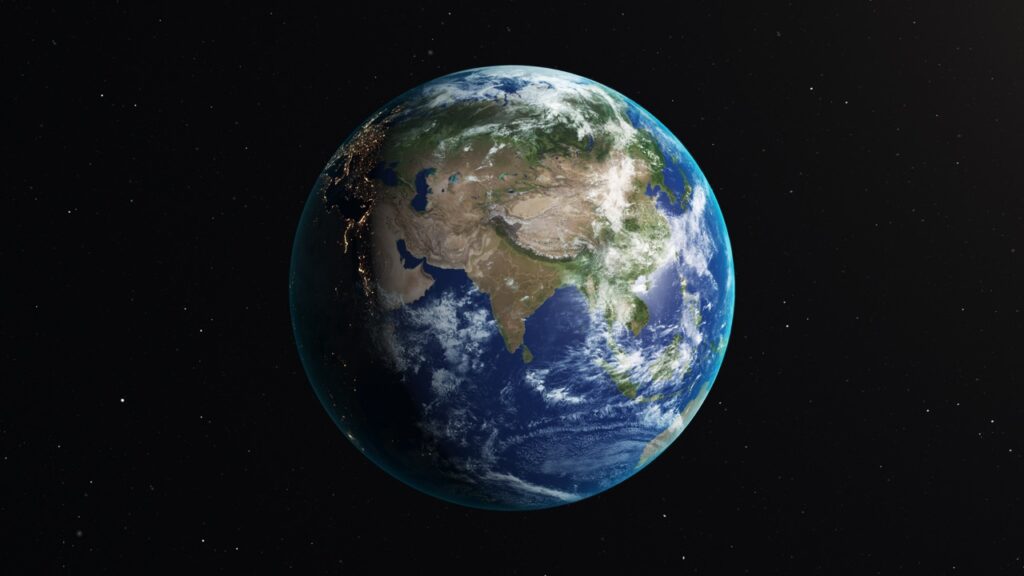
To Automate Remote Industrial Operations Drives efficiency, sustainability and compliance for FreeWave’s environmental IoT solutions Rochelle Park, NJ, March 13, 2023 – ORBCOMM Inc., a global provider of Internet of Things (IoT) solutions, today announced that FreeWave® Technologies (FreeWave), a leader in industrial wireless technology, has selected ORBCOMM’s next-generation satellite technology to expand its environmental IoT solutions portfolio, which helps customers improve the efficiency, sustainability and compliance of their remote global industrial operations. FreeWave is using ORBCOMM’s feature-rich satellite terminal, which provides enhanced two-way communication speed, global coverage and low power consumption for monitoring a wide variety of environmental IoT applications, including farming and agricultural systems, water treatment and distribution, weather prediction, and tank-level management. Leveraging ORBCOMM’s latest satellite IoT technology, FreeWave can deliver uninterrupted visibility and control for sensors, equipment and machines anytime, anywhere for maximum reliability. With access to deep data insights, alert notifications and customizable reports, FreeWave can help its customers drive greater uptime, process and compliance automation as well as real-time performance management. ORBCOMM’s technology also helps FreeWave’s customers optimize their operations to reduce the environmental impact and make more sustainable business decisions. “ORBCOMM’s best-in-class satellite technology is integral to FreeWave’s environmental IoT solutions to ensure optimal reliability, global coverage and longevity for customers spanning the agriculture, oil & gas and natural resources industries, which expands our reach in these critical markets,” said Chris MacDonald, ORBCOMM’s Senior Vice President of North America Sales. “With ORBCOMM’s two-way satellite terminals, FreeWave’s customers can seamlessly monitor and control their industrial assets from anywhere in the world, enabling precise and efficient management of their operations with an immediate ROI.” “We are excited to partner with ORBCOMM and leverage their high-performance satellite IoT technology to transform the extreme edge of our customers’ industrial operations into a connected part of their enterprise,” said Mike Tate, COO and Senior Vice President of Global Sales & Marketing with FreeWave Technologies. “By incorporating ORBCOMM’s devices into our industrial IoT applications, we can bring exponential efficiency and productivity gains to our customers and help them preserve essential natural resources such as food, air, energy and water to create a more sustainable world for generations to come.” To schedule an appointment to meet with ORBCOMM or FreeWave on-site at Satellite 2023 from March 13-16, 2023 at the Walter E. Washington Convention Center in Washington, DC, please click here for ORBCOMM and contact Jeff Horton for FreeWave. About ORBCOMM Inc. ORBCOMM is a pioneer in IoT technology, empowering customers with insight to make data-driven decisions that help them optimize their operations, maximize profitability and build a more sustainable future. With 30 years of experience and the most comprehensive solution portfolio in the industry, ORBCOMM enables the management of over a million assets worldwide for a diverse customer base spanning transportation, supply chain, heavy equipment, maritime, natural resources and government. For more information about how ORBCOMM is driving the evolution of industry through the power of data, visit www.orbcomm.com. About FreeWave Technologies Based in Boulder, Colo., for 30 years, FreeWave Technologies have connected the unconnected with a reliable ecosystem of edge intelligent radios and solutions – manufactured in the United States – to optimize the extreme edge of remote industrial operations. FreeWave has a legacy of solving thousands of customer challenges globally across multiple industries. FreeWave can help transform and future-proof an operation now. Visit www.freewave.com to get started.
