International IIoT Perspectives: Smart Cities
The Industrial Internet of Things (IIoT) is, at times, hard to pin down. The stronger the technology has gotten, the broader the applications have become, affecting everything from energy, to smart cities to manufacturing, and in the process, blurring the line between traditional consumer and industrial markets. Interestingly, in the United States, much of the Industrial IoT advancements have come from the private sector – oil and gas, utilities, precision agriculture, etc. International IIoT, however, has seen real advancements coming from cities – smart cities, that is. Smartest Cities in the World A 2015 article from Forbes provided a list of the top five smartest cities in the world based on a number of factors, including environmental monitoring, smart traffic management, data usage and creative tech applications. Barcelona topped the list, with New York City, London, Nice (France), and Singapore rounding out the top five. In each instance, the use of smart technology improved quality of life, efficiency, and better overall functionality. Of course, there are myriad factors to consider when evaluating a city’s “smartness,” but considering how many moving parts – literally and figuratively – that it takes to create a smart infrastructure, the breadth of application is impressive. Barcelona’s comprehensive wired network drives an infrastructure that is constantly aggregating, transmitting and analyzing data for all kinds of things: The boxes are no regular electricity meters. They are fine-tuned computer systems, capable of measuring noise, traffic, pollution, crowds, even the number of selfies posted from the street. They are the future of Barcelona, and in some sense they are the future for all of us too. The hard drives are just one piece of what is “unusual” on this street, in fact. Cast your eyes down, and you might spot the digital chips plugged into garbage containers, or the soda-can-size sensors rammed into the asphalt under the parking spaces. The paragraph above not only highlights the often hidden aspects of smart cities – sensors, hard drives, boxes – but also the sheer magnitude of the data being collected from wherever possible. The technology that powers that data collection lies in the actual communication networks, which are powered by an array of RF, cellular and WiFi connections. Today, many of the devices that are responsible for collecting the data from the source – the access layer – are capable of hosting third-party, proprietary applications that can filter and transmit data in specific packages, turning Big Data into Smart Data. Lately, London has focused on green energy and environmental progress. The city launched an initiative to become a zero-emission city by 2050 with a combination of electric vehicles and public transportation. Sounds familiar, right? The actual mechanisms driving that initiative are not necessarily ground breaking: reduce combustion engines on the road, encourage people to use public transport. However, the technology has finally started to catch up. With smart traffic monitoring capabilities, public transportation can run more efficiently, keeping to strict schedules. Additionally, driverless vehicles can perhaps help lead a transportation infrastructure devoid of human-caused accidents, opening the road systems and, again, leading to greater efficiency. Smart Cities, Smart World Of course, the two examples above come at a high level. There are significant technologies driving the actual implementation of smart city devices, but the key factor is that the leaders of the respective cities understand the need for a stronger, smarter infrastructure. Many other cities are catching up – India often pops up with smart city initiatives, which is a fascinating case study based on the economic disparity of the country. Still, the drivers of the international IIoT goals often point to the development of smart cities as an ideal outcome based on the continued growth of connected technology.
