FreeWave Named Bronze Winner by American Business Awards and IT World Awards
We here are FreeWave are excited to announce that our ZumLink 900 Radio Series and Industrial IoT Programmable Radio (IPR) have been named bronze award winners by the American Business Awards and the IT World Awards, respectively. The ZumLink 900 series is comprised of the Z9-PE, Z9-T and Z9-C – all of which provide extensive future-proof networking capabilities and are specifically designed to function in extreme, rugged environments. The IIoT Programmable Radio combines the same rugged functionality of the 900 series, along with the added capability of hosting third-party applications that can be deployed at the network’s edge to facilitate secure smart data collection, transport and control. “Our ZumLink technology has been a driving factor behind our ongoing mission to bring intelligence to the network edge,” said Scott Allen, CMO of FreeWave Technologies. “We understand that there is a demand for rugged hardware that can perform the same next-gen data collection, transport and control capabilities of advanced, back-office IT operations. We are extremely excited for the future of not only our technology, but the ongoing transformation of Industrial IoT at-large.” Both the ZumLink 900 series and the IPR are powered by FreeWave’s Zumboost™ technology, which incorporates several leading-edge components of data packet compression and aggregation, as well as forward error correction. These tools not only allow for increased data security, but also enable high-speed transmission critical to the fast-paced functionality demands of the Industrial IoT. Share this: .@freewavetech named bronze winner for ZumLink 900 series & IPR #IIoT networking solution stevieawards.com/aba/2017-new-product-award-winners & www.networkproductsguide.com/world/
Industrially Hardened Time Keeping
Today, a wide variety of industries with outdoor OT assets require technology that can connect the assets to a modern communication network. Depending on the application, the solution is not always as simple as slapping on a cellular or standard WiFi solution. For one, many industries have assets located in remote locations where cellular coverage is limited and long range communication is required. The OT network must also be highly secure and have the ability to avoid interference. Additionally, any outdoor communication network is subject to weather and natural elements. The best hope for maintaining reliable, secure, real-time connectivity is with a solution that is ruggedized, industrially hardened and proven to work in the most extreme environments. Recently we talked about wireless communication solutions used in Antarctica, that are performing under some of the most extreme conditions in the planet. These Frequency Hopping Spread Spectrum (FHSS)-based technologies are built to last and perform with a secure connection. Did you know that the same solutions have also made their way into the sport of boat racing? When November rolls around each year, rowing enthusiasts gather in Chatanooga, Tenn. For the Head of the Hooch race. A total length of 5,000 meters, it is one of the largest and fastest growing regattas in the U.S. Each year more than 2,000 boats race over the course of two days. Participants come in from all over the U.S. and the event has hosted international teams from Canada, Germany, Sweden and Australia. Real-Time Accuracy The race is organized by the Atlanta Rowing Club. In the early days, organizers relied upon stopwatches for keeping time. As the race grew and more boats participated, the manual method of time keeping was no longer feasible. Organizers needed a time keeping solution with a link strong enough to deliver race results in real-time in any weather condition. Organizers selected an industrially hardened wireless communication solution and used it in conjunction with a timing system built for downhill skiing races. The system offers precise timing accuracy – down to 1/10th second for each boat. The wireless solution uses FHSS technology that is typically used in utility-scale Industrial IoT (IIoT) applications. These types of solutions have been used for monitoring and control of outdoor assets in the utility industries for decades and have proven to ensure accurate, real-time connectivity in harsh, remote locations. Not only is the “hopping” nature of FHSS inherently secure, but there are solutions with AES-encryption and other advanced security features to further secure the network. The solutions also offer a range of 60 miles Line-of-Site (LOS), and have proven to be ideal for the Head of the Hooch race. Over the years, races have been conducted in cold, rainy, cloudy and/or windy weather, and the solution has reliably performed in all whether conditions present during the race. Rugged, industrially hardened communication solutions that are well known in the oil/gas and utilities markets – aren’t always the initial choice for connecting non-industrial outdoor networks. In some cases, decision makers in these markets may simply be unfamiliar with the benefits of FHSS. What they need to know is that FHSS solutions have been trusted for years to provide long-range, real-time connectivity, and they are often ideal for a variety of use cases outside of industrial markets. Read the full Head of the Hooch case study here: https://www.freewave.com/case-studies/head-of-the-hooch/