FreeWave’s Steve Wulchin Returns as CEO
On January 9, 2023, Steve Wulchin returned as CEO of FreeWave Technologies. Steve served as the company’s CEO from founding — as one of its co-founders —until 2014. An experienced business leader, Wulchin will succeed Kirk Byles and assume responsibilities immediately. Mr. Byles has left the company to pursue other opportunities. As the chairman, co-founder, and former CEO of FreeWave, Steve has been intimately involved since its inception three decades ago. Steve’s vision has always been to create a great company with great products and amazing people who are driven to provide superior solutions and service to our customers. “Steve’s leadership will propel FreeWave forward into the vision set for its IoT-enabled success and next phase of growth.” said Bob Dimicco, FreeWave board member. Wulchin holds an MBA from the University of Texas and a BS in Commerce from the University of Virginia. His passion for both the wireless industry and FreeWave’s evolution as an intelligent edge solutions provider played a pivotal role in the company’s success to date. “FreeWave is uniquely positioned to take advantage of the cloud-enabled data opportunities available in the IoT space.” said Nazila Alasti, board member. “With Steve at the helm I’m excited to see what the team can do to bring that vision to fruition.”
Unlocking Creativity within the Industrial Sector
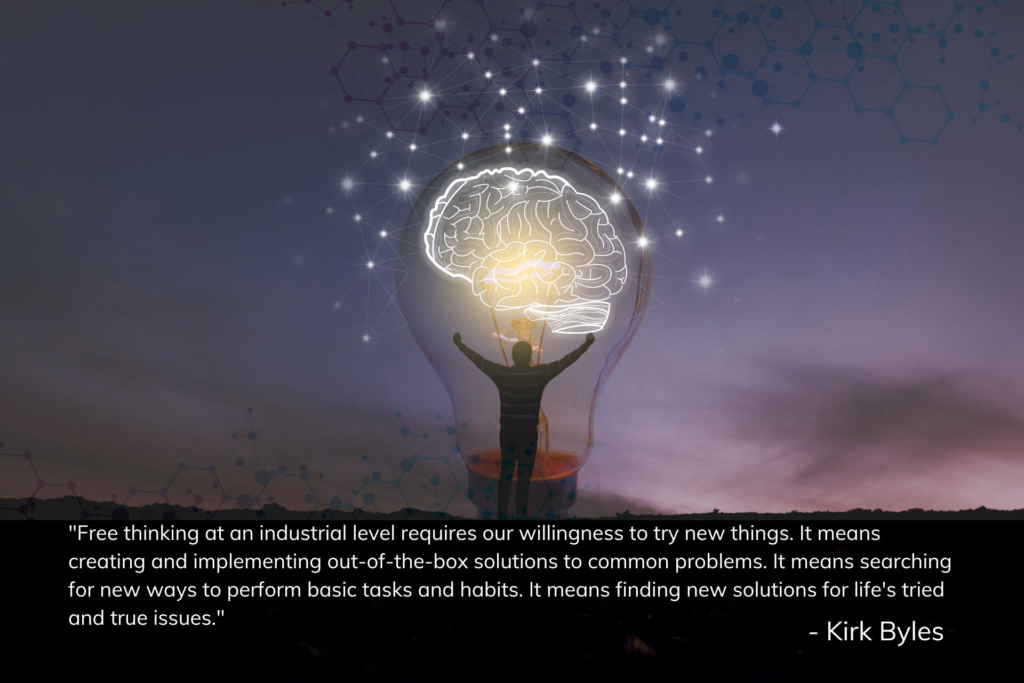
Never content My friends and coworkers can attest that I live by the basic life philosophy: “never content.” I believe in pushing boundaries and resisting the status quo, both in business and leadership. As I see it, we have two options in this life: we can sit on our laurels and wait for change or take things into our own hands and innovate. Thanks to the industrial internet of things (IIoT), our opportunities for change and transformation are endless. The more willing we are to be free thinkers — expanding the territories of our respective industries, the larger the impact we’ll witness in the world around us. The key to true transformation Most people can agree that innovation is the key to success in the industrial sector. If we keep doing things the way we’ve always done them, we won’t have much of a world left in short order. My kids are now in their twenties, and quite frankly, they’re pissed at the environment the generations before them left behind. I understand their frustration; it’s no secret that we’re facing a global environmental crisis, and without positive change, things will only get worse. If we truly want to be a part of the solution, we have to think bigger. We must become free thinkers, willing to do more than what’s been done to actually see the kind of transformation we’re looking for. Today, IIoT helps us expand our thinking. We are only on the cusp of what edge computing and data analytics can do in remote areas. Data helps us make sound decisions. When you think about where our day-to-day information is generated and how it is analyzed, you can actually imagine a world where operational managers don’t have to walk the fields, manually check pressure gauges, or physically adjust pumps to gather intel. With the right technology in place, these tasks can all be automated, which means a natural skyrocket in productivity and efficiency for remote operations worldwide. This is truly exciting because it means a shift in the culture of business, environmentalism, and sustainability. When industrial leaders and remote operations managers are given more