Autonomous Tech and Self-Driving Cars Dominate the Headlines
The autonomous tech industry is poised to explode, driving job growth and technological innovation. Everything from self-driving vehicles to automated infrastructure is sitting on a precipice of advancement that can be a truly momentous step into the era of the connected world. This week, we are focusing on some of the industry news surrounding autonomous vehicles, including the manufacturing aspect, their space in a smart city, and how major metropolitan areas initially resistant to the technology are starting to come around. In Japan the Race is On for Self-Driving Cars IMAGE by Takashi Aoyama According to a recent study by the Boston Consulting Group, fully autonomous vehicles are expected to account for a quarter of all new cars by 2035 — a slice of the auto industry totaling around $77 billion. While automakers across the globe are racing to become a leader in this new tech, no where is the competition more intense than in the auto-manufacturer rich island nation of Japan. This recent article from the San Francisco Chronicle notes that Toyota, Nissan and Honda have all made significant investments in developing autonomous tech. The autonomous vehicle race is particularly impactful because of the major implications to not only car OEMs who have to fundamentally change the way they approach their product, but to the hardware and software companies building the technology that will support these highly sophisticated (and regulated) vehicles. Could Owning an Autonomous Car Make You “Traffic Elite”? IMAGE courtesy ZDNet If you end up being an early adopter of new autonomous tech, you may find your commute becomes shorter. ZDNet explains that a recent proposal from UC Berkeley grad students suggested the creation of a “Hyperland” — a special traffic lane reserved just for self-driving vehicles. If you want to be in the Hyperlane, you better not mind a brisk ride as the special lanes would allow for speeds over 100mph. The traffic on the Hyperlane would be controlled by a central computer that monitors traffic congestion, speed, and other variables through advanced sensor arrays and keeps traffic flowing freely. The project will cost a cool $11.4 per mile of road, so travel will likely come with a toll to ease the financial burden. Self-Driving Cars Job Market Booming IMAGE by Gene J. Puskar, AP With so much emphasis on autonomous driving, cities are rushing to cash in on the movement. According to the Detroit Free Press, the advanced driver assistance systems and autonomous vehicle market was around $5 billion in 2015. It’s projected to grow to $96 billion by 2025 and a staggering $290 billion by 2035. This massive market growth has led to a number of cities across the country pitching their location as the “place to be” for autonomous tech. From Austin to Pittsburgh, automakers, OEMs and even government officials are pushing for their city as the best spot for innovation in the autonomous vehicle space. So will it be Detroit or Silicon Valley? Or one of a host of other cities vying for a slice of this massive cash cow? Time will tell. Better Late than Never: New York Easing Up on Laws for Driverless Vehicles Back in 1971, New York passed a state law insisting all motor vehicles have a driver with at least one hand on the wheel at all times. Back then, this seemed that a pretty standard rule — but with the advent of self-driving cars, the rules of the game have changed. A recent article from the Democrat and Chronicle noted that until recently, New York was the only state the explicitly banned driverless cars from its roadways. However, the state has now approved a pilot program to allow the testing of driverless vehicles under certain conditions. State Senator Joe Robach was a vocal advocate for the new change. “While the technology for fully driverless cars is in the future, consumers certainly appreciate the automated technology that is currently in cars, including lane assist, self-braking, hands-free park assist and collision avoidance,” he said. “The legislation that was passed earlier this year ensures that driverless cars can be tested on the roads that future consumers in our state will use them on and are tested responsibly.” Audi of America is the first automaker to get approved for the new program, with other manufactures expected to jump on board in the coming months.
Robotics on the Battlefield
We’ve all seen those futuristic Sci-Fi movies where man and machine fight alongside each other in the throes of battle. While that might have seemed far fetched years ago, the reality is that robotics are increasingly becoming a part of our military today. In fact, the Pentagon recently requested prototypes of combined human-robot squads. As the robotics industry becomes increasingly important to military officials, technology providers are working hard to develop solutions that will support increasingly automated military efforts. A recent report estimates that robotics in the military will grow at a CAGR of 9.5 percent between now and 2023. According to the same report, robotics will be most used by the military in Europe during this time frame, followed by North America. The U.S. military continues to test out the possibilities for leveraging robots to protect soldiers, increase visibility in combat situations and generally streamline operations. Not only are these robotic applications groundbreaking — but they’re also really cool. News stories on new robotic technology boast of robotic ships, heavily armed unmanned ground vehicles, and robotic tanks – with more innovative technology coming out all the time. For example, there is a robotic insect called the “RoboBee” which was created for crop pollination and disaster relief efforts, but could