IIoT Top News — Security Remains Top of Mind
Cybersecurity has been top of mind for industry experts and consumers alike. The WannaCry ransomware is putting a legitimate scare into affected companies, although many are apparently preparing to call the hackers’ bluff. Yesterday, another cyberattack was announced as well, and it has the potential to be far more lucrative for the developers. The common denominator between the two? A leaked exploit developed by the NSA that leverages a Windows file-sharing protocol. These attacks are indicative of the long-term game of cat and mouse that the government and private enterprise faces for the foreseeable future of security and counterintelligence. Moving forward, the growing network of connected devices for the Industrial Internet of Things (IIoT) faces similar security threats. This week, we found several stories demonstrating some of the solutions surrounding those potential security issues. The 9 Best Practices for IIoT from a Dell Security Expert At a recent presentation for 2017 Dell EMC World Conference, Rohan Kotian, Dell EMC’s senior product manager for IoT security, spoke about his nine best practices for improved IIoT security. His number one strategy? Simply understanding the concerns. Many IoT devices come out of the box with few security controls in place, and understanding the risk is the most important step in addressing them. In this article from Tech Republic, you can read Mr. Kotian’s other nine best practices, including studying the attack trends, classifying risk, and leveraging fog computing. IIoT Market Expected to Approach One Trillion Dollars by 2025 Grand View Research writes that the industrial Internet of Things will experience explosive growth over the next decade, going from a $109 billion industry in 2016 to an expected $933.62 billion by 2025. The massive market increase will be driven by a number of factors, one of which continued investment by government agencies and corporate leaders. As the report states, “The role of the Internet of Things (IoT) is increasingly becoming more prominent in enabling easy access to devices and machines. Government-sponsored initiatives and innovative efforts made by key companies, such as Huawei, GE, and Cisco, are anticipated to enhance the adoption of IIoT worldwide over the forecast period.” IIoT Presents Unique Security Challenges Security is always a top priority in the Internet of Things, but IIoT applications present unique challenges. In this article from CSO Online, Phil Neray, CyberX’s vice president of industrial cybersecurity, writes that despite the growth of IoT applications in oil, gas, electric, and pharmaceuticals, “The fact is that all of these devices were designed a long time ago.” That means IIoT innovators have the challenge of integrating the newest technology into systems that may be decades old. This sort of retrofitting can make security a real challenge and there are few experts available who have both the knowledge of legacy systems and the latest IIoT solutions. Sprint to Deploy LTW Cat 1 by End Of July The Internet of Things relies heavily on low-power communication protocols to perform, so a recent announcement on FierceWireless.com that Sprint will be releasing LTE Cat 1 by the end of July is music to IoT developer’s ears. LTE Cat 1 is designed to support low-power applications on the Sprint network such as vehicle telematics and industrial IoT applications. “As one of the leading enablers and solution providers of the internet of things, Ericsson believes in its power to transform industries and capture new growth,” said Glenn Laxdal, head of Network Products for Ericsson North America. “Ericsson looks forward to partnering with Sprint to deploy Cat M1 next year and bring the transformative power of IoT to the Sprint Nationwide network.” The announcement also noted that Cat M would be following in mid-2018. TE Cat M1 and LTE Cat NB1 will support other applications requiring ultralow-throughput and power consumption.
Do You Speak the Languages of Industrial IoT?