time and space to think, they can innovate on a whole new level. Where does this lead us? Straight to the intersection of modern technology and inventiveness, where we all have the opportunity to create a safer, stronger, and more innovative world. This is great news for the modern business owner because it means the opportunity to create stronger work models and a more efficient workflow, which naturally leads to greater employee retention and better cash flow. This is truly a win for all. The big picture As a whole, technology has provided extensive upgrades within the industrial sector over the last few decades, but in reality, until IIoT came around at a large scale, just within the last few years, we didn’t have the data needed to actually know or understand what was going on. Data is great, but intelligent insight into that data is even better. Now, thanks to the ever-expanding world of technology, we can analyze data intelligently and utilize it more effectively. With this type of smart equipment on the market, field workers can do things like monitor a banana plantation from formation all the way to the supermarket. Where before, we could only know that a banana was picked and on a boat to its next destination, we now have the technology and subsequent opportunities to see things, like product quality, faster and more clearly. Free thinking at an industrial level requires our willingness to try new things. It means creating and implementing out-of-the-box solutions to common problems. It means searching for new ways to perform basic tasks and habits. It means finding new solutions for life’s tried and true issues. Sure the modern farmer may be used to turning the same lever on and off every single day, but with the right technology in place, they don’t have to. Free thinking means moving beyond the status quo to see and receive a world filled with new possibilities. Over the next few years, we’re going to see billions of dollars spent on data processing and analysis solutions. The more we know, the more we can respond to real-life situations with confidence and precision. The current financial trends and predictions are important because they reveal that our world is ready for change. Now is the time to innovate. Think bigger A crucial part of our strategy at FreeWave is implementation without dictation. This means we fully empower our customers to be free thinkers within their own environments. We want you to have full control over the information you receive and how you use it. Our job is simply to make your life easier by deploying the technology you need — edge computing capabilities, wireless connectivity, sensor technology, and more to help you manage your operation from anywhere in the world. Our IIoT solutions are designed with a simple-to-use control panel (aka our single pane of glass dashboard) so that you can run your entire operation from a singular entry point. We are no strangers to the work of free-thinking here at FreeWave (it’s part of our name as well as our culture). In our own business model, we’ve had to expand our ideas and our identity as a leader in the tech space. For many years FreeWave rode its pedigree of building and selling narrowband radios without much thought toward innovation, but then, we recognized the need our customer base faced as they searched for help in understanding what IIoT could mean for their businesses. We could’ve stayed as we were and continued to do what we did best at the time, but instead, we chose to pivot and really dig into our customers’ needs and how we could best serve them. Now, our solutions include multi-radio edge computing solutions with gateways, edge data analytics and applications, and it all started with our team’s willingness to think bigger. Free