also potentially lead to robotic insects used for military purposes as the true “fly on the wall” concept — equipped with audio and visual capabilities. There are also recent reports around the push for robots designed to carry wounded soldiers out of battle instead of forcing medics to enter live combat zones. These robotics may also support troops behind enemy lines in a variety of other ways to prevent risking more lives, such as dropping medical supplies to soldiers in dangerous areas. Future technologies may have the power to deliver specific medicine and even blood to wounded soldiers. While there are robotic models being tested and deployed around the world, perhaps the most uncertainty lies in the data. A Data Disaster? As recently reported in Popular Mechanics, the robotics of tomorrow may be facing a serious data problem. The article notes that for one, robots are both consumers and creators of data. Technology needs to be able to sustain the sheer amount of data required for robotic operations. The article also highlights the importance of collecting and using the right data instead of ALL the data. The good news — thanks to the Industrial Internet of Things (IIoT) — is that modern technology is becoming more favorable for managing data and it will further be supported by secure command and control (C2) links. Wireless data communications solutions are available that enable reliable C2 links have been trusted by the government and defense industry for decades. Not only are they proven in combat, but they are applicable for today’s complex data-centric systems, including robotics. With appropriate security measures and encryption capabilities in place, C2 links can be better protected to thwart malicious attacks on these automated systems – a critical function when the C2 links enable operations of the device. Further, when frequency-hopping techniques are used there is an additional layer of security, as these types of devices leverage coordinated, rapid changes in radio frequencies that naturally avoid interference. When FHSS technologies are combined with FIPS and AES security standards, as well as multiple user-defined cryptography keys (up to 32), they are equipped with a highly robust link that is well suited for military and combat operations. While robotics brings concerns to the data conversation, technology providers are working to keep up with modern data needs. With a secure C2 link, technology is further hardened for combat applications. It will be interesting to see the developments in robotics for the military in the next couple of years. What are some of the most interesting robotics applications you’ve seen?
7 Tips for OEMs to Improve SCADA Networking Communications
From remote field sensors to Supervisory Control and Data Acquisition (SCADA) and I/O modules, industrial wireless radios connect your device and sensor ecosystems with robust and reliable links. Furthermore, wireless data radio networking technology connected to I/O modules for SCADA applications have become faster, smarter and their firmware now easier to upgrade. More options and frequencies, including 2.4 GHz for short range I/O and 900MHz for long range data networking, continue to improve SCADA-based network communications for robotics, industrial automation, unmanned systems and heavy machinery. So what do Original Equipment Manufacturers (OEMs) need to know when deciding upon which technology to use? Below are seven tips for OEMs to consider when reviewing industrial wireless communication options. 1) Assess Technology Options for the SCADA Network Start first by identifying your needs, goals, and limitations. When it’s time to research technology options, observe what’s available today and what’s going to be available in the future, heeding the “buyer beware” saying. Communication products vary in many ways, and each manufacturer and/or technology has advantages and disadvantages. No single product—and likely not a single manufacturer—can meet all application needs. 2) Reduce Costs While some companies seek to continue to preserve existing investments of wired and wireless technologies, wireless options have clear advantages for SCADA systems. Most obviously, wireless installations reduce labor and material costs by avoiding hard-wiring remote assets. Speed of deployment adds savings. Wired systems can take days or weeks to be properly installed. Wireless networks generally require only the end points to be installed, saving substantial time and costs. Networks need to scale gracefully as the number of end points increases. After installation savings, scalability is the biggest advantage of wireless over hard-wiring, including slow integration into wired systems as it’s implemented. 3) Consider Hybrid Benefits Toss out any old perceptions. If you need mobile SCADA network access, find somebody that offers it. If you have a microwave tower place, use it. Piggyback slower licensed radio networks with faster 902-928 MHz frequency hopping, AES encrypted networks. Know that you can install I/O capable radios (analog and digital signal, 4 to 20 and 1 to 5) to relay contact closures or other data without adding a new Progammable Logic Controllder (PLC) or Remote Terminal Unit (RTU). 4) Maximize SCADA System Value With telemetry technologies, such as spread spectrum radios, the same radio used in RTUs can act as a slave device sending data back to the SCADA host, and as a repeater to other field devices or other RTUs. This allows almost limitless network expansion by using remote sites as a series of repeaters, and by using radios in the RTUs to poll the instrumentation. Polling the instrumentation creates a second network reporting wirelessly back to the RTU. This shorthaul network is the equivalent of a local area network (LAN). 