There is an ongoing transition from a world where having an internet connection was sufficient, to a world where ubiquitous connectivity is quickly becoming the norm. The ability to gather and transport data at high speeds from anywhere is leading to increased automation, smart-everything (vehicles, homes, appliances – you name it), and a standardization of languages and protocols that make the possibilities nearly endless. Recently, IEEE and Eclipse Foundation completed surveys that provided a snapshot on tools, platforms and solutions being used by engineers and programmers alike to build the Internet of Things. According to Joe McKendrick for RTInsights.com, there were several notable conclusions to be drawn from the results, including the revelation that, of the 713 tech professionals surveyed, nearly 42 percent said their companies currently deploy an IoT solution, and 32 percent said they will be deploying/working with an IoT solution over the next 18 months. Additionally, RT Insights writes: “In terms of areas of concentration, 42% report they are working with IoT-ready middleware, while 41% are concentrating on home automation solutions. Another 36% are working with industrial automation as part of their IoT efforts. One-third are working on IoT for smart cities, and the same number are building smart energy solutions.” An interesting note from those conclusions is that 36 percent are working with industrial automation as part of their IoT efforts. Earlier this year, we predicted that Industrial IoT (IIoT) app development would outpace consumer IoT apps, and although this sample size is somewhat limited, it still bodes well for the development of the IIoT sector that is just starting to come into its own. Among IoT developers, there has been a bit of debate over the programming languages that best suit IoT apps. There are situationally appropriate uses for the main languages, but currently, the majority of developers prefer Java and the C language. For developers, being able to build out IoT apps that can work across platforms is a giant step toward standardization. Specifically, in the Industrial IoT, being able to build apps that can function at the Edge to enable smart data collection is a becoming an unofficial mandate for any companies hoping to transition legacy OT operations into the IT/OT convergence movement taking place across critical industries. Of course, building apps is a meaningless task if the hardware being deployed can’t host those apps, a finding that was demonstrated by the survey: Hardware associated with IoT implementations include sensors, used at 87% of sites, along with actuators (51%), gateways and hub devices (50%), and edge node devices (36%). This Edge functionality and sensor deployment are two pieces that are driving the adaption of IoT technology across industries that have traditionally relied on data as the main tool for decision making. However, with smarter hardware, these industries now have the opportunity to improve the efficiency of that decision making – a transformative capability in the industrial realm. Join FreeWave’s ZumLink IPR Pilot Program! What if you could….. Collect, analyze and react to data in real-time at the sensor edge? Reduce BIG DATA that clogs data pipelines? Minimize the cost of expensive PLCs? Control your sensor at the closest touchpoint? The ZumLink IPR App Server Radio combines 900 MHz wireless telemetry with the ability to program and host 3rd party Apps for intelligent control and automation of remote sensors and devices. To participate in the pilot program, visit: https://www.freewave.com/zumlink-ipr-pilot-program/. Pilot Program participants: Receive a complimentary hardware/software Dev Kit Get support from FreeWave software engineers Should have App developer’s skills Let’s discuss: Use cases that would help you or your organization solve a problem Problems you would like to solve Developers that could build this App
Smart Border Protection
Plans for “The Wall” at the U.S./Mexico border appear to be driving forward. Recent reports indicate that building the border protection wall could cost upwards of $22 Billion. However, news coverage suggests that there is a more cost-effective solution in using drones to create a ‘virtual wall.’ Time will tell whether the current administration will consider replacing all or parts of the physical wall with modern drone technology to intelligently monitor rural and desolate parts of the border. In fact, some are reporting that it’s a possibility. On the other hand, several companies have already been selected to build prototypes of the border wall. Perhaps the final solution will be some combination of both, as The Department of Homeland is actively seeking border monitoring solutions in drones for Border Patrol. Drones at the Border In 2014, it was reported that Predator drones were patrolling nearly half the U.S./Mexico border. These drones were used to monitor rural areas for illegal immigrants, human traffickers and drug cartels – covering parts of the border where there are no US Customs and Border Patrol (CPB) agents, camera towers, ground sensors or fences. The Predator drones used for these purposes were designed for the battlefield, and unfortunately a report from December 2014 found that they did not