FreeWave Technologies Welcomes Jeff Horton as Chief Revenue Officer
BOULDER, Colo. – April 25, 2022 – FreeWave Technologies, the leader in Industrial internet of things (IIoT) wireless connectivity and edge computing, today announced that it is adding a new Chief Revenue Officer, Jeff Horton. Mr. Horton is an accomplished, solutions-focused executive with a proven approach to revenue generation and will apply that experience now to support FreeWave in its innovation and growth trajectory. “Joining FreeWave at this critical juncture in its growth provides an exciting platform for me to engage decades of experience of evaluating industry trends to further revenue opportunities,” Horton stated. “The Industrial space has undergone such monumental change in its evolution and FreeWave is well-positioned to support its customers in embracing data-based decisions from the edge.” Recently, FreeWave introduced a series of solutions for remote monitoring and data analytics in its Fusion™ platform expanding the way to connect devices in even the most remote locations with its Fusion Satellite solution. This is the beginning of a new era of data-based edge computing tools available to industrial customers worldwide. “We’re eager to have Jeff join the team at such a great point in the journey. His customer-centric approach and broad market understanding will certainly add to the already strong team we have at FreeWave. I’m thrilled for things to come.” Said CEO, Kirk Byles. About FreeWave Technologies For 28 years, we’ve connected the unconnected with a reliable ecosystem of edge intelligent radios and solutions — manufactured in the U.S. — to optimize the extreme edge of remote industrial operations. We enable high-fidelity data capture, analysis, control, and automation via a scalable IIoT platform purpose built for the harshest, remote environments in the world. A joint venture with ModuSense makes global innovation agility and turn-key industrial IoT edge solutions a reality, accelerating our ability to bring fully integrated, plug and play IIoT solutions to the market quickly and cost-effectively. With deployments in 39 countries, and a legacy of solving thousands of customer challenges across multiple industries, we can help transform and future-proof your operation now. Visit freewave.com to get started.
Your Employees are Talking, But Are You Listening?
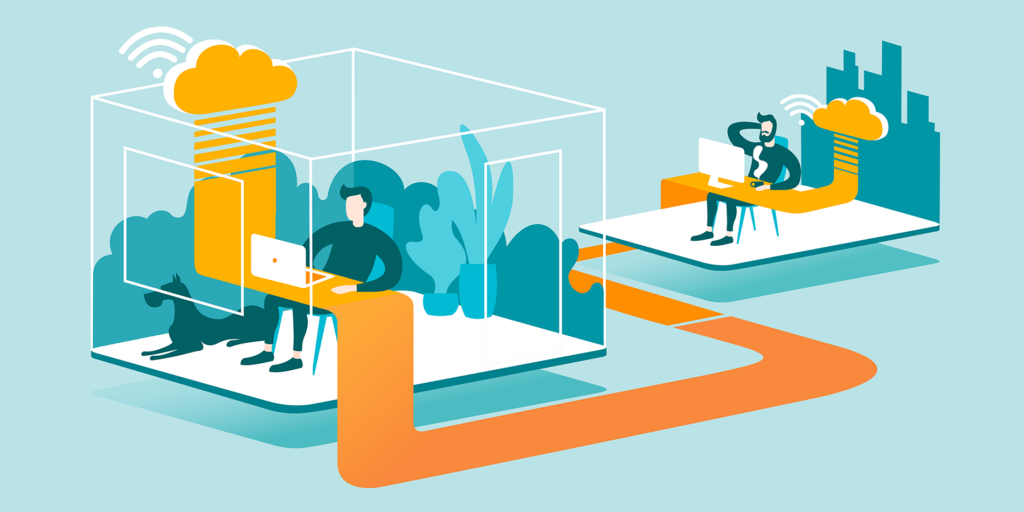
FreeWave’s Kirk Byles explains why listening to your employees is an easy way to increase engagement and productivity among remote teams. WIRED recently published an article about why we are seeing pushback from executives about working from home despite the fact that businesses have transitioned successfully to the WFH model and employees routinely express greater satisfaction with it. The article highlights the disconnect in both planning and execution between executives and staff and it basically comes down to three things: assumption, bias, and transparency. It’s not about knowing all the answers, it’s about asking the right questions. One of the most important things we’ve done at FreeWave during the pandemic when working from home wasn’t a choice, but a necessity: increase the cadence of our engagement survey to every six months and *really* listen to feedback. Like most