5) Don’t Use a Proprietary SCADA System By using a non-proprietary SCADA system, users gain real-time access, control, and monitoring of their network (including all the devices and functions of their network). They can manage requirements of an ever-growing system allowing them to manage their network in real-time with fewer bodies and hours invested. Security and safety improves with better monitoring. For instance, some industrial systems don’t contain a process for monitoring the cathodic integrity for corrosion (like in water/wastewater and oil and gas) to avoid disaster. But with deployment of a wireless system, they can. They can begin by monitoring simple things, such as pump stations at wells, using I/O radios communicating back to the central SCADA system to get up-to-date information on the tanks’ or pipelines’ status. End users can more quickly resolve an emergency wirelessly, instead of manually. 6) Seek SCADA System Flexibility Advanced flexibility of radio communications offers benefits to new SCADA system deployments and upgrades performance of existing SCADA systems. For example, in water/wastewater industrial applications, there need to be generation/distribution, lift stations, system monitoring, and treatment facility systems in place (or planned) to meet the expanding growth of a community’s population and/or service areas to meet future requirements. Each year, many industries deploy more frequency hopping spread spectrum (FHSS) SCADA solutions to help monitor and manage critical infrastructure. Several manufacturers (including FreeWave Technologies) offer FHSS radios capable of retrieving data from remote locations. And although wireless IO (input/output) has been available, only recently have both capabilities been offered in one communication solution. 7) Seek Easy-to-Use SCADA Software OEMs implementing and using a SCADA network systems for data communications want a simplified, rapid setup and easy management of a network. That includes ability to manage multiple frequencies and multiple networks within one system. A centralized storage and management center provides easy access to system configuration and diagnostics data. Technicians in remote or harsh weather environments need robust reporting capabilities. Software like FreeWave’s ToolSuite can manage data communication diagnostics and configuration.
Utilities & IIoT: The ‘Perfect Storm’ Meets the Revolution
In early 2017, John Kennedy at SiliconRepublic declared the Industrial Internet of Things (IIoT) the ‘perfect storm’ – a convergence of technologies with the capacity to create new economic benefits based on operational efficiency. On these blog pages, we’ve covered many different facets of industries adopting intelligent communication technologies likes sensors, programmable radios, and powerful analytics tools, but one industry in particular seems poised for the greatest upheaval: utilities. Many industry experts are pointing at utility markets as poised for revolution. So, what happens when the ‘perfect storm’ meets the revolution? Critical Infrastructure Transformation Given the way the human population is dispersed in the United States (and abroad), cities play a huge role in driving the growth of IIoT technologies in utilities. Water and wastewater treatment plants are perhaps one of the most important (and overlooked) pieces to modern infrastructure. Without these plants, after 1-2 uses, most of the water in North America would be unusable. Instead, companies are using sensors and other connected monitoring devices to create smart data that informs decision making, eliminates variables, and improves effective responsiveness. Similarly, the electric grid has seen significant transformation as well. In the era of the smart grid, we now have the ability to monitor grid activity more closely, deploy electricity more efficiently based on usage spikes, and allow consumers to track their own energy usage. The residual effect of this tracking is, perhaps, an increased awareness of how we use energy on a daily basis and could lead to better individual conservation efforts. Alternative Energy On The Rise And speaking of conservation efforts, with the ability to use energy more efficiently, alternative energy has exploded as viable alternatives to our traditional resources. Wind power has grown into a consistent source of energy, but for years, operators needed a better way to monitor the energy systems. Today, IIoT technology not only allows better monitoring, but provides real-time management capabilities for operators. The name of the game is efficiency, and if the operations are efficient, then the usage can be efficient as well. Business Convergence Since utility companies are now better equipped to understand when and how resources are being used or deployed, they can streamline some of the day-to-day operations by building a network of smaller solutions that are specifically designed to meet niche needs, creating more business opportunities for both traditional and alternative utility providers. Although many doomsday scenarios point to increased automation as the death of the worker, with a greater diversity of solutions, the economic impact might actually provide more jobs instead of fewer. Relying on the traditional model of the last half-century, however, does not. Ultimately, we are still looking at an industry that is right on the cusp of revolution. Utilities have, historically, been slightly slower to respond to technology overhauls at a high level, but with the added efficiency and financial benefits that accompany IIoT adoption, companies are rethinking old strategies and pushing into a new frontier – confronting the ‘perfect storm’ head-on to ensure the best possible landscape once the dust settles.