achieve the intended results. Today, The Department of Homeland Security is looking to use smaller drones with facial recognition as part of its Silicon Valley Innovation Program – a program created to, “cultivate relationships with technology innovators, particularly non-traditional performers, from small start-ups to large companies, investors, incubators, and accelerators.” A contractor solicitation notice that was issued last summer (and closed on April 27, 2017) by DHS requested specific requirements for these border patrol drones. According to NBC News, the Department of Homeland Security was “flooded with bids” for these smaller drones. Here’s a small sampling of what the solicitation was requesting (see the full solicitation for the detailed list of requirements): Functional across a variety of weather conditions and times of day Ability to detect the following items of interest within required detection range: humans traveling on foot (alone and in groups), humans traveling on animals (e.g., horseback), and moving ground conveyances (e.g., All Terrain Vehicles, motorcycles, automobiles, and trucks Easy to navigate and operate Sophisticated sensors, with advanced capabilities – such as infrared and facial recognition capabilities sUAS capabilities (sUAS typically applies to smaller consumer-grade drones under 55 pounds) Hypothetical natural language voice command system While the request includes a broad range of desired capabilities, an article in The Verge suggested that, “the greatest challenge facing contractors is how to stream data from the devices, since much of the border lacks conventional cellular service.” Connecting Where Cellular Can’t From a technology standpoint, consumer-grade drones for border patrol are going to need secure, reliable and rugged command-and-control (C2) links. There are a number of secure wireless data communications solutions available that enable reliable C2 links. These solutions have been trusted by the government and defense industry for years, offering secure, reliable links with more than 60 miles Line of Site (LOS). There are C2 solutions providers that have operated in unmanned systems for millions of flight hours in some of the harshest weather conditions without a single broken communication link. Drone manufacturers also should consider these types of C2 solutions because they offer secure wireless data communication by leveraging data encryption capabilities that adhere to FIPS and AES standards. Some non-cellular solutions are also proven to be reliable and secure in nature which further boosts the overall data security scheme. Frequency-hopping techniques, for example, leverage coordinated, rapid changes in radio frequencies that “hop” in the radio spectrum, evading detection and the potential of interference. Some wireless products also deliver multiple user-defined cryptography keys (as many as 32 user-defined keys in some cases), providing a more robust link security by allowing the automatic and frequent changing of cryptographic keys. As drones are deployed more frequently for mission critical operations at our borders, it will be imperative to leverage secure C2 links that can support modern data needs in real-time while keeping the links secure. With the comfort of these powerful C2 links, Border Patrol agents can effectively monitor, assess and act upon threats in the most efficient manner possible.
FreeWave at AUVSI Xponential – Booth #3142
AUVSI XPONENTIAL 2017 is just around the corner and we couldn’t be more excited! Unmanned systems from some of the industry’s leading technology providers will be on display, and we’re looking forward to putting our embedded systems solutions out there as well (booth #3142). It’s a potentially transformative time for the unmanned systems industry. As military spending budgets increase, along with the adoption of unmanned systems for air, land and water, manufacturers and operators will need rugged, reliable and secure C2 solutions with high-speed data transmission. Reliability and security are two extremely critical factors in the ongoing development of unmanned systems solutions, especially for commercial deployments. For years, the government and defense industry has been on the forefront of secure unmanned systems, but as the commercial sector begins to utilize unmanned technology, the ability to ensure secure command and control can be the difference between reliable industry operations and serious injury. Clearly, security considerations for unmanned systems are going to be an ongoing hot topic at XPONENTIAL and into the future. We have spent the past 20 years supplying secure, rugged and reliable embedded solutions for government and defense, precision agriculture and beyond, and as a result, we hold a firm belief that the unmanned systems solutions providers for the next generation need to be hyper-vigilant with regard to the industry. With that in mind, we will be offering demonstrations of our latest C2 solutions for unmanned systems at XPONENTIAL this year. Booth attendees will get a first-hand look at our solutions, offered in a small form factor ideal for drones and robotics that have logged more than 2.5 million flight hours without a single link failure (https://www.freewave.com/unmanned-systems-drones-robots/).