businesses in the last two years, we had to react quickly to the changing tides of COVID. We shut down our office on March 13th of 2020 and, after consistently receiving meaningful and reliable feedback from our staff, we decided to transition to a “remote encouraged” culture. And, it’s working. The article mentions that executives have very differing views, experiences, and appreciation for in-office than most of their own staff. There are assumptions and biases about what is needed for both productivity and engagement and about the experience that most staff have versus the experience of the executive. The survey refers to it as “a focus group of one. I have X, Y, and Z resources and experience so that must be true of everyone in the company from Assembler to Customer Service and Accounting.” We approached the challenge of engagement with a simple premise: we don’t know the answer so let’s ask questions and base an iterative plan on the data. We wouldn’t start developing a product without market research so why would we do the same with employee engagement? Transparency and the Fail Fast Philosophy In the article, Brian Elliott of Future Forum cites the reticence of executives to announce an action plan if they “don’t know all the answers”. Maybe it’s because we’re a tech-based business where iteration is the norm or maybe COVID taught us lessons in adaptability but, whatever the case, we’ve always understood the fail-fast philosophy is not just for the technical side of the company. While actively addressing the issues of assumption and bias in collecting the survey data, we still had one more challenge to address and that was transparency. To that end, not only do we present ALL survey data in our quarterly All Hands; we also announce specific plans to address areas of concern. We set expectations and not only encourage employees to hold us accountable for the action items but acknowledge that these plans build upon each other. In every, all-hands gathering we summarize any changes in survey results, announce whether the previous two- quarters plans’ have seen any success, and move forward with new plans to either maintain or improve engagement results. These relatively short timelines and repeated testing allow us to move quickly to actively address not just employee needs but the needs of the business as a whole. Results As any businessperson knows all it takes for top talent to leave is a phone call from a recruiter on the right day. Businesses who have neglected to both survey their employees, publicly announce results, and work on improving engagement are seeing this in droves. I’m sure there are many other companies like FreeWave that don’t have the ability to provide many of the perks that other large tech companies rely on such as gyms on-site or free food or even salaries in the top 10%. However, on the flip side, many of those companies have doubled down on returning to the office and implemented micromanagement and monitoring tools of their staff and even old-fashioned dress codes and attendance policies. Their employees become more frustrated at losing the flexibility, trust, and better work/life balance benefits they have come to appreciate during the pandemic. If they were successful and thriving over the past 18 months, why should we consider they wouldn’t be going forward? Maybe we’re lucky, but we’ve been able to attract some really top-tier talent from larger organizations by providing, not just the flexibility employees’ demand, but the trust that allows them to flourish.