Intelligent Decision Making in Precision Agriculture
Modern businesses are making intelligent business decisions thanks to the Industrial IoT and its push towards increased connectivity. In precision agriculture, new technology has the potential to be a game changer for crop management, enabling more visibility over crops and intelligent decision making that directly impacts food output. However, according to a recent article from CropLife magazine, while farmers are leveraging automation, the precision agriculture industry as a whole is relatively new in comparison to the traditional agriculture industry, and so is the adoption of IT technology. The exciting news is that farmers are increasingly turning towards automation to streamline operations. As automation and connectivity are adopted for precision agriculture, there is an emerging market for drones that is ripe with possibility. A recent article focusing on drones in agriculture reports, “With precision agriculture, farmers can now rest assured that they are making crucial decisions correctly and intelligently – made easy through drone analytics.” Drone manufacturers are actively working to make technology that they believe will change the game for precision agriculture. They aim to improve food production and more efficiently distribute pesticides and water. Drones may also aid in disease management for the diseases that rapidly spread through crops. With the use of cameras, drones are also able to offer farmers real-time visibility into the health of their crops. With the rise of drones in the commercial and industrial sectors we see a lot of opportunity for drone manufacturers, technology providers and farmers alike. What we also see as a key to success in all these areas is technology that performs with consistency and reliability. In the case of drones, without secure and reliable command and control (C2) links, drone performance will suffer, and as a result so will the important data that farmers will find essential to making intelligent decisions. Command and Control Links There are technologies available that have proven to unfailingly support critical drone operations. In fact, after decades of serving mission-critical applications in government and defense, the same C2 capabilities of advanced wireless data communications have begun to migrate into the commercial and industrial drone markets. Today, there are a number of secure wireless data communications solutions available that enable reliable C2 links and have been trusted by the government and defense industry for years. Additionally, there are solution providers that offer multiple frequencies for C2 links offering unmanned systems manufacturers a portfolio of options to deploy. In addition to frequency options, when the appropriate security measures and encryption capabilities are in place, C2 links can be better protected to thwart malicious attacks on unmanned systems. For the precision agriculture industry this means less downtime and reliable drones for operations that are critical to the health of the crop. Drones and other modern IT technologies are disrupting the precision agriculture industry, but there is substantial potential for a big impact on the farming industry as a whole. As drones are developed to carry out these applications in precision agriculture is especially important to ensure they are being created with the C2 links that will support modern connectivity needs.