A ‘Heads Up’ on Drone Safety
We all know that what goes up must come down. In the case of drones falling out of the sky, hopefully your head isn’t in the collision path. Drones are becoming increasingly popular for commercial and recreational purposes. According to a recent FAA report, this has sparked an “increase in accidents resulting in blunt impact or laceration injuries to bystanders.” The report, released late last month, generated a fair share of news coverage. It examines the dangers of drone collisions with people on the ground, the risk of injury and ways to reduce those risks. The good news, and probably most newsworthy conclusion, is that if a small drone were to hypothetically fall from the sky and collide with your head, you probably won’t die. One of the tests conducted during the study included dropping a drone on the head of a crash test dummy. The drone used in the test represented a typical drone — a Phantom 3, which weighs about 2.7 pounds. Test results determined that a drone causes significantly less damage than a wood block or steel debris. Findings also showed that the “drag,” caused by air resistance slowed the drone down much more than the wood and steel. A USA Today article reported that while there was only a 0.01 to 0.03 percent chance of a serious head injury, but there was an 11-13 percent chance of a serious neck injury. While the risk of serious injury might be lower than expected, both drone manufacturers and operators of remotely piloted aircrafts can continue to actively take responsibility for the risks by operating from a preventative and safety-focused perspective. A combination of proper training, education and reliable, secure command and control links (C2) can lead each side to a safer drone environment. Knowing the Rules Groups have formed with commercial drone safety in mind. Know Before You Fly is an organization dedicated to educating drone operators on the FAA guidelines for operation. They also offer resources on how to safely and responsibly operate unmanned aircraft systems (UAS). The FAA report also names Academy of Model Aeronautics (AMA), Association of Unmanned Vehicle Systems International (AUVSI), and the FAA as groups dedicated to educating hobbyist and commercial UAS users on the important requirements for piloting UAS. New drone operators who leverage the assortment of educational tools available can help champion the pursuit of responsible drone operations. Building Drones with Reliability and Safety in Mind In addition to training and education from the operator perspective, when the right command-and-control (C2) solution is in place, drone operations can become much more safe and reliable. Secure wireless data communication solutions that leverage data encryption capabilities, adhering to FIPS and AES standards, are already heavily relied on for mission-critical government and defense applications. Additionally, certain types of wireless solutions, like Frequency Hopping Spread Spectrum Technologies (FHSS) are secure in their nature. For example, frequency-hopping techniques can leverage coordinated, rapid changes in radio frequencies that literally “hop” in the radio spectrum, thus evading detection and the potential of interference Some wireless products also can deliver multiple user-defined cryptography keys (as many as 32 user-defined keys in some cases), providing more robust link security by allowing the automatic and frequent changing of cryptographic keys. In addition to secure data, these solutions also offer distance. There are FHSS radio solutions that can transmit more than 60 miles Line-of-Sight (LOS). When the communication links are robust and prevent interference, they are much less likely to be jammed or disrupted, ultimately preventing drone performance issues (i.e., falling from the sky). This is a very important consideration because of the growing number of unmanned vehicles operating in industrial and commercial sectors today. With a secure and reliable wireless C2 link, these technical issues are substantially reduced. Drones have opened the door for many hobbyist and commercial opportunities, but that also means there are more inexperienced operators. If an operator educates themselves on the FAA guidelines and safety procedures when operating a drone, and the manufacturers build in a secure and reliable C2 link that works over long distances, then both are taking the steps to decrease drone-related injuries. Although the FAA report shows the risk of serious injury and death is low, manufacturers and operators still need to keep safety a top priority.