Introducing Game-Changing Connectivity for Remote Operations
FreeWave’s new Fusion Bridge dual-radio gateway delivers seamless Wi-Fi connectivity to remote 900 MHz networks BOULDER (May 3rd, 2021) – Data is everywhere, but Wi-Fi is not. If remote operations lack on-site connectivity to gather and share real-time, business critical data, efficiency suffers. Today, Boulder-based FreeWave Technologies introduced a reliable way to connect remote assets and unlock siloed operational data: Fusion Bridge. The dual-radio bridge adds WiFi access point connectivity to remote 900 MHz networks. A plug and play option for existing ZumLink Networks, it makes it easy for enterprises to connect multiple devices and sensors in the field, access real-time data, drive new operational efficiencies and improve asset management. “Fusion Bridge solves a real problem for enterprises that have remote assets generating critical data in the field and requires staff to physically monitor or collect it directly,” said FreeWave CEO Kirk Byles. “Manual data collection is time-consuming, can introduce human error and is highly inefficient. But it also delays decision making, which not only adds costs, but also minimizes the ability for companies to proactively mitigate business risk. Fusion Bridge is another example of how we are working to help customers address real problems and add capability to existing network communications without substantial investments.” Fusion Bridge is over-the-air compatible with ZumLink networks and accommodates any WiFi device, including tablets, sensors, smartphones and security cameras. It offers an easy, browser-based configuration that is OEM-ready and features a fully customizable interface. If you are looking for a platform to deliver remote security intelligence applications including human or vehicle presence alerting, activity monitoring and remote access protection outside of network range, look no further than Fusion Bridge. To learn more about this remote WiFi bridge game-changer, as well as FreeWave’s comprehensive portfolio of edge computing solutions, contact your sales representative or visit www.freewave.com. About FreeWave Technologies With deployments in over 39 countries, FreeWave’s products are leveraged by industrial end users and OEMs alike to connect, control and optimize remote machines and processes to impact smarter decision-making, improve operational efficiencies and drive cost savings. Throughout our 27-year history, Freewave’s IIoT Connectivity and EDGE Solutions have solved thousands of customers’ problems in government/defense, energy, agriculture, and municipalities – achieve reliable connectivity for data telemetry and command and control in some of the most challenging, remote and rugged environments in the world. Today, we are transforming the extreme edge of operations – and the proliferation of smart devices within it – into a connected part of the enterprise with our IQ edge computing platform and ecosystem of solutions evolved for IIoT. Are you ready to transform your operation? Visit freewave.com to get started. # # # Media Contacts: Lisa DiBenedetto Corporate Communications [email protected] 630-338-2208 Renea Sloan Director, Channel Marketing [email protected]
FreeWave Technologies Delivers New Edge Data Software Platform
The solution you need for real-time data processing and storage capability at the network edge BOULDER (March 4, 2021) – Today FreeWave Technologies, a leader in industrial edge computing and long-range industrial wireless connectivity, now offers seamless industrial data collection with the introduction of FreeWave Edge. The new software platform performs real-time processing of industrial protocols and sensor data providing edge data storage, processing and cloud compatibility alongside existing enterprise systems. The benefit? Faster, high-resolution data even under challenging connectivity scenarios with added store and forward capabilities. FreeWave Edge marks the first software introduction from is acquisition of CPU LLC, a decades old engineering focused software analytics company that produced multiple software suites in the industrial market. For existing FreeWave customers the addition of FreeWave Edge means greater access to network operations, while adding bandwidth and processing capacity. The platform also drastically reduces the need for additional capital investments. CPU has helped accelerate FreeWave’s momentum into SCADA and digital applications in the cloud. “FreeWave Edge is a direct reflection of our commitment to build a robust and fully-integrated suite of edge computing solutions for industrial customers and system integrators looking to increase network and operation efficiencies and configure data processing at the edge,” said FreeWave’s CEO Kirk Byles. “What all this means is, we listened to our customers who recognize the hodgepodge of