IIoT News Headlines: Trains, Agriculture, Underwater and More
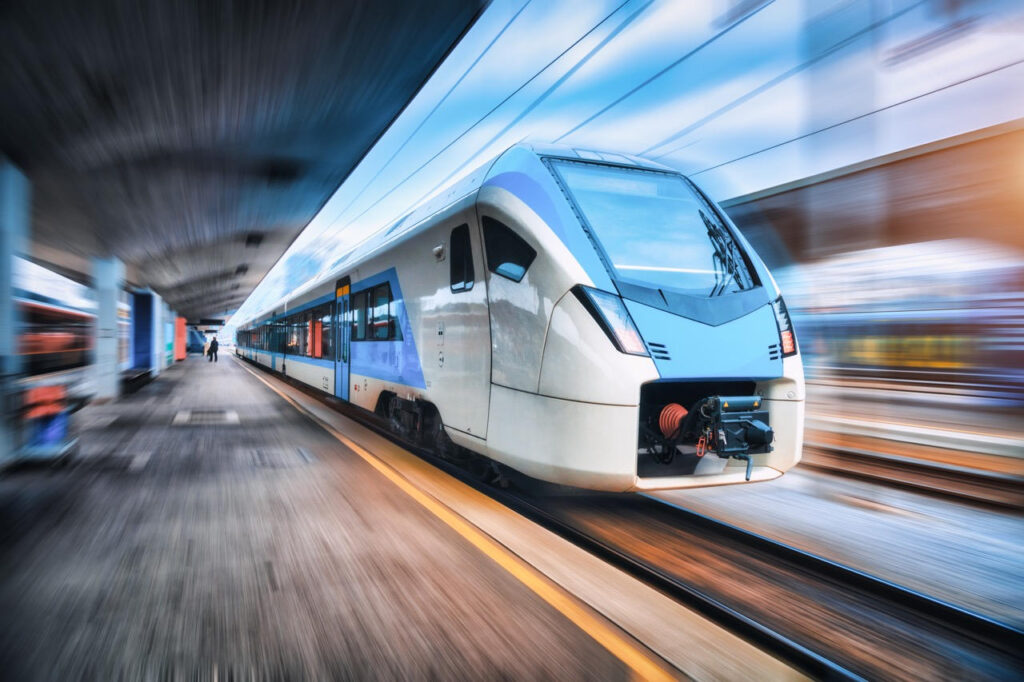
Industries around the world are being transformed by the Industrial IoT. We recently shared a blog with a report that estimates IIoT will experience explosive growth and approach one trillion dollars by 2025. From trains and under water applications, to agriculture, we are already seeing IIoT expand its reach today. However, we continue to see security as one of the biggest challenges – which continues to top news headlines. Below are some of the recent IIoT stories that have caught our attention: How Siemens Is Using Big Data And IoT To Build The Internet Of Trains By: @BernardMarr | Published on: @Forbes “Siemens AG is one of the world’s largest providers of railway infrastructure, serving rail operators in over 60 countries. Through harnessing Big Data, sensors and predictive analytics they say they can now guarantee their customers close to 100% reliabilit It calls this the “Internet of Trains” – the on-rails segment of the wider ‘Internet of Things’ concept which describes how everyday objects of all shapes and sizes can now be connected together online and given the ability to communicate and capture data for analytic purposes.” Agriculture Is The No. 1 Opportunity For African Internet Of Things, Security The No. 1 Challenge By Tom Jackson | Published on: @AFKInsider “Agriculture, Africa’s largest economic sector, is likely to be central to the growth of IoT. There are many examples around the world where value can be unlocked from enhanced efficiencies along the value chain. Mining, oil and gas, telecommunications and manufacturing will have to adopt IoT to improve efficiencies.” The Internet of Underwater Things Published on: @NauticExpo_eMag “The development of an Internet of Underwater Things (IoUT), transmitting data throughout the ocean could make possible a system of roaming, autonomous vehicles and underwater sensors, all communicating with each other and relaying information to networks above the surface. This could be used for a wide range of submarine tasks, from pipeline repair and shipwreck surveys to seismic detection and ecological monitoring.” IIoT and The Cyberthreat: The Perfect Storm of Risk By: @ChrisGrove_Geek | Published on: @MBTwebsite “Many of these newfound risks did not previously exist, mostly due to the lack of interconnectivity and the network ‘air-gap’ — which has become a thing of the past. As industrial organizations race to keep up with advances in manufacturing technologies, IT is increasingly encroaching into the OT world. It’s no longer uncommon to find IT technologies like Ethernet, Wi-Fi, the Cloud and cybersecurity products like virus scanners, firewalls, Intrusion Detection/Prevention Systems and Security Information/Event Management (SIEM) products being managed outside the purview of IT.” It will be interesting to see how the IIoT continues to transform industries. What are some of the interesting use cases you are seeing as the IIoT growes? What are your biggest security concerns when it comes to IIoT?