ZumLink Firmware Update 1.0.4.1
FreeWave announces the release of firmware version 1.0.4.1 for all ZumLink Enclosed Ethernet Radios (Z9-PE and Z9-PE-DEVKIT). This new firmware version includes improvements which are not backwards compatible in frequency hopping mode with the original firmware release (1.0.3.2) so it is required that all radios be upgraded to the same firmware version. FreeWave recommends that your radios get upgraded with the new firmware version to take advantage of improvements and additional features, including: IP Filtering – Prevents IP addresses not within the IP subnet from being transmitted. Repeater – Allows a single radio to repeat (store and forward) traffic from one radio to another. Terminal Server Activity Timeout – Provides a settable time that closes the port when no data is received through the socket connection for longer than the timeout period. Diagnostic Support Bundle – Generates a zip file containing all the configuration and diagnostics information when IP address followed by /support is typed in a web browser. You can download the new firmware version from the Support Section of the FreeWave website. Note that you must be logged into the Support Knowledge Base to access and download. A complete list of changes and improvements will be included in the updated Release Notes and User Manual which will also be found on the Support website. Please contact FreeWave Tech Support for more information or assistance.
British Antarctic Survey Leverages Ruggedized Data Transport
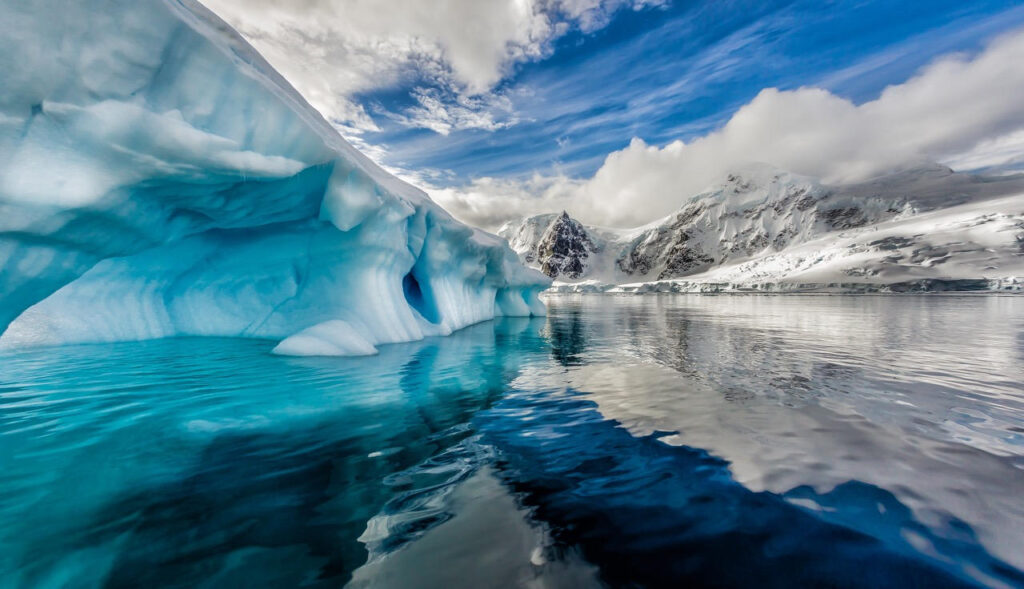
Antarctica inhabits a unique place in the human exploration mythos. The vast expanse of uninhabitable land twice the size of Australia has birthed legendary stories of human perseverance and cautionary tales about the indomitable force of nature. However, since those early years, Antarctica has become a rich research center for all different kinds of data collection – from climate change, to biology, to seismic and more. And although today there are many organizations with field stations running this data collection, the nature of its, well, nature still presents daily challenges that technology has had a hand in helping address. Can You Send Data Through Snow? British Antarctic Survey (BAS) – of recent Boaty McBoatface fame – has been collecting data from its field station network for more than 60 years. Over that time, BAS has become a global leader for polar science and polar operations, collecting data on sediments, ice cores, the polar atmosphere and the ever-changing ice shelves – all of which are vitally important for helping predict the climate of the future. To collect this data, BAS required a network that could reliably transmit it in what could be considered one of the harshest environments on the planet. This means deploying GPS equipment, motion and atmospheric sensors, radios and more that could stand up to the daily tests. In order to collect and transport the data in this harsh environment, BAS needed a ruggedized solution that could handle both the freezing temperatures (-58 degrees F in the winter), strong winds and snow accumulation. Additionally, the solution needed to be low power due to the region’s lack of power infrastructure. The Solution BAS found that FreeWave’s 900 MHz radios could handle this myriad of requirements. The organization deployed 19 radios across its network, each connected to a remote GPS station containing sensors that track the movement of the Brunt Ice Shelf near one of the primary research stations. The GPS sensors determine the Shelf’s position and dynamics before sending the data back to the station. There are several other specs that make the deployment of these radios operationally viable for British Antarctic Survey, but to find out more check out our case study with all the details: https://www.freewave.com/case-studies/british-antarctic-survey/!