hardware and software is hindering their growth, and we created a solution to fill that void. Too many times we’ve heard about how differing protocols can’t work together or hardware isn’t compatible, or…..it doesn’t’ matter. FreeWave is here to provide a bridge between hardware and software in the industrial world. This is our mission and passion.” FreeWave Edge makes it simple to configure custom system alerts and data processing specific to the needs of industrial operations, connecting them to preferred reporting systems, email or the Cloud. Lost connectivity can often mean lost data. Free Wave Edge addresses that with its Store & Forward feature at the edge, ensuring no critical data analytics get left behind. A straightforward web interface allows users to set up data inputs and connect to industrial controllers and devices with standard protocols or sensors via analog and digital IO. The platform also delivers the ability to publish data to a wide variety of enterprise tools via configurable MQTT. To learn more about FreeWave Edge capabilities and specifications, as well as FreeWave’s comprehensive portfolio of edge computing solutions, contact your sales representative or visit www.freewave.com. About FreeWave Technologies With deployments in over 39 countries, FreeWave’s products are leveraged by industrial end users and OEMs alike to connect, control and optimize remote machines and processes to impact smarter decision-making, improve operational efficiencies and drive cost savings. Throughout our 27-year history, FreeWave’s IIoT Connectivity and EDGE Solutions have solved thousands of customers’ problems in government/defense, energy, agriculture, and municipalities – achieve reliable connectivity for data telemetry and command and control in some of the most challenging, remote and rugged environments in the world. Today, we are transforming the extreme edge of operations – and the proliferation of smart devices within it – into a connected part of the enterprise with our IQ edge computing platform and ecosystem of solutions evolved for IIoT. Are you ready to transform your operation? Visit freewave.com to get started. # # # Media Contacts: Lisa DiBenedetto Corporate Communications [email protected] 630-338-2208 Renea Sloan Marketing Director [email protected]
FreeWave Technologies Expands Integration Partnership in India
New Partnership Penned with Cotmac Electronics Pvt Ltd BOULDER (June 10, 2020) – Today, FreeWave Technologies, a leader in long-range industrial wireless connectivity and wired edge computing platforms announced it will expand the distribution of its industrial automation and edge computing solutions to India with new authorized integration partner Cotmac Electronics. As part of the Cotmac Group, established in 1896 as a cotton and machinery trading company, Cotmac Electronics is a respected name in industrial automation. Since its inception in 1992, Cotmac Electronics has grown to employ over 600 skilled and qualified engineers, it has 5 state-of-the-art manufacturing plants and 13 branch offices in India. The company provides innovative solutions for various factory and process automation applications in industries such as automotive, pharmaceuticals, energy, material handling, Oil and gas, as well as water/wastewater. Cotmac Electronics is the first choice in world class industrial automation solutions. “Freewave’s partnership with Cotmac in India is a powerful combination. I am confident that Freewave’s industry leading connectivity and EDGE compute platforms combined with Cotmac’s experience, people and channel reach, will ensure that together, working as one team, we will deliver the full potential of optimized IIoT solutions to verticals and clients across India” said Mike Tate, SVP Global Sales & Marketing, Freewave Technologies. General Manager for Cotmac Electronics, Nitin Apsangi said “The collaboration of FreeWave and Cotmac Electronics will deliver a powerful combination of strengths in the industrial automation space with transformative solutions to help customers achieve the full benefits of IIOT.” “With demand for Industry 4.0 solutions growing, our partnership with FreeWave uniquely positions us to deliver comprehensive solutions for manufacturing, plant automation, process control, and energy monitoring, from the edge to the core to the cloud,” For more information on FreeWave Technologies’ and its Intelligent Edge solutions, visit www.freewave.com. For more information on Cotmac Electronics and its integration capabilities, visit www.cotmac.io About FreeWave Technologies With deployments in over 32 countries, FreeWave’s products are leveraged by industrial end users and OEMs alike to connect, control and optimize remote machines and processes to impact smarter decision-making, improve operational efficiencies and drive cost savings. Throughout our 26-year history, we’ve helped thousands of customers – government/defense, energy, agriculture, and municipalities – achieve reliable connectivity for data telemetry and command and control in some of the most challenging, remote and rugged environments in the world. Today, we are transforming the extreme edge of operations – and the proliferation of smart devices within it – into a connected part of the enterprise with our IQ edge computing platform and ecosystem of solutions evolved for IIoT. Are you ready to transform your operation? Visit freewave.com to get started. # # # Media Contacts: Renea Sloan Marketing Director [email protected]