Connected Oil Fields in Peru
China National Petroleum Corporation (CNPC) is one of the largest energy companies in the world with operations in 28 countries. In May 2017, CNPC announced it would invest $2 billion in an oil and natural gas block in the southern part of Peru. Beyond the recent investment, CNPC has had a presence in Peru for more than 20 years, including oil fields in the northern portion of the country. To optimize operations in 2009, CNPC ran a pilot test in Piura, Peru to find the ideal communication solution for monitoring, collecting and transporting data. Piura is a coastal city located near the equator where the average temperatures hover around 95 degrees Fahrenheight. To connect the oil fields into the Supervisory Control and Data Acquisition (SCADA) system, CNPC needed a communication technology built to withstand harsh weather, such as high temperatures, large amounts of rain, wind and a variety of other environmental factors. The goal of the pilot was to have several test sites reporting to a gateway and then into a SCADA system to monitor several pumping devices and equipment including: Pump of Controller (POC), Pump Cavity Progressive (PCP), Balance Oil Recovery System (BORS) and plunger lift. FHSS for Oil and Gas In the Piura test case, the distances between links weren’t long, but depressions, canyons and steams made line-of-site (LOS) a challenge. CNPC, who tested multiple Machine-to-Machine (M2M) communication solutions in Piura, found that FreeWave’s Frequency Hopping Spread Spectrum (FHSS) technology solutions offered the most reliable connectivity in comparison to other solutions used during the test. FreeWave solutions also use repeaters that helped establish and maintain connectivity despite the lack of LOS. Additionally, the links were established easily and fast in comparison to other solutions that were a part of the test. During the entire three-month pilot, the FHSS-based M2M solutions did not lose communication or the ability to send data to the SCADA system. Industrially hardened, ruggedized FHSS technology has proven to be reliable in in many oil and gas installations around the world. As the Industrial IoT (IIoT) drives connectivity, we continue to see the demand for reliable communication links in environments like Piura that can have challenging conditions. FHSS technology offers not only a reliable, easy to install communication link, but it easily integrates into today’s modern IIoT networks. To get the full story about the test sites in Piura, read the case study: https://www.freewave.com/case-studies/china-national-petroleum-company/
Can Oil and Gas Keep Up with Digital Disruption?
The oil and gas industry has faced transformational potential in the last several years. As a critical piece of infrastructure for nearly every industry – and the economy – it’s ability to keep pace with the lightning rate of technological upheaval has been challenged. The convergence of IoT, the Cloud and Big Data has created a whirlwind of possibilities, but the major challenge will be whether the industry can successfully unify its data collection and transport at the necessary scale. There are several factors that will determine the ultimate success of this data: hardware capable of handling the consistently rugged environment, reliable connectivity, a general consensus on the best programming language for widespread use, and the applications capable of transforming Big Data into Smart Data. Rugged Hardware Most well pads are set in remote environments where the conditions are rugged or downright extreme. Not only are RF communications greatly affected by these conditions, but as the connectivity shifts toward (potentially) remote WiFi, then the devices must not only be more sophisticated, but that sophistication must be ruggedized as well. We recently published a case study that shows how our radios held up in a cool use-case in Antarctica for data collection in an extremely harsh environment. Granted, most oil companies are not looking Antarctica as a possible drilling location, but the visual does a good job of showing just how rugged the hardware needs to be. It cannot fail when delivering data to companies, as that data is more important than ever. Reliable Connectivity There are several different methods for connectivity at remote locations, but two that are gaining ground on traditional systems are Frequency Hopping Spread Spectrum (FHSS) and WiFi. Of the two, WiFi faces the greatest obstacles because it relies on several different transfer or booster points, but its strengths as a transport method are starting to outweigh some of those challenges. FHSS has been around for quite a while, but the technology, surprisingly, is still somewhat misunderstood. The ripple effect from its applications are felt throughout many industries, but the key differentiators are its consistency and reliability. Programming Languages Today, there is hardware on the market that is capable of putting proprietary, third-party applications at the edge. But, in order for these apps to be effective, the industry needs to find the programming language that best serves the need. It’s similar to when personal computers were first hitting the market. Each PC company wanted its computer to run its own kind of software, but the industry ultimately realized that best chance for success was to create a standard. Since then, even though open source is still a critical piece of software development, most PCs and other platforms can basically run the same kind of software. This same approach to standardization needs to be taken with programming languages or the battle for supremacy will continue to fracture an industry at a time when it needs cohesion for maximum growth. Edge Applications Speaking of finding a unified programming language, the result of that will be an explosion of applications that can be deployed on the aforementioned hardware. Once companies have the ability to create these applications to fit specific needs, then they will be able to take Big Data and turn it into Smart Data. A hallmark of the Industrial IoT, and what separates it from basic machine-to-machine communication, is the intelligence. Smarter applications means smarter data means more efficiency. Many of these platforms are still in their infancies, but we’ve seen evidence of a strong groundswell bringing these to the forefront. Ultimately, if these four components can come together in the right way, the oil and gas industry will be able to reap the benefits. And, frankly, they will be reaping these benefits long before other industrially oriented markets. Aligning these needs is not easy, but the potential exists as long as oil and gas companies embrace the disruption and unify the data.
Diving Deep Into the Internet of Underwater Things
Much has been said and done regarding the Internet of Things (IoT) across the terrestrial and aerial environments – just look at the proliferation of robotics, drones and unmanned vehicles being used across the globe. But, what about our submarine world? Does the IoT only apply to systems above water?This week we are going to take a “deep dive” into the life aquatic and see what forms the IoT is taking underwater. As many scientists and researchers continue to demonstrate, there is much to be learned about life underwater, especially when it comes to the largest bodies of water on the planet – the seas and oceans. The development of an Internet of Underwater Things (IoUT) would certainly help make the discovery, recording and transmission of information a lot easier, especially if it would in turn be limiting the manual intervention of humans. Collecting and transmitting data throughout large bodies of water could enable a system of roaming, autonomous vehicles and underwater sensors, all communicating with each other and relaying information to networks above the surface. This could be used for a wide range of underwater tasks, from pipeline repairs and crash site surveys to seismic and ecological monitoring applications. As Richard Mills, director of sales at Norwegian AUV and marine robot developer Kongsberg Maritime, states in an interview with NauticExpo e-magazine, “there are an incredible number of possibilities for IoUT and autonomous underwater vehicles (AUVs). The technology has finite bounds, but new applications are only limited by our imagination.” Underwater Apps Bound by Tech Limits Before the IoUT can become a practical endeavor, engineers, scientists and researchers still have plenty of work to do to make it a reality. One of the biggest challenges surrounding the IoUT is the fact that underwater data communications are somewhat limited and unconventional as compared to the systems that work above water. The science behind underwater communications requires different thinking and technology requirements – for example, the electromagnetic waves used by conventional WiFi networks only travel a few centimeters in water. Furthermore, background noise from marine life and anthropogenic activity can also lead to signal interference. Also, the cost of implementing remotely operated vehicles (ROVs) comes at a significant cost as compared to autonomous underwater vehicles (AUVs), which looks to be the replacement in the near future. An AUV’s ability to function without manual human intervention is already a huge advantage and the cost of deploying an AUV is significantly lower than that of an ROV, while their autonomous nature minimizes the human effort needed during missions. As the IoUT develops, it will facilitate new ways for AUVs to interact with the subsea environment. Such vehicles increasingly will be used to harvest data from instruments on the seabed for scientific monitoring and surveying oilfield infrastructure, for example. With better submarine communications, the use of AUVs is already diversifying. There is an increasing number of deep-water and under-ice research projects, and new applications in defense and shallow-water seabed imagery rising to the surface. At FreeWave, we’ll be keeping a close eye on these developments as the possibilities for underwater IoT applications abound.