IIoT Top News: Internet of Things Growth Continues at Dizzying Pace
The Industrial Internet of Things, or IIoT, has fundamentally transformed the way organizations not only conduct business in their current day-to-day operations, but also has changed the way businesses plan for the future. The explosive growth in data, and the corresponding business decisions driven by that data, is causing a massive ripple effect through the industry and is driving hyper-growth in software, hardware, cloud services, security and integration platforms. Here are some of the recent headlines in IIoT that are shaping the landscape. IIoT’s Growth Shows No Signs of Slowing A recent report released by ABI Research and published by Fierce Wireless forecasts that industrial manufacturing applications will generate more than $138 million this from cellular and satellite connectivity fees alone. Driving this massive fee generation is the expectation that the IIoT will exceed 53M installed connections in 2017. The largest marketplace for this activity is the Asian-Pacific region, where an additional 5 million connections are expected over this year. IIoT Security Concerns Increase While the IIoT is experiencing massive growth, new security concerns continue to arise. A new study from Tripwire published in IoT Tech News sought insight from 400 IT professionals who describe security as a “significant” part of their job. Of the respondents, over 50% say they do not feel prepared for security attacks that exploit unsecured IIoT devices. 94% of those same respondents believe that the IIoT exposes their organizations to increased vulnerability for cyber attacks. Robert Westervelt, security research manager at IDC, said: “The apparent contradiction of known risks and continued deployment demonstrates that security and operations need to coordinate on these issues. While IIoT may bring new challenges and risks, the fundamentals of security still apply. Organisations do not need to find new security controls, rather they need to figure out how to apply security best practices in new environments.” IIoT is Booming — But is Your Company Ready? Industry leaders across the globe are making large-scale investments in the IoT — but are they ready for all the challenges that come along with it? In a recent report developed by the BPI Network and featured in the Data Center Journal, 52 percent of executives at large enterprises expect IIoT to have a significant or major impact on their industry within three years — yet only 1.5% of executives surveyed say they have a clear plan and are on their way to implementation. These aren’t leaders from small brands, but executives from huge organizations like Whirlpool, Hitachi and Philips Lighting. And what is these executives biggest concern about the IIoT? You guessed it — security and data privacy. Robotic Automation Changing the Workforce Secretary of the Treasury Steve Mnuchin recently made news when he claimed that the effect of automation on the U.S. workforce is still “50 to 100 more years” away. A recent working paper from the National Bureau of Economic Research strongly disputes that. As written about by the MIT Technology Review, the NBER claims that just in the time period from 1990 to 2007, as many as 670,000 U.S. jobs were lost to automation. Despite this significant impact, robots are still relatively scarce in the U.S. economy. With the growing strength of the IIoT, the number of robots used for automation are expected to increase rapidly, and it will be worthwhile to monitor the impact on the U.S. labor force, particularly in the area of manufacturing.