IIoT and Work-Life Balance: A Healthy and Productive Relationship
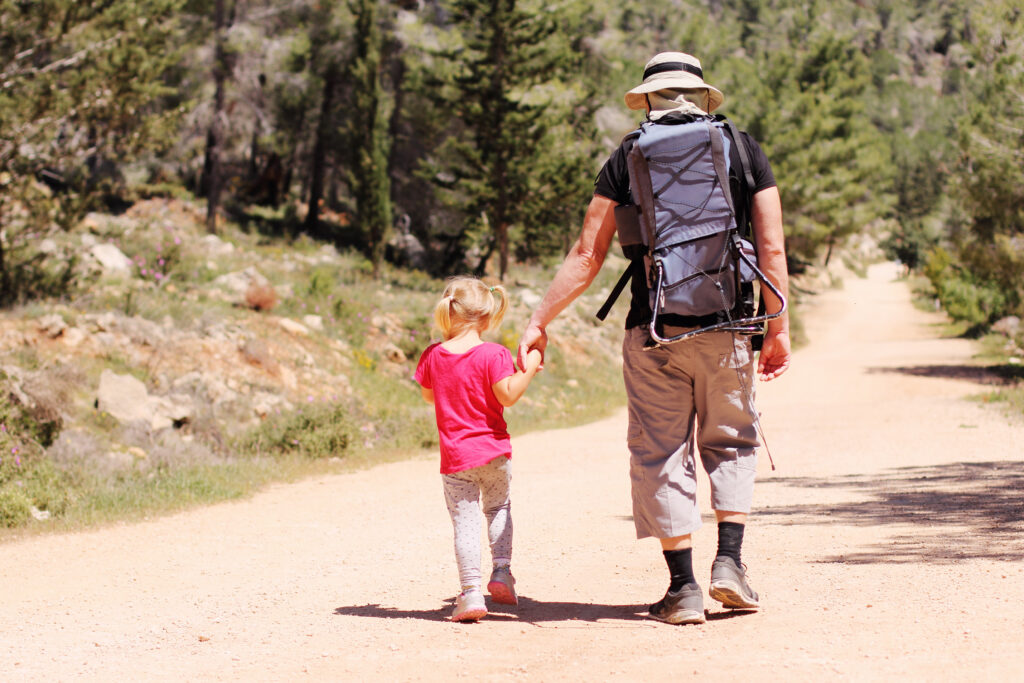
This article was authored by Kirk Byles, FreeWave CEO The Industrial Internet of Things can improve productivity and promote a healthy work-life balance. Here’s how. “There is no such thing as work-life balance anymore. You’ve got to integrate them. Otherwise, you will fail miserably at one of them.” – Benjamin Laker, Forbes Because of COVID-19, the boundaries between our work and home lives continue to blur. I often find myself doing chores while on a conference call or listening to a webinar while cooking at my barbeque. And I’m becoming more interested in who is at the office, now that we’ve opened part-time (I use the key card application on my phone to monitor access). It’s not my intention to be Big Brother – working from the FreeWave office is voluntary. Rather, I want to gauge how folks are feeling. I took the same action to monitor my kid’s activities at home when I was still working from the office, to see whether or not they crank the heat or A/C when they get home from school. These are typical IoT-related activities we take for granted. Like most people, I’ve tried to strike the perfect balance between my life at work and my life at home. Since I’ve worked remotely for most of my professional life, I’m fairly disciplined when it comes to shutting off work at the appropriate time. Still, like so many people, I’ve recently found myself working extended hours. Experts criticize the concept of work-life balance because it suggests life and work are in opposition. And the pursuit of balance is exhausting. Some researchers suggest it’s better to embrace imbalance than strive to achieve a state of work-life nirvana. And I tend to agree with them. Of course, you have to schedule aspects of your work-from-home time, just like you’d plan family activities. Still, there’s nothing wrong with blocking out personal time during the day if you can spend a few hours hiking with your kids or friends during the afternoon. Even if you’ll be working at 10 PM as a result. This balancing act is new to quite a few folks, and it’s difficult. But, if you have the right solutions at your fingertips, it gives you peace of mind and helps you become more efficient. I mentioned mobile apps for my home and office, but what about tools for people working in industries that need to go beyond looking at cameras or names on a screen? Many people work in oilfields, on manufacturing floors, water sanitation sites, farms, or cities. And for most of their careers, they’ve been able to pull data from remote locations, view pressure gauges, monitor flow rates, check on pick and place machines for errors, and in some cases, manipulate those machines remotely (assuming they have the necessary skills). How does this work get done when you have to work from home? The right technology makes it possible. By placing edge computers with industrial applications where the action is happening, people can see the apps at work and relax, knowing they’ll be notified if there is a problem. This helps remote employees see what might be happening, and it also helps them know what is actually happening and how automatic changes improve systems. With edge computers, application-specific software, and communications technologies, folks working from home don’t have to stress about what’s happening on-site. And they don’t have to try to fix issues. The software corrects the issue before you know there’s a problem, so you can cook for the kids and rest easy knowing you’ve had zero downtime and machinery is running at absolute efficiency. The IIoT helps Mom, the field services director for a major utility, work from home, and be 10x more productive because of remote applications at the edge that make sure everything runs as it should. She can spend more time with the kids, and address aspects of her work she couldn’t get to before implementing this technology. It’s about creating efficiencies and solving problems before you even know there is one. An imbalance between work and home life is okay as long as you’re doing all you can to ensure work gets done and your home life isn’t neglected. The Industrial Internet of Things can make